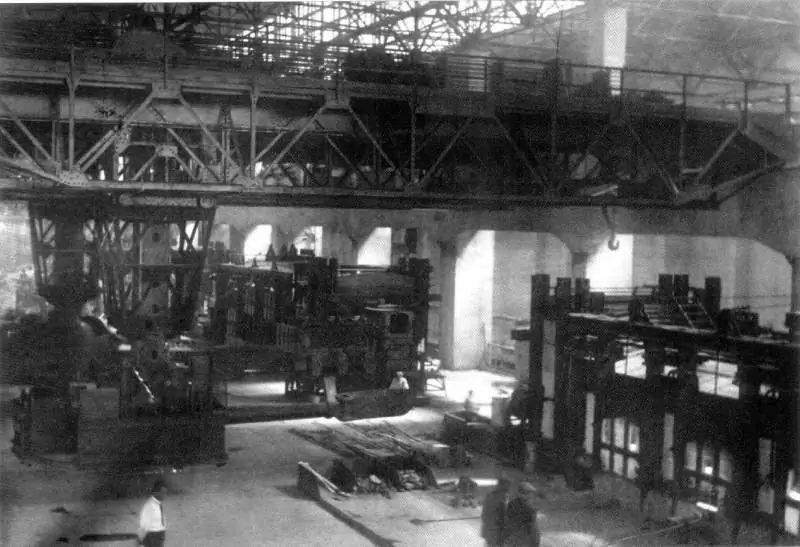
Recurso estratégico
Es difícil sobreestimar la producción de acero de alta calidad para el complejo militar-industrial en condiciones de guerra. Este es uno de los factores más importantes en el éxito de los ejércitos en el campo de batalla.
Como saben, los metalúrgicos de Krupp fueron de los primeros en aprender a producir acero de alta calidad para armas.
Los alemanes adoptaron el proceso de fabricación de Thomas a finales del siglo XIX. Este método de fundición de acero permitió eliminar las impurezas de fósforo del mineral, lo que automáticamente aumentó la calidad del producto. Las armaduras y el acero de alta calidad durante la Primera Guerra Mundial a menudo aseguraron la superioridad de los alemanes en el campo de batalla.
Para organizar tal producción, se requerían nuevos materiales refractarios, que revestían las superficies internas de los hornos. Los alemanes utilizaron los últimos refractarios de magnesita para su época, soportando temperaturas de más de 2000 grados. Tales sustancias de mayor refractariedad se basan en óxidos de magnesio con pequeñas mezclas de óxidos de aluminio.
A principios del siglo XX, los países con tecnologías para la producción en masa de refractarios de magnesita podían permitirse producir armaduras y cañones de armas de alta calidad. Esto se puede comparar con una ventaja estratégica.
Más bajos en términos de resistencia al fuego fueron los llamados materiales altamente refractarios que soportan temperaturas de 1750 a 1950 grados. Estos son refractarios de dolomita y alto contenido de alúmina. Los materiales refractarios de arcilla refractaria, semiácidos, de cuarzo y dinas pueden soportar temperaturas de 1610 a 1750 grados.
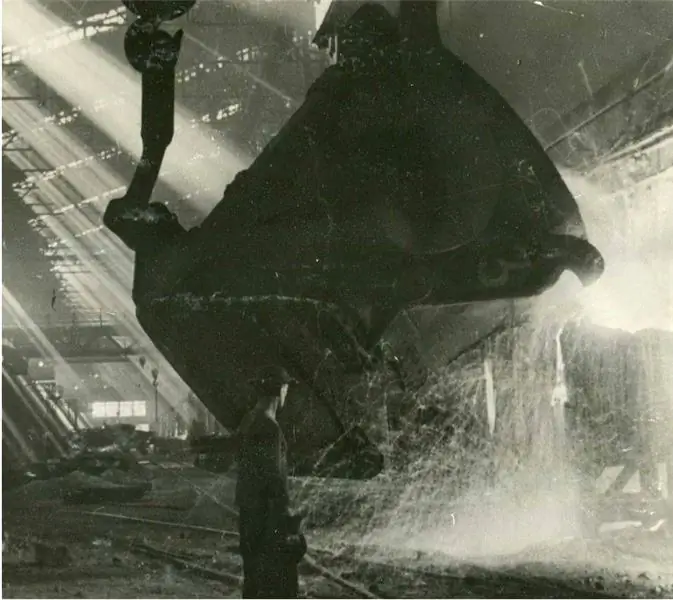
Por cierto, las tecnologías y los sitios para la producción de refractarios de magnesita aparecieron por primera vez en Rusia en 1900.
El ladrillo refractario de magnesita Satka en 1905 recibió una medalla de oro en la Exposición Industrial Mundial de Lieja. Se produjo cerca de Chelyabinsk en la ciudad de Satka, donde se encontraba un depósito de magnesita único.
El mineral periclasa, a partir del cual se fabricaban los refractarios en la fábrica, era de alta calidad y no requería enriquecimiento adicional. Como resultado, el refractario de magnesita de Satka fue superior a sus homólogos de Grecia y Austria.
Cerrando la brecha
A pesar del ladrillo de magnesita de bastante alta calidad de Satka, hasta los años 30, los principales refractarios de los metalúrgicos soviéticos eran materiales dinas de arcilla. Naturalmente, obtener una temperatura alta para fundir acero apto para armas no funcionó: el revestimiento del interior de los hornos de hogar abierto se desmoronó y requirió reparaciones extraordinarias.
No había suficientes ladrillos Satka y, en el período posrevolucionario, se perdieron las principales tecnologías de producción.
Al mismo tiempo, los europeos siguieron adelante; por ejemplo, la magnesita austriaca Radex se distinguió por una excelente resistencia al fuego.
La Unión Soviética compró este material. Pero era imposible conseguir un análogo sin un secreto de producción. Este problema fue abordado por un graduado de la Universidad Técnica Estatal de Moscú. NORDESTE. Bauman Alexey Petrovich Panarin. En la planta Magnet (anteriormente Satka Combine) en 1933 dirigió el Laboratorio Central de Plantas. Y cinco años después, lanzó la producción en masa de refractarios de periclasa-cromita o cromomagnesita para hornos de hogar abierto.
En la planta metalúrgica de Zlatoust y el martillo y la hoz de Moscú, el refractario de Panarin reemplazó a las obsoletas dinas.
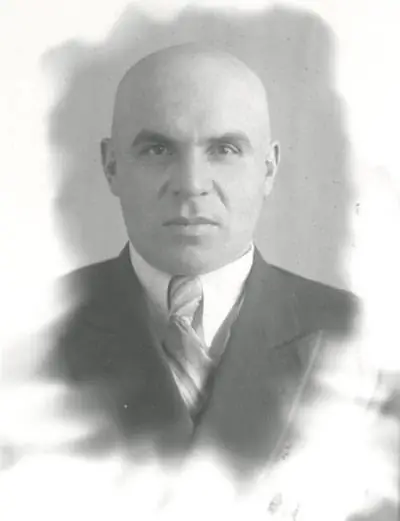
La tecnología, que se había desarrollado en el laboratorio de "Magnezit" durante varios años, consistía en una composición y tamaño de partícula especiales.
Anteriormente, la planta producía ladrillos convencionales de cromo-magnesita, que consistían en magnesita y mineral de hierro y cromo, en una proporción de 50/50. El secreto revelado por el grupo de Panarin fue el siguiente:
“Si se agrega mineral de cromita en granos granulométricos gruesos con un contenido mínimo de fracciones de menos de 0,5 mm a una carga de magnesita ordinaria, incluso con una adición del 10% de dicho mineral, la estabilidad térmica del ladrillo aumenta drásticamente.
A medida que aumenta la adición de mineral de cromita de granulometría gruesa, la estabilidad del ladrillo crece y alcanza un máximo en una cierta proporción de componentes.
Se extrajo cromita para el nuevo refractario en la mina Saranovskoye y se continuó extrayendo periclasa en Satka.
A modo de comparación, un ladrillo de magnesita "prerrevolucionario" ordinario resistió temperaturas de 5 a 6 veces menos que la novedad de Panarin.
En la planta de fundición de cobre de Kirovograd, el refractario de cromo-magnesita en el techo de un horno de reverberación resistió temperaturas de hasta 1550 grados durante 151 días. Anteriormente, los refractarios de dichos hornos debían cambiarse cada 20 a 30 días.
En 1941, se dominó la producción de refractarios a gran escala, lo que hizo posible el uso de los materiales en grandes hornos de fabricación de acero a temperaturas de hasta 1800 grados. Una contribución importante a esto fue hecha por el director técnico de "Magnezit" Alexander Frenkel, quien desarrolló un nuevo método para sujetar el material refractario a los techos de los hornos.
Refractarios por la victoria
A fines de 1941, los metalúrgicos de Magnitka lograron lo que antes era impensable: por primera vez en la historia dominaron la fundición de acero blindado para tanques T-34 en los principales hornos pesados de hogar abierto.
El principal proveedor de refractarios para un proceso tan importante fue Satka "Magnezit". Es innecesario hablar de las dificultades de la guerra, cuando un tercio de los obreros de las fábricas fueron llamados al frente y el Estado exigió que el plan se cumpliera en exceso. Sin embargo, la planta estaba haciendo su trabajo, y Panarin en 1943
"Por dominar la producción de productos altamente refractarios a partir de materias primas locales para la metalurgia ferrosa"
fue galardonado con el Premio Stalin.
En 1944, este metalúrgico-investigador desarrollará una tecnología para la producción de polvo de magnesita de alta calidad "Extra". Este producto semiacabado se utilizó para preparar un refractario prensado utilizado en la producción especialmente importante de acero blindado en hornos eléctricos. El límite de temperatura para tales refractarios alcanzó los 2000 grados.
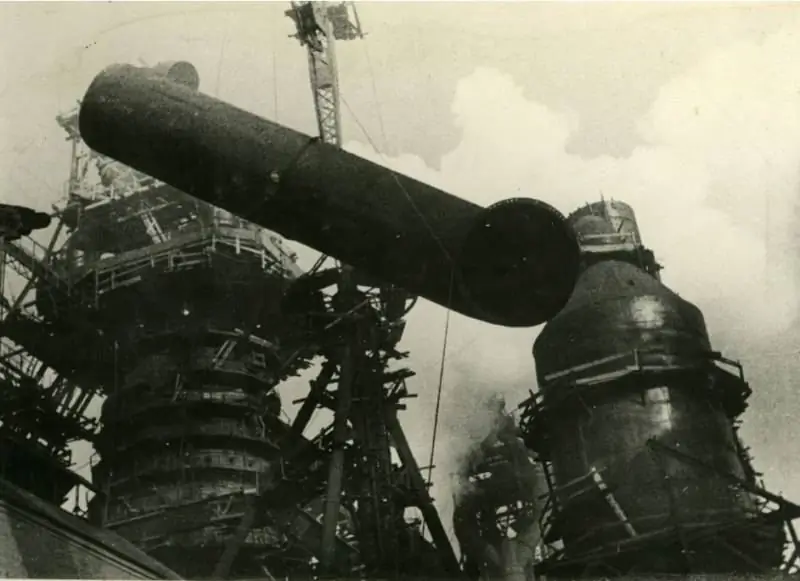
Pero no se debe suponer que el ejemplo de una planta Magnezit generalmente exitosa se extendió a toda la industria refractaria de la Unión Soviética.
Una situación particularmente difícil se desarrolló en los Urales, donde prácticamente toda la construcción de tanques del país fue evacuada en 1941-1942.
Las plantas metalúrgicas de Magnitogorsk y Novotagilsk se reorientaron hacia la producción de armaduras, suministrando productos a Sverdlovsk Uralmash, Chelyabinsk "Tankograd" y la planta de tanques Nizhny Tagil No. 183. Al mismo tiempo, las plantas metalúrgicas tenían su propia producción de refractarios a partir de materias primas locales.
Por ejemplo, en Magnitka, la planta de dinas-chamotte producía entre 65 y 70 mil toneladas de ladrillos por año. Esto no fue suficiente ni siquiera para sus propias necesidades, por no mencionar el suministro a otras empresas.
Las primeras dificultades surgieron cuando las fábricas de tanques comenzaron a construir sus propios hornos térmicos y de calefacción. La metalurgia de los Urales ya apenas tenía refractarios suficientes, y luego la producción de cascos de las fábricas de tanques requería materiales de alta calidad para revestir los hornos.
No se habló de refractarios de cromomagnesita aquí; este material escaseaba e incluso se exportaba a cambio de American Lend-Lease. Al menos esto se menciona en varias fuentes. Los historiadores de los Urales escriben que la costosa cromomagnesita de Panarin podría ir al extranjero a cambio de escasas ferroaleaciones por blindaje de tanques. Pero aún no hay evidencia directa de esto.
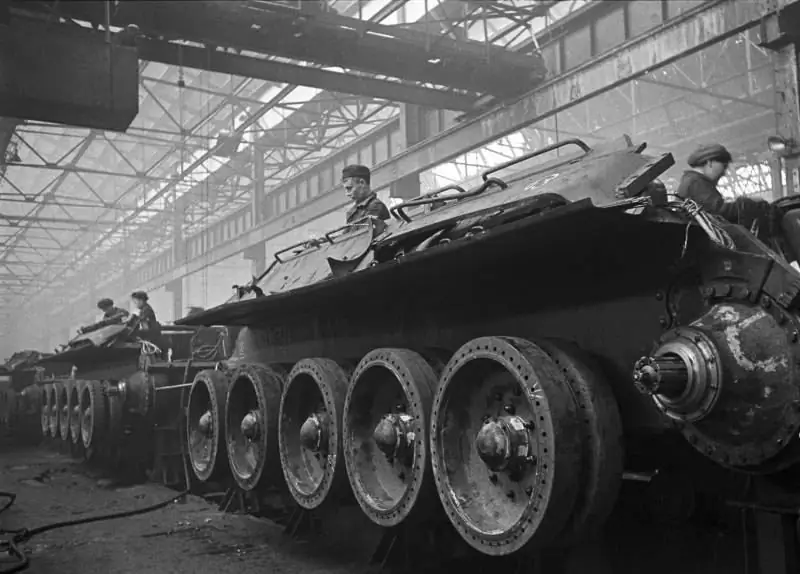
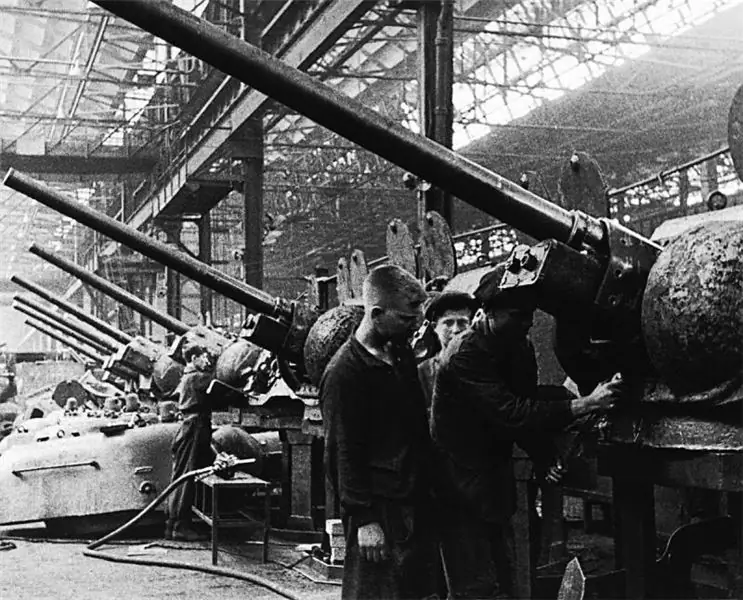
Las fábricas de tanques se basaban principalmente en material refractario dinas producido por la planta de Pervouralsk. Pero, en primer lugar, solo se producían 12 mil toneladas por mes y, en segundo lugar, los metalúrgicos se llevaban la mayor parte.
La expansión de la producción en la planta de Pervouralsk fue muy lenta. Y a mediados de 1942, solo aparecieron 4 nuevos hornos. El resto no estaba listo o, en general, solo existía en proyectos.
Los refractarios para hornos de hogar abierto de fábricas de tanques a menudo eran de mala calidad, no estaban completos y en el momento equivocado. Solo para la reparación de los hornos de Uralmash en el cuarto trimestre de 1942, se requirieron 1035 toneladas de ladrillos resistentes al fuego y solo se recibieron alrededor de 827 toneladas.
En 1943, el taller de hogar abierto de Uralmash, en general, casi se detuvo debido a la falta de refractarios para reparar.
La calidad de los refractarios suministrados durante la guerra dejó mucho que desear. Si en condiciones normales el ladrillo dinas del horno de hogar abierto podía soportar 400 calores, en tiempo de guerra no excedía los 135 calores. Y en marzo de 1943, este parámetro se había reducido a 30-40 calores.
Esta situación demuestra claramente cómo la falta de un recurso (en este caso, refractario) puede ralentizar seriamente el trabajo de toda la industria de defensa. Como escribe el candidato de ciencias históricas Nikita Melnikov en sus obras, en marzo de 1943, tres hornos de hogar abierto de Uralmash todavía se detuvieron y llevaron a cabo un ciclo completo de trabajos de reparación. Se necesitaron 2346 toneladas de dinas, 580 toneladas de chamota y 86 toneladas de escasa magnesita.
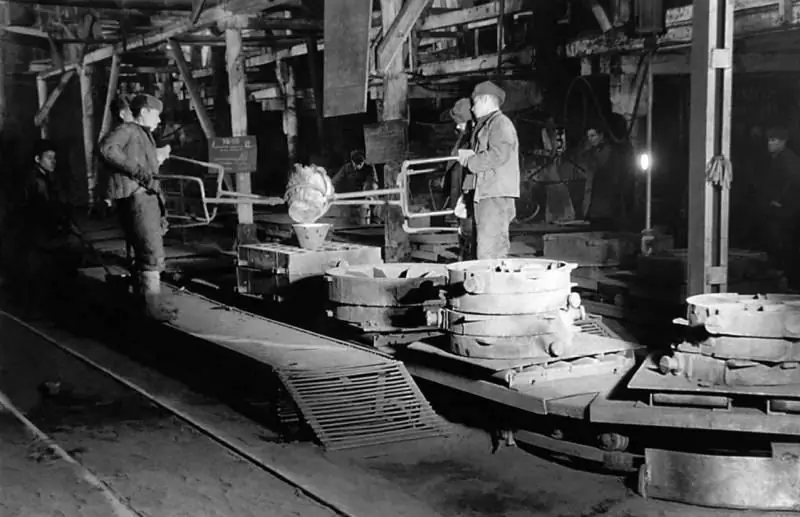
A mediados de 1942, en la planta de tanques No. 183, la situación se estaba desarrollando de manera similar: la producción de acero estaba rezagada con respecto al ensamblaje mecánico. Y tuvimos que "importar" los cascos del T-34 de Uralmash.
Una de las razones fue la falta de refractarios para la reparación de hornos de hogar abierto, que en la primavera de 1942 estaban funcionando al límite. Como resultado, solo 2 de los 6 hornos de hogar abierto estuvieron en funcionamiento en el otoño. Los volúmenes de fundición se restauraron solo en la segunda mitad de 1943.
La situación de los refractarios en la estructura del complejo de defensa soviético durante la Gran Guerra Patria ilustra claramente la complejidad de la situación en la retaguardia del país.
Una escasez crónica de, en general, no el producto más de alta tecnología afectó directamente el ritmo de producción de vehículos blindados.