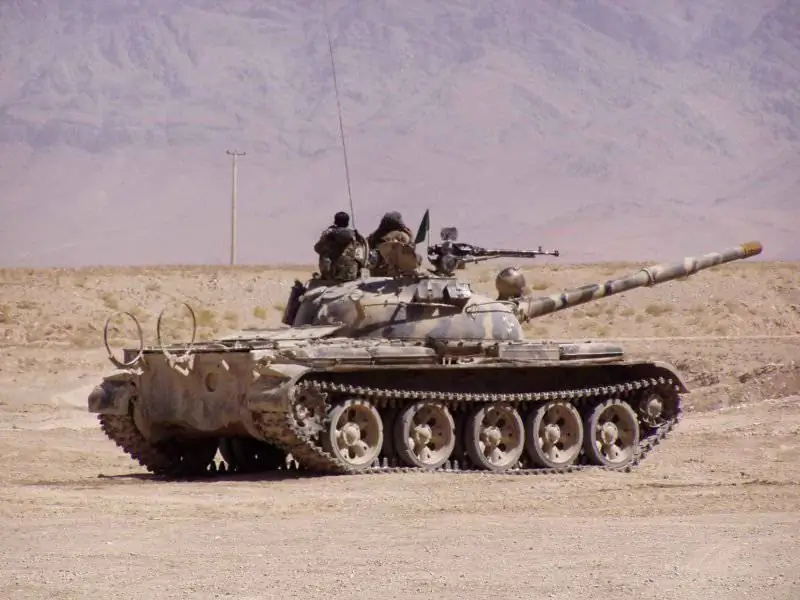
En 1955, el gobierno tomó la decisión de crear una oficina de diseño para la ingeniería diesel especial en la planta de ingeniería de transporte de Jarkov y crear un nuevo motor diesel de tanque. El profesor A. D. Charomsky fue nombrado diseñador jefe de la oficina de diseño.

La elección del esquema de diseño del futuro motor diesel se determinó principalmente por la experiencia de trabajar en motores diesel de 2 tiempos OND TsIAM y el motor U-305, así como por el deseo de cumplir con los requisitos de los diseñadores del nuevo T -64 tanque, desarrollado en esta planta bajo el liderazgo del diseñador jefe AA … Morozov: para asegurar las dimensiones mínimas del motor diesel, especialmente en altura, en combinación con la posibilidad de colocarlo en el tanque en una posición transversal entre las cajas de engranajes planetarios a bordo. Se eligió un esquema diésel de dos tiempos con una disposición horizontal de cinco cilindros con pistones que se mueven de manera opuesta en ellos. Se decidió fabricar un motor con inflado y aprovechamiento de la energía de los gases de escape en una turbina.
¿Cuál fue el motivo de la elección de un motor diésel de 2 tiempos?
Anteriormente, en las décadas de 1920 y 1930, la creación de un motor diesel de 2 tiempos para vehículos de aviación y terrestres se vio frenada debido a muchos problemas no resueltos que no pudieron superarse con el nivel de conocimiento, experiencia y capacidades de la industria nacional acumulada por ese momento.
El estudio y la investigación de los motores diésel de 2 tiempos de algunas empresas extranjeras llevaron a la conclusión sobre la gran dificultad de dominarlos en la producción. Así, por ejemplo, un estudio realizado por el Instituto Central de Motores de Aviación (CIAM) en los años 30 del motor diesel Jumo-4 diseñado por Hugo Juneckers mostró problemas significativos asociados con el desarrollo de dichos motores en la producción de dichos motores por parte de los nacionales. industria de ese período. También se conoció que Inglaterra y Japón, habiendo comprado una licencia para este motor diesel, sufrieron fallas en el desarrollo del motor Junkers. Al mismo tiempo, en los años 30 y 40, ya se realizaron trabajos de investigación en motores diesel de 2 tiempos en nuestro país y se fabricaron muestras experimentales de dichos motores. El protagonismo en estos trabajos correspondió a los especialistas del CIAM y, en particular, a su Departamento de Motores de Aceite (OND). CIAM diseñó y fabricó muestras de motores diesel de 2 tiempos de varias dimensiones: OH-2 (12/16, 3), OH-16 (11/14), OH-17 (18/20), OH-4 (8 / 9) y varios otros motores originales.
Entre ellos se encontraba el motor FED-8, diseñado bajo la dirección de destacados científicos de motores B. S. Stechkin, N. R. Briling, A. A. Bessonov. Se trataba de un motor diésel de avión de 2 tiempos y 16 cilindros en forma de X con distribución de gas válvula-pistón, con una dimensión de 18/23, que desarrollaba una potencia de 1470 kW (2000 CV). Uno de los representantes de los motores diesel de 2 tiempos con sobrealimentación es un motor diesel turbo-pistón de 6 cilindros en forma de estrella con una capacidad de 147 … 220 kW (200 … 300 hp) fabricado en el CIAM bajo el liderazgo de BS Stechkin. La potencia de la turbina de gas se transmitía al cigüeñal a través de una caja de cambios adecuada.
La decisión tomada entonces al crear el motor FED-8 en términos de la idea en sí y el esquema de diseño representó un importante paso adelante. Sin embargo, el proceso de trabajo y especialmente el proceso de intercambio de gases a un alto grado de presurización y soplado en bucle no se han elaborado de forma preliminar. Por lo tanto, el diesel FED-8 no recibió más desarrollo y en 1937 se interrumpió el trabajo en él.
Después de la guerra, la documentación técnica alemana pasó a ser propiedad de la URSS. Ella cae en A. D. Charomsky como desarrollador de motores de aviones, y está interesado en la maleta de Junkers.
La maleta de Junkers: una serie de motores de turbo pistón de dos tiempos para aviones Jumo 205 con pistones de movimiento opuesto se creó a principios de los años 30 del siglo XX. Las características del motor Jumo 205-C son las siguientes: 6 cilindros, 600 CV. carrera 2 x 160 mm, cilindrada 16,62 litros, relación de compresión 17: 1, a 2200 rpm
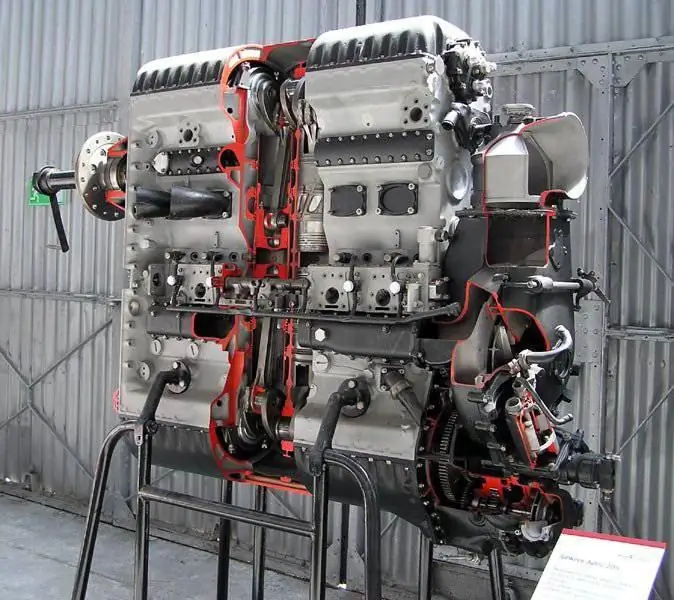
Motor Jumo 205
Durante la guerra, se produjeron alrededor de 900 motores, que se utilizaron con éxito en hidroaviones Do-18, Do-27 y más tarde en barcos de alta velocidad. Poco después del final de la Segunda Guerra Mundial en 1949, se decidió instalar dichos motores en los barcos patrulleros de Alemania Oriental, que estuvieron en servicio hasta los años 60.
Sobre la base de estos desarrollos, AD Charomsky en 1947 en la URSS creó un avión diesel de dos tiempos M-305 y un compartimiento monocilíndrico de este motor U-305. Este motor diesel desarrolló una potencia de 7350 kW (10,000 hp) con un bajo peso específico (0,5 kg / h.p.) y un bajo consumo específico de combustible -190 g / kWh (140 g / h.p.h). Se adoptó una disposición en forma de X de 28 cilindros (cuatro bloques de 7 cilindros). La dimensión del motor se eligió igual a 12/12. Un turbocompresor conectado mecánicamente al eje diesel proporcionaba un gran impulso. Para comprobar las principales características establecidas en el proyecto M-305, para elaborar el proceso de trabajo y el diseño de piezas, se construyó un modelo experimental del motor, que contaba con el índice U-305. G. V. Orlova, N. I. Rudakov, L. V. Ustinova, N. S. Zolotarev, S. M. Shifrin, N. S. Sobolev, así como tecnólogos y trabajadores de la planta piloto del CIAM y el taller de la OND.
El proyecto de la aeronave full size diesel M-305 no se implementó, ya que el trabajo del CIAM, como toda la industria aeronáutica del país, en ese momento ya estaba enfocado en el desarrollo de motores turborreactores y turbohélice y la necesidad de un Desapareció el motor diesel de 10,000 caballos de fuerza para la aviación.
Los indicadores altos obtenidos en el motor diesel U-305: potencia del motor en litros 99 kW / l (135 hp / l), potencia en litros de un cilindro de casi 220 kW (300 hp) a una presión de sobrealimentación de 0.35 MPa; alta velocidad de rotación (3500 rpm) y datos de una serie de pruebas exitosas a largo plazo del motor: confirmaron la posibilidad de crear un motor diésel de 2 tiempos de tamaño pequeño eficaz para fines de transporte con indicadores y elementos estructurales similares.
En 1952, el laboratorio No. 7 (ex OND) del CIAM fue transformado por decisión del gobierno en el Laboratorio de Investigación de Motores (NILD) con su subordinación al Ministerio de Ingeniería de Transporte. Un grupo de iniciativa de empleados - especialistas altamente calificados en motores diesel (G. V. Orlova, N. I. Rudakov, S. M. Shifrin, etc.), encabezados por el profesor A. D. Charomsky, ya están en el NILD (más tarde - NIID). En el ajuste fino y la investigación de el motor U-305 de 2 tiempos.
Diésel 5TDF
En 1954, A. D. Charomsky hizo una propuesta al gobierno para crear un motor diesel de tanque de 2 tiempos. Esta propuesta coincidió con el requisito del diseñador jefe del nuevo tanque A. A. Morozov y A. D. Charomsky fue nombrado diseñador jefe de la planta. V. Malyshev en Jarkov.
Dado que la oficina de diseño de motores de tanque de esta planta permaneció principalmente en Chelyabinsk, A. D. Charomsky tuvo que formar una nueva oficina de diseño, crear una base experimental, establecer una producción piloto y en serie y desarrollar tecnología que la planta no tenía. El trabajo comenzó con la fabricación de una unidad monocilíndrica (OTsU), similar al motor U-305. En la OTsU, se estaban elaborando los elementos y procesos del futuro motor diesel de tanque de tamaño completo.
Los principales participantes en este trabajo fueron A. D. Charomsky, G. A. Volkov, L. L. Golinets, B. M. Kugel, M. A., Meksin, I. L. Rovensky y otros.
En 1955, los empleados de NILD se unieron al trabajo de diseño en la planta de diesel: G. V. Orlova, N. I. Rudakov, V. G. Lavrov, I. S. Elperin, I. K. Lagovsky y otros especialistas de NILD L. M. Belinsky, LI Pugachev, LSRoninson, SM Shifrin llevaron a cabo un trabajo experimental en la OTsU en la planta de ingeniería de transporte de Jarkov. Así es como aparece el 4TPD soviético. Era un motor que funcionaba, pero con un inconveniente: la potencia era de poco más de 400 hp, lo que no era suficiente para un tanque. Charomsky pone otro cilindro y obtiene 5TD.
La introducción de un cilindro adicional ha cambiado seriamente la dinámica del motor. Surgió un desequilibrio que provocó intensas vibraciones de torsión en el sistema. Las principales fuerzas científicas de Leningrado (VNII-100), Moscú (NIID) y Jarkov (KhPI) están involucradas en su solución. 5TDF fue puesto a condición EXPERIMENTALMENTE, por ensayo y error.
La dimensión de este motor se eligió igual a 12/12, es decir lo mismo que en el motor U-305 y OTsU. Para mejorar la respuesta del acelerador del motor diesel, se decidió conectar mecánicamente la turbina y el compresor al cigüeñal.
Diesel 5TD tenía las siguientes características:
- alta potencia: 426 kW (580 hp) con dimensiones generales relativamente pequeñas;
- mayor velocidad - 3000 rpm;
- eficiencia de presurización y utilización de la energía de los gases residuales;
- baja altura (menos de 700 mm);
- una disminución del 30-35% en la transferencia de calor en comparación con los motores diésel de 4 tiempos (aspiración natural) existentes y, en consecuencia, un volumen menor requerido para el sistema de refrigeración de la central eléctrica;
- eficiencia de combustible satisfactoria y capacidad para operar el motor no solo con combustible diesel, sino también con queroseno, gasolina y sus diversas mezclas;
- Toma de fuerza de ambos extremos y su longitud relativamente pequeña, lo que permite montar el tanque MTO con una disposición transversal de un motor diesel entre dos cajas de cambios a bordo en un volumen ocupado mucho menor que con una disposición longitudinal de el motor y la caja de cambios central;
- Colocación exitosa de unidades tales como un compresor de aire de alta presión con sus propios sistemas, un generador de arranque, etc.
Habiendo conservado la disposición transversal del motor con una toma de fuerza bidireccional y dos transmisiones planetarias a bordo ubicadas a ambos lados del motor, los diseñadores cambiaron a los lugares vacantes en los lados del motor, paralelos a las cajas de cambios., el compresor y la turbina de gas, previamente montados en 4TD encima del bloque motor. El nuevo diseño permitió reducir a la mitad el volumen de MTO en comparación con el tanque T-54, y se excluyeron componentes tradicionales como la caja de cambios central, la caja de cambios, el embrague principal, los mecanismos de giro planetario a bordo, los mandos finales y los frenos. Como se señaló más adelante en el informe de GBTU, el nuevo tipo de transmisión ahorró 750 kg de masa y constaba de 150 piezas mecanizadas en lugar de las 500 anteriores.
Todos los sistemas de servicio del motor estaban interconectados por encima del motor diesel, formando el "segundo piso" del MTO, cuyo esquema se denominó "dos niveles".
El alto rendimiento del motor 5TD requirió el uso de una serie de nuevas soluciones fundamentales y materiales especiales en su diseño. El pistón de este diésel, por ejemplo, se fabricó con una almohadilla térmica y un espaciador.
El primer anillo de pistón fue un anillo de llama de tipo labio continuo. Los cilindros eran de acero cromado.
La capacidad de operar el motor con una alta presión de flash fue proporcionada por el circuito de potencia del motor con pernos de acero de soporte, un bloque de aluminio fundido descargado por la acción de las fuerzas del gas y la ausencia de una junta de gas. La mejora del proceso de purga y llenado de los cilindros (y este es un problema para todos los motores diésel de 2 tiempos) fue facilitada en cierta medida por el esquema de dinámica de gas que utiliza la energía cinética de los gases de escape y el efecto de eyección.
El sistema de formación de la mezcla chorro-vórtice, en el que la naturaleza y la dirección de los chorros de combustible se coordinan con la dirección del movimiento del aire, aseguró una turbulización eficaz de la mezcla aire-combustible, lo que contribuyó a mejorar el proceso de transferencia de calor y masa.
La forma especialmente seleccionada de la cámara de combustión también permitió mejorar el proceso de mezcla y combustión. Las tapas de los cojinetes principales se juntaron con el cárter mediante pernos de potencia de acero, tomando la carga de las fuerzas del gas que actúan sobre el pistón.
Una placa con una turbina y una bomba de agua se unió a un extremo del bloque del cárter, y una placa de la transmisión principal y cubiertas con transmisiones al sobrealimentador, regulador, sensor de tacómetro, compresor de alta presión y distribuidor de aire se unieron al lado opuesto. fin.
En enero de 1957, se preparó el primer prototipo del motor diesel tanque 5TD para pruebas en banco. Al final de las pruebas de banco, el 5TD en el mismo año fue transferido para pruebas de objetos (mar) en un tanque experimental "Objeto 430", y en mayo de 1958 pasó las pruebas estatales interdepartamentales con una buena nota.
Sin embargo, se decidió no transferir el diésel 5TD a la producción en masa. La razón fue nuevamente el cambio en los requisitos de los militares para nuevos tanques, que una vez más requirieron un aumento en el poder. Teniendo en cuenta los altísimos indicadores técnicos y económicos del motor 5TD y las reservas inherentes al mismo (que también fueron demostradas por las pruebas), una nueva planta de energía con una capacidad de unos 700 CV. decidió crear sobre su base.
La creación de un motor tan original para la planta de ingeniería de transporte de Jarkov requirió la fabricación de equipos tecnológicos significativos, una gran cantidad de prototipos de un motor diesel y pruebas repetidas a largo plazo. Debe tenerse en cuenta que el departamento de diseño de la planta se convirtió más tarde en la Oficina de Diseño de Ingeniería Mecánica de Jarkov (KHKBD), y la producción de motores se creó prácticamente desde cero después de la guerra.
Simultáneamente con el diseño del motor diesel, se creó en la planta un gran complejo de stands experimentales y varias instalaciones (24 unidades) para probar los elementos de su diseño y flujo de trabajo. Esto ayudó en gran medida a verificar y resolver los diseños de unidades tales como un sobrealimentador, una turbina, una bomba de combustible, un colector de escape, una centrífuga, bombas de agua y aceite, un bloque de cárter, etc., sin embargo, su desarrollo continuó.
En 1959, a petición del diseñador jefe del nuevo tanque (AA Morozov), para quien se diseñó este motor diésel para tal fin, se consideró necesario aumentar su potencia de 426 kW (580 hp) a 515 kW (700 hp).). La versión forzada del motor se denominó 5TDF.
Al aumentar la velocidad del compresor de refuerzo, se incrementó la potencia en litros del motor. Sin embargo, como resultado de forzar el motor diesel, aparecieron nuevos problemas, principalmente en la confiabilidad de los componentes y conjuntos.
Los diseñadores de KhKBD, NIID, VNIITransmash, tecnólogos de la planta y los institutos VNITI y TsNITI (desde 1965) han llevado a cabo una gran cantidad de trabajo de cálculo, investigación, diseño y tecnología para lograr la confiabilidad y el tiempo de operación requeridos del motor diesel 5TDF..
Los problemas más difíciles resultaron ser los problemas de aumento de la confiabilidad del grupo de pistones, el equipo de combustible y el turbocompresor. Todas las mejoras, incluso insignificantes, se obtuvieron solo como resultado de una amplia gama de medidas de diseño, tecnológicas y organizativas (de producción).
El primer lote de motores diesel 5TDF se caracterizó por una gran inestabilidad en la calidad de las piezas y ensamblajes. Una parte de los motores diésel de la serie producida (lote) han acumulado el tiempo de funcionamiento de garantía establecido (300 horas). Al mismo tiempo, una parte importante de los motores se retiraron de los stands antes del tiempo de funcionamiento de la garantía debido a ciertos defectos.
La especificidad de un motor diesel de 2 tiempos de alta velocidad radica en un sistema de intercambio de gases más complejo que en un 4 tiempos, mayor consumo de aire y una mayor carga de calor del grupo de pistones. Por lo tanto, rigidez y resistencia a las vibraciones de la estructura, observancia más estricta de la forma geométrica de varias partes, altas propiedades anti-agarrotamiento y resistencia al desgaste de los cilindros, resistencia al calor y resistencia mecánica de los pistones, suministro cuidadoso de dosificación y remoción del lubricante del cilindro y Se requería una mejora en la calidad de las superficies de fricción. Para tener en cuenta estas características específicas de los motores de 2 tiempos, fue necesario resolver problemas complejos de diseño y tecnológicos.
Una de las partes más críticas que proporciona una distribución precisa del gas y la protección de los anillos de sellado del pistón contra el sobrecalentamiento fue un anillo de llama tipo manguito de acero roscado de paredes delgadas con un revestimiento especial antifricción. En el refinamiento del motor diesel 5TDF, el problema de la operatividad de este anillo se ha convertido en uno de los principales. En el proceso de ajuste fino, durante mucho tiempo, se produjeron raspaduras y roturas de los anillos de llama debido a la deformación de su plano de soporte, configuración subóptima tanto del anillo como del cuerpo del pistón, cromado insatisfactorio de los anillos, lubricación insuficiente, suministro desigual de combustible por toberas, desconchado de incrustaciones y deposición de sales formadas en el revestimiento del pistón, así como por desgaste de polvo asociado con un grado insuficiente de limpieza del aire aspirado por el motor.
Solo como resultado del largo y arduo trabajo de muchos especialistas de la planta e institutos de investigación y tecnología, a medida que se mejora la configuración del pistón y el anillo de llama, se mejora la tecnología de fabricación, se mejoran los elementos del equipo de combustible, el se mejoró la lubricación, se eliminaron prácticamente el uso de recubrimientos antifricción más efectivos, así como el refinamiento del sistema de limpieza de aire, los defectos asociados con el funcionamiento del anillo de llama.
Las averías de los anillos de pistón trapezoidales, por ejemplo, se eliminaron reduciendo el juego axial entre el anillo y la ranura del pistón, mejorando el material, cambiando la configuración de la sección transversal del anillo (cambiado de trapezoidal a rectangular) y perfeccionando la tecnología. para fabricar los anillos. Las fracturas de los pernos del revestimiento del pistón se han reparado volviendo a roscar y bloqueando, ajustando los controles de fabricación, ajustando los límites de torsión y utilizando un material de perno mejorado.
La estabilidad del consumo de aceite se logró aumentando la rigidez de los cilindros, reduciendo el tamaño de los recortes en los extremos de los cilindros, apretando el control en la fabricación de anillos colectores de aceite.
Al ajustar los elementos del equipo de combustible y mejorar el intercambio de gases, se obtuvo alguna mejora en la eficiencia del combustible y una disminución en la presión de flash máxima.
Al mejorar la calidad del caucho utilizado y simplificar el espacio entre el cilindro y el bloque, se eliminaron los casos de fugas de refrigerante a través de los anillos de sellado de caucho.
En relación con un aumento significativo en la relación de transmisión del cigüeñal al sobrealimentador, algunos motores diésel 5TDF revelaron defectos tales como deslizamiento y desgaste de los discos de embrague de fricción, averías de la rueda del sobrealimentador y fallas de sus cojinetes, que estaban ausentes en el motor. Motor diesel 5TD. Para eliminarlos, fue necesario tomar medidas como seleccionar el apriete óptimo del paquete de discos de embrague de fricción, aumentar el número de discos en el paquete, eliminar los concentradores de tensión en el impulsor del sobrealimentador, hacer vibrar la rueda, aumentar las propiedades de amortiguación de el soporte y la selección de mejores rodamientos. Esto permitió eliminar los defectos resultantes de forzar el motor diesel en términos de potencia.
El aumento de la fiabilidad y el tiempo de funcionamiento del motor diésel 5TDF ha contribuido en gran medida al uso de aceites de mayor calidad con aditivos especiales.
En los stands de VNIITransmash, con la participación de los empleados de KKBD y NIID, se llevó a cabo una gran cantidad de investigación sobre el funcionamiento del motor diesel 5TDF en condiciones de polvo real del aire de admisión. Finalmente, culminaron con una prueba exitosa de "polvo" del motor durante 500 horas de funcionamiento. Esto confirmó el alto grado de desarrollo del grupo cilindro-pistón del motor diesel y del sistema de limpieza de aire.
Paralelamente al ajuste fino del diésel en sí, se probó repetidamente junto con los sistemas de la planta de energía. Al mismo tiempo, se estaban mejorando los sistemas, se estaba resolviendo el tema de su interconexión y operación confiable en el tanque.
L. L. Golinets fue el diseñador jefe del KHKBD en el período decisivo de puesta a punto del motor diésel 5TDF. El ex diseñador jefe A. D. Charomsky se retiró y continuó participando en la puesta a punto como consultor.
El desarrollo de la producción en serie del motor diesel 5TDF en nuevos talleres de la planta especialmente construidos, con nuevos cuadros de trabajadores e ingenieros que estudiaron en este motor, provocó muchas dificultades, la participación de especialistas de otras organizaciones.
Hasta 1965, el motor 5TDF se produjo en series separadas (lotes). Cada serie posterior incluyó una serie de medidas desarrolladas y probadas en las gradas, eliminando los defectos identificados durante las pruebas y durante la operación de prueba en el ejército.
Sin embargo, el tiempo de funcionamiento real de los motores no superó las 100 horas.
Un avance significativo en la mejora de la fiabilidad del diésel tuvo lugar a principios de 1965. Para entonces, se habían realizado una gran cantidad de cambios en el diseño y la tecnología de su fabricación. Introducidos en producción, estos cambios permitieron aumentar el tiempo de funcionamiento de la siguiente serie de motores hasta 300 horas. Las pruebas de funcionamiento a largo plazo de tanques con motores de esta serie confirmaron la confiabilidad significativamente mayor de los motores diesel: todos los motores durante estas pruebas funcionaron 300 horas, y algunos de ellos (selectivamente), continuando las pruebas, funcionaron 400 … 500 horas cada uno.
En 1965, finalmente se lanzó un lote de instalación de motores diesel de acuerdo con la documentación y la tecnología del dibujo técnico corregido para la producción en masa. En 1965 se fabricaron un total de 200 motores en serie. El aumento de la producción comenzó, alcanzando su punto máximo en 1980. En septiembre de 1966, el motor diesel 5TDF pasó las pruebas interdepartamentales.
Teniendo en cuenta la historia de la creación del motor diésel 5TDF, cabe destacar el avance de su desarrollo tecnológico como motor completamente nuevo para la producción de la planta. Casi simultáneamente con la fabricación de prototipos del motor y su refinamiento de diseño, se llevó a cabo su desarrollo tecnológico y la construcción de nuevas instalaciones de producción de la planta y su terminación con equipamiento.
De acuerdo con los dibujos revisados de las primeras muestras de motores, ya en 1960, comenzó el desarrollo de la tecnología de diseño para la fabricación de 5TDF y, en 1961, comenzó la producción de documentación tecnológica de trabajo. Las características de diseño de un motor diesel de 2 tiempos, el uso de nuevos materiales, la alta precisión de sus componentes individuales y requirieron que la tecnología utilizara métodos fundamentalmente nuevos en el procesamiento e incluso el ensamblaje del motor. El diseño de los procesos tecnológicos y sus equipos se llevó a cabo tanto por los servicios tecnológicos de la planta, encabezados por A. I. Isaev, V. D. Dyachenko, V. I. Doschechkin y otros, como por empleados de los institutos tecnológicos de la industria. Especialistas del Instituto Central de Investigación de Materiales (director F. A. Kupriyanov) participaron en la resolución de muchos problemas de ciencia metalúrgica y de materiales.
La construcción de nuevos talleres para la producción de motores de la planta de ingeniería de transporte de Jarkov se llevó a cabo de acuerdo con el proyecto del Instituto Soyuzmashproekt (ingeniero jefe de proyectos S. I. Shpynov).
Durante 1964-1967. la nueva producción de diesel se completó con el equipo (especialmente máquinas especiales, más de 100 unidades), sin el cual sería prácticamente imposible organizar la producción en serie de piezas de diesel. Se trataba de máquinas taladradoras con diamante y multihusillos para el procesamiento de bloques, máquinas especiales de torneado y acabado para el procesamiento de cigüeñales, etc. Antes de la puesta en marcha de nuevos talleres y áreas de prueba y la depuración de la tecnología de fabricación para una serie de piezas principales, así como la fabricación de lotes de instalación y la primera serie del motor, los cascos de las grandes locomotoras diesel se organizaron temporalmente en la producción. sitios.
La puesta en servicio de las principales capacidades de la nueva producción de diésel se llevó a cabo alternativamente en el período 1964-1967. En los nuevos talleres, se brindó un ciclo completo de producción de diesel 5TDF, a excepción de la producción en blanco ubicada en el sitio principal de la planta.
Al formar nuevas instalaciones de producción, se prestó mucha atención a elevar el nivel y la organización de la producción. La producción de un motor diesel se organizó de acuerdo con el principio de línea y grupo, teniendo en cuenta los últimos logros de ese período en esta área. Se utilizaron los medios más avanzados de mecanización y automatización del procesamiento y ensamblaje de piezas, lo que aseguró la creación de una producción completamente mecanizada del motor diesel 5TDF.
En el proceso de formación de la producción, se llevó a cabo un gran trabajo conjunto de tecnólogos y diseñadores para mejorar la fabricabilidad del diseño del motor diesel, durante el cual los tecnólogos emitieron alrededor de seis mil propuestas al KHKBD, una parte significativa de las cuales se reflejó en el documentación de diseño del motor.
En términos del nivel técnico, la nueva producción de diesel superó significativamente los indicadores de las empresas de la industria que producían productos similares logrados en ese momento. El factor de equipamiento de los procesos de producción de diesel 5TDF ha alcanzado un alto valor - 6, 22. En sólo 3 años se han desarrollado más de 10 mil procesos tecnológicos, se han diseñado y fabricado más de 50 mil equipos. Varias empresas del Consejo Económico de Jarkov participaron en la fabricación de equipos y herramientas para ayudar a la planta de Malyshev.
En los años siguientes (después de 1965), ya en el curso de la producción en serie del motor diesel 5TDF, los servicios tecnológicos de la planta y TsNITI llevaron a cabo trabajos para mejorar aún más las tecnologías con el fin de reducir la intensidad del trabajo, mejorar la calidad y confiabilidad del motor. Empleados de TsNITI (director Ya. A. Shifrin, ingeniero jefe B. N. Surnin) durante 1967-1970. Se han desarrollado más de 4500 propuestas tecnológicas, proporcionando una reducción de la intensidad laboral en más de 530 horas estándar y una reducción significativa de las pérdidas por chatarra durante la producción. Al mismo tiempo, estas medidas permitieron reducir a más de la mitad el número de operaciones de montaje y unión selectiva de piezas. El resultado de la implementación de un complejo de diseño y medidas tecnológicas fue un funcionamiento más confiable y de alta calidad del motor en funcionamiento con un tiempo de funcionamiento garantizado de 300 horas. Pero el trabajo de los tecnólogos de la planta y TsNITI, junto con los diseñadores del KHKBD, continuó. Fue necesario aumentar el tiempo de funcionamiento del motor 5TDF en 1,5 … 2,0 veces. Esta tarea también está resuelta. El motor diesel de tanque de 2 tiempos 5TDF se modificó y se puso en producción en la planta de ingeniería de transporte de Jarkov.
El director de la planta, O. A. Soich, desempeñó un papel muy importante en la organización de la producción de diesel 5TDF, así como varios líderes de la industria (D. F. Ustinov, E. P. Shkurko, I. F. Dmitriev, etc.), monitorearon constantemente el progreso y el desarrollo de producción de diésel, así como aquellos que participaron directamente en la solución de problemas técnicos y organizativos.
Los sistemas autónomos de calentamiento de antorchas e inyección de aceite hicieron posible por primera vez (en 1978) proporcionar un arranque en frío de un motor diesel de tanque a temperaturas de hasta -20 grados C (de 1984 a -25 grados C). Más tarde (en 1985) fue posible con la ayuda del sistema PVV (calentador de aire de admisión) realizar un arranque en frío de un motor diesel de cuatro tiempos (V-84-1) en tanques T-72, pero solo hasta una temperatura de -20 grados C, y no más de veinte arranques dentro del recurso de garantía.
Lo más importante es que 5TDF ha pasado sin problemas a una nueva calidad en motores diesel de la serie 6TD (6TD-1… 6TD-4) con un rango de potencia de 1000-1500 hp.y superando a los análogos extranjeros en una serie de parámetros básicos.
INFORMACIÓN DE FUNCIONAMIENTO DEL MOTOR
Materiales operativos aplicados
El principal tipo de combustible para alimentar el motor es el combustible para motores diesel de alta velocidad GOST 4749-73:
a una temperatura ambiente no inferior a + 5 ° С - marca DL;
a temperaturas ambiente de +5 a -30 ° С - marcas DZ;
a una temperatura ambiente por debajo de -30 ° С - marca DA.
Si es necesario, se permite utilizar combustible DZ a temperaturas ambiente superiores a + 50 ° C.
Además del combustible para motores diésel de alta velocidad, el motor puede funcionar con combustible para aviones TC-1 GOST 10227-62 o gasolina de motor A-72 GOST 2084-67, así como con mezclas de combustibles utilizados en cualquier proporción.
El aceite M16-IHP-3 TU 001226-75 se utiliza para la lubricación del motor. En ausencia de este aceite, se permite el uso de aceite MT-16p.
Al cambiar de un aceite a otro, se debe drenar el aceite residual del cárter del motor y el tanque de aceite de la máquina.
Está prohibido mezclar los aceites usados entre sí, así como el uso de otras marcas de aceites. Se permite mezclar en el sistema de aceite el residuo no drenante de una marca de aceite con otra, rellenado.
Al drenar, la temperatura del aceite no debe ser inferior a + 40 ° C.
Para enfriar el motor a una temperatura ambiente de al menos + 5 ° C, se utiliza agua dulce pura sin impurezas mecánicas, pasada a través de un filtro especial suministrado a la CE de la máquina.
Para proteger el motor de la corrosión y la formación de ácidos, se agrega 0.15% de un aditivo de tres componentes (0.05% de cada componente) al agua que pasa a través del filtro.
El aditivo consiste en fosfato trisódico GOST 201-58, pico de potasio cromo GOST 2652-71 y nitrito de sodio GOST 6194-69 primero se debe disolver en 5-6 litros de agua que se pasa a través de un filtro químico y se calienta a una temperatura de 60-80 ° C. En caso de repostar 2-3 litros, se permite (una vez) usar agua sin aditivos.
No vierta aditivo anticorrosión directamente en el sistema.
En ausencia de un aditivo de tres componentes, se permite utilizar un pico de cromo puro del 0,5%.
A una temperatura ambiente por debajo de + 50 ° C, se debe utilizar un líquido de baja congelación (anticongelante) de "40" o "65" GOST 159-52. El anticongelante de la marca "40" se utiliza a temperaturas ambiente de hasta -35 ° C, a temperaturas inferiores a -35 ° C - el anticongelante de la marca "65".
Llene el motor con combustible, aceite y refrigerante de acuerdo con las medidas para evitar la entrada de impurezas mecánicas, polvo y humedad en el combustible y el aceite.
Se recomienda repostar con la ayuda de camiones cisterna especiales o un dispositivo de repostaje regular (al repostar desde contenedores separados).
El combustible debe repostar a través de un filtro de seda. Se recomienda llenar el aceite con la ayuda de rellenos de aceite especiales. Llene el aceite, el agua y el líquido de baja congelación a través de un filtro con una malla No. 0224 GOST 6613-53.
Llene los sistemas hasta los niveles especificados en las instrucciones de funcionamiento de la máquina.
Para llenar completamente los volúmenes de los sistemas de lubricación y enfriamiento, después de repostar, arranque el motor durante 1-2 minutos, luego verifique los niveles y, si es necesario, reposte los sistemas, Durante el funcionamiento, es necesario controlar la cantidad de refrigerante y aceite en los sistemas del motor y mantener sus niveles de IB dentro de los límites especificados.
No permita que el motor funcione si hay menos de 20 litros de aceite en el tanque de lubricación del motor.
Si el nivel de refrigerante cae debido a la evaporación o se filtra en el sistema de enfriamiento, agregue agua o anticongelante, respectivamente.
Drene el refrigerante y el aceite a través de las válvulas especiales de drenaje del motor y la máquina (caldera de calefacción y tanque de aceite) utilizando una manguera con un racor con las aberturas de llenado abiertas. Para eliminar completamente el agua restante del sistema de enfriamiento para evitar su congelación, se recomienda derramar el sistema con 5-6 litros de líquido de baja congelación.
Características del funcionamiento del motor con varios tipos de combustible.
El funcionamiento del motor con varios tipos de combustible se realiza mediante un mecanismo de control de alimentación de combustible que tiene dos posiciones para ajustar la palanca de combustible múltiple: funcionamiento con combustible para motores diésel de alta velocidad, combustible para motores a reacción, gasolina (con una disminución de potencia).) y sus mezclas en cualquier proporción; trabaja solo con gasolina.
El funcionamiento con otros tipos de combustible con esta posición de palanca está estrictamente prohibido.
La instalación del mecanismo de control de alimentación de combustible desde la posición "Operación con combustible diesel" hasta la posición "Operación con gasolina" se realiza girando el tornillo de ajuste de la palanca multicombustible en el sentido de las agujas del reloj hasta que se detenga, y desde la posición "Operación en gasolina "a la posición" Funcionamiento con combustible diesel "- girando el tornillo de ajuste de la palanca multicombustible en sentido antihorario hasta que se detenga.
Características de arrancar y operar el motor cuando funciona con gasolina. Al menos 2 minutos antes de arrancar el motor, es necesario encender la bomba BCN de la máquina y bombear intensamente el combustible con la bomba de cebado manual de la máquina; en todos los casos, independientemente de la temperatura ambiente, antes de arrancar inyectar aceite dos veces en los cilindros.
La bomba centrífuga de gasolina de la máquina debe permanecer encendida durante todo el tiempo que el motor esté funcionando con gasolina, sus mezclas con otros combustibles y durante paradas breves (3-5 minutos) de la máquina.
La velocidad mínima constante en ralentí cuando el motor funciona con gasolina es de 1000 por minuto.
CARACTERÍSTICAS DE FUNCIONAMIENTO
S. Suvorov recuerda las ventajas y desventajas de este motor en su libro "T-64".
En los tanques T-64A, producidos desde 1975, la armadura de la torreta también se reforzó debido al uso de relleno de corindón.
En estas máquinas, la capacidad de los tanques de combustible también se incrementó de 1093 litros a 1270 litros, como resultado de lo cual apareció una caja para guardar piezas de repuesto en la parte trasera de la torreta. En máquinas de lanzamientos anteriores, los repuestos y accesorios se colocaron en cajas en los guardabarros derechos, donde se instalaron tanques de combustible adicionales, conectados al sistema de combustible. Cuando el conductor instaló la válvula de distribución de combustible en cualquier grupo de tanques (traseros o delanteros), el combustible se produjo principalmente a partir de los tanques externos.
En el mecanismo tensor de la oruga se utilizó un par de tornillo sin fin, lo que permitió su funcionamiento sin mantenimiento durante toda la vida útil del tanque.
Las características de rendimiento de estas máquinas se han mejorado enormemente. Así, por ejemplo, la prueba antes del siguiente servicio numérico se incrementó de 1500 y 3000 km a 2500 y 5000 km para T01 y TO, respectivamente. A modo de comparación, en el tanque T-62 TO1 TO2 se llevó a cabo después de 1000 y 2000 km de carrera, y en el tanque T-72, después de 1600-1800 y 3300-3500 km de carrera, respectivamente. El período de garantía para el motor 5TDF se aumentó de 250 a 500 horas, el período de garantía para toda la máquina fue de 5.000 km.
Pero la escuela es solo un preludio, la operación principal comenzó en las tropas, donde terminé después de graduarme de la universidad en 1978. Justo antes de la graduación, fuimos informados de la orden del Comandante en Jefe de las Fuerzas Terrestres de que los egresados de nuestra escuela deben ser distribuidos solo a aquellas formaciones donde hay tanques T-64. Esto se debió al hecho de que en las tropas hubo casos de fallas masivas de los tanques T-64, en particular, los motores 5TDF. La razón: desconocimiento del material y las reglas de funcionamiento de estos tanques. La adopción del tanque T-64 fue comparable a la transición en la aviación de los motores de pistón a los motores a reacción: los veteranos de la aviación recuerdan cómo fue.
En cuanto al motor 5TDF, hubo dos razones principales para su falla en las tropas: sobrecalentamiento y desgaste por polvo. Ambas razones se debieron al desconocimiento o descuido de las reglas de funcionamiento. El principal inconveniente de este motor es que no está demasiado diseñado para tontos, a veces requiere que hagan lo que está escrito en las instrucciones de funcionamiento. Cuando ya era comandante de una compañía de tanques, uno de mis comandantes de pelotón, un graduado de la Escuela de Tanques de Chelyabinsk, que entrenaba a oficiales para los tanques T-72, de alguna manera comenzó a criticar la planta de energía del tanque T-64. No le gustó el motor y la frecuencia de su mantenimiento. Pero cuando le hicieron la pregunta "¿Cuántas veces en seis meses abriste los techos del MTO en tus tres tanques de entrenamiento y miraste en el compartimiento del motor-transmisión?" Resultó que nunca. Y los tanques se fueron, proporcionaron entrenamiento de combate.
Y así sucesivamente. El sobrecalentamiento del motor se produjo por varias razones. Primero, el mecánico olvidó quitar la alfombrilla del radiador y luego no miró los instrumentos, pero esto sucedió muy raramente y, por regla general, en invierno. El segundo y principal es el llenado con refrigerante. De acuerdo con las instrucciones, se supone que debe llenar el agua (durante el período de operación de verano) con un aditivo de tres componentes, y el agua debe llenarse a través de un sulfofiltro especial, con el que se equiparon todas las máquinas de liberación temprana, y en nuevas máquinas se emitió uno de estos filtros por empresa (10-13 tanques). Los motores fallaron, principalmente de los tanques del grupo de entrenamiento de operación, que fueron operados al menos cinco días a la semana y generalmente se ubican en rangos en parques de campo. Al mismo tiempo, los "libros de texto" de los conductores-mecánicos (los llamados mecánicos de las máquinas de entrenamiento), como regla, trabajadores duros y muchachos concienzudos, pero no conocían las complejidades del motor, a veces podían permitirse verter agua en el sistema de enfriamiento solo del grifo, especialmente porque el sulfofiltro (que es uno por empresa) generalmente se guardaba en los cuarteles de invierno, en algún lugar del casillero del director técnico de la empresa. El resultado es la formación de incrustaciones en los canales delgados del sistema de refrigeración (en la zona de las cámaras de combustión), la falta de circulación de líquido en la parte más caliente del motor, el sobrecalentamiento y la avería del motor. La formación de escamas se vio agravada por el hecho de que el agua en Alemania es muy dura.
Una vez en una unidad vecina, se retiró el motor por sobrecalentamiento por culpa del conductor. Habiendo encontrado una pequeña fuga de refrigerante del radiador, siguiendo el consejo de uno de los "expertos" para agregar mostaza al sistema, compró un paquete de mostaza en la tienda y lo vertió todo en el sistema, como resultado: obstrucción de canales y avería del motor.
También hubo otras sorpresas con el sistema de refrigeración. De repente, comienza a expulsar refrigerante del sistema de enfriamiento a través de una válvula de vapor-aire (PVK). Algunos, sin comprender cuál es el problema, intentan arrancarlo desde el remolcador, el resultado de la destrucción del motor. Así, el subjefe de mi batallón me hizo un "regalo" para el Año Nuevo, y tuve que cambiar el motor el 31 de diciembre. Tuve tiempo antes del Año Nuevo, porque Reemplazar el motor en un tanque T-64 no es un procedimiento muy complicado y, lo más importante, no requiere alineación al instalarlo. La mayoría de las veces, cuando se reemplaza un motor en un tanque T-64, como en todos los tanques domésticos, se realiza mediante el procedimiento de drenaje y reabastecimiento de aceite y refrigerante. Si nuestros tanques tuvieran conectores con válvulas en lugar de conexiones durit, como en Leopards o Leclercs, entonces reemplazar el motor en los tanques T-64 o T-80 a tiempo no tomaría más que reemplazar toda la unidad de potencia en los tanques occidentales. Por ejemplo, en ese día memorable, el 31 de diciembre de 1980, después de drenar el aceite y el refrigerante, el suboficial E. Sokolov y yo "tiramos" el motor del MTO en sólo 15 minutos.
La segunda razón del fallo de los motores 5TDF es el polvo. Sistema de purificación de aire. Si no verifica el nivel de refrigerante de manera oportuna, pero debe verificarlo antes de cada salida de la máquina, puede llegar un momento en que no habrá líquido en la parte superior de la camisa de enfriamiento y se producirá un sobrecalentamiento local. En este caso, el punto más débil es la boquilla. En este caso, las juntas del inyector se queman o el propio inyector falla, luego, a través de grietas o juntas quemadas, los gases de los cilindros penetran en el sistema de enfriamiento y, bajo su presión, el líquido se expulsa a través del PVCL. Todo esto no es fatal para el motor y se elimina si hay una persona con conocimientos en la unidad. En motores convencionales en línea y en forma de V en una situación similar, "conduce" la junta de culata, y en este caso habrá más trabajo.
Si en tal situación, el motor se detiene y no se toman medidas, luego de un tiempo los cilindros comenzarán a llenarse de refrigerante, el motor es una rejilla inercial y un filtro de aire ciclónico. El filtro de aire, de acuerdo con las instrucciones de funcionamiento, se limpia según sea necesario. En tanques del tipo T-62, se lavó en invierno después de 1000 km y en verano después de 500 km. En un tanque T-64, según sea necesario. Aquí es donde entra el obstáculo: algunos lo tomaron como el hecho de que no es necesario lavarlo en absoluto. La necesidad surgió cuando el petróleo entró en los ciclones. Y si al menos uno de los 144 ciclones contiene aceite, entonces el filtro de aire debe lavarse, porque a través de este ciclón, el aire sin limpiar con polvo ingresa al motor y luego, como esmeril, se borran las camisas de los cilindros y los segmentos de los pistones. El motor comienza a perder potencia, aumenta el consumo de aceite y luego deja de arrancar por completo.
No es difícil verificar la entrada de aceite en los ciclones; solo mire las entradas de ciclones en el filtro de aire. Por lo general, miraban el tubo de descarga de polvo del filtro de aire y, si se encontraba aceite en él, miraban el filtro de aire y, si era necesario, lo lavaban. ¿De dónde vino el aceite? Es simple: la boca de llenado del tanque de aceite del sistema de lubricación del motor se encuentra junto a la rejilla de entrada de aire. Al repostar con aceite, se suele utilizar una regadera, pero como nuevamente, en las máquinas de entrenamiento, las regaderas, por regla general, estaban ausentes (alguien se perdió, alguien se lo puso en un cinturón de oruga, lo olvidó y lo atravesó, etc.), luego los mecánicos simplemente vertieron aceite de los cubos, mientras que el aceite se derramaba, primero cayó sobre la malla de entrada de aire y luego en el filtro de aire. Incluso cuando se llena el aceite a través de una regadera, pero en un clima ventoso, el viento salpica el aceite sobre la malla del filtro de aire. Por lo tanto, al repostar el aceite, exigí a mis subordinados que pusieran una alfombra de los repuestos y accesorios del tanque en la malla de entrada de aire, como resultado de lo cual evité problemas con el desgaste del motor por polvo. Cabe señalar que las condiciones polvorientas en Alemania en el verano fueron las más severas. Así, por ejemplo, durante los ejercicios divisionales en agosto de 1982, al realizar una marcha por los claros del bosque de Alemania, debido al polvo que colgaba, ni siquiera se veía dónde terminaba el cañón del cañón de su propio tanque. La distancia entre los coches de la columna se mantuvo literalmente mediante el olor. Cuando quedaban literalmente unos pocos metros para el tanque de cabeza, era posible discernir el olor de sus gases de escape y frenar a tiempo. Y así 150 kilómetros. Después de la marcha, todo: los tanques, las personas y sus rostros, los monos y las botas eran del mismo color, el color del polvo de la carretera.
Diésel 6TD
Simultáneamente con el diseño y el refinamiento tecnológico del motor diésel 5TDF, el equipo de diseño de KKBD comenzó a desarrollar el siguiente modelo de un motor diésel de 2 tiempos ya en un diseño de 6 cilindros con una potencia aumentada de hasta 735 kW (1000 CV).. Este motor, al igual que el 5TDF, era un motor diésel con cilindros dispuestos horizontalmente, pistones de contramovimiento y soplado de flujo directo. El diesel se llamó 6TD.
La turboalimentación se realizó desde un compresor conectado mecánicamente (resorte) a la turbina de gas, convirtiendo parte de la energía térmica de los gases de escape en trabajo mecánico para accionar el compresor.
Dado que la potencia desarrollada por la turbina no era suficiente para impulsar el compresor, se conectó a ambos cigüeñales del motor mediante una caja de cambios y un mecanismo de transmisión. La relación de compresión se tomó como 15.
Para obtener la sincronización de válvulas requerida, en la que se proporcionaría la limpieza necesaria del cilindro de los gases de escape y el llenado con aire comprimido, se proporcionó un desplazamiento angular de los cigüeñales (como en los motores 5TDF) en combinación con una disposición asimétrica de la admisión. y lumbreras de escape de los cilindros a lo largo de su longitud. El par tomado de los cigüeñales es del 30% para el eje de admisión y del 70% para el escape del par motor. El par desarrollado en el eje de admisión se transmitió a través de la transmisión de engranajes al eje de escape. El par total se puede tomar de ambos extremos del eje de escape a través del embrague de la toma de fuerza.
En octubre de 1979, el motor 6TD, después de una seria revisión del grupo cilindro-pistón, el equipo de combustible, el sistema de suministro de aire y otros elementos, pasó con éxito las pruebas interdepartamentales. Desde 1986 se fabrican los primeros motores de la serie 55. En los años siguientes, la producción en serie aumentó y alcanzó su punto máximo en 1989.
El porcentaje de unificación pieza por pieza del 6TD con el motor diesel 5TDF fue de más del 76%, y la confiabilidad de operación no fue menor que la del 5TDF, que se había producido en serie durante muchos años.
Continuó el trabajo del KHKBD bajo el liderazgo del diseñador jefe N. K. Ryazantsev para mejorar aún más el motor diesel de tanque de 2 tiempos. Se estaban ultimando unidades, mecanismos y sistemas, según los cuales se identificaron defectos individuales en funcionamiento. Se mejoró el sistema de presurización. Se llevaron a cabo numerosas pruebas de banco de motores con la introducción de cambios de diseño.
Se estaba desarrollando una nueva modificación del motor diesel, 6TD-2. Su potencia ya no era de 735 kW (1000 CV), como en el 6TD, sino de 882 kW (1200 CV). Su unificación detallada con el motor diesel 6TD fue proporcionada en más del 90%, y con el motor diesel 5TDF, más del 69%.
A diferencia del motor 6TD, el motor 6TD-2 utilizó un compresor axialmente centrífugo de 2 etapas del sistema de presurización y cambios en el diseño de la turbina, fuelles, filtro de aceite centrífugo, tubería de derivación y otras unidades. La relación de compresión también se redujo ligeramente, de 15 a 14,5 y la presión efectiva media se incrementó de 0,98 MPa a 1,27 MPa. El consumo específico de combustible del motor 6TD-2 fue 220 g / (kW * h) (162 g / (hp * h)) en lugar de 215 g / (kW * h) (158 g / (hp * h)) - para 6TD. Desde el punto de vista de la instalación en un tanque, el motor diesel 6TD-2 era completamente intercambiable con el motor 6DT.
En 1985, el Diesel 6TD-2 pasó las pruebas interdepartamentales y se presentó la documentación de diseño para la preparación y organización de la producción en serie.
En KKBD, con la participación de NIID y otras organizaciones, continuaron los trabajos de investigación y desarrollo del motor diésel 6TD de 2 tiempos con el objetivo de aumentar su potencia a 1103 kW (1500 CV), 1176 kW (1600 CV), 1323 kW (1800 CV). con pruebas en muestras, así como la creación de una familia de motores para VGM y máquinas de economía nacional. Para VGM de categoría de peso ligero e intermedio, se desarrollaron motores diésel 3TD con una capacidad de 184 … 235 kW (250-320 CV), 4TD con una capacidad de 294 … 331 kW (400 … 450 CV). También se desarrolló una variante de un motor diesel 5DN con una capacidad de 331… 367 kW (450-500 hp) para vehículos de ruedas. Para los transportadores de tractores y vehículos de ingeniería, se desarrolló un proyecto para un motor diesel 6DN con una capacidad de 441 … 515 kW (600-700 hp).
Diésel 3TD
Los motores ZTD en diseño de tres cilindros son miembros de una sola serie unificada con motores en serie 5TDF, 6TD-1 y 6TD-2E. A principios de los años 60, se creó en Jarkov una familia de motores basados en 5TDF para vehículos ligeros (vehículos blindados de transporte de tropas, vehículos de combate de infantería, etc.) y categoría de peso pesado (tanques, 5TDF, 6TD).
Estos motores tienen un esquema de diseño único:
- ciclo de dos tiempos;
- disposición horizontal de cilindros;
- alta compacidad;
- baja transferencia de calor;
- la capacidad de usar a temperatura ambiente
entornos de menos 50 a más 55 ° С;
- reducción de potencia de baja potencia a altas temperaturas
el entorno;
- multicombustible.
Además de razones objetivas, se cometieron errores en la creación de una familia de motores diésel bóxer de dos tiempos 3TD a mediados de los años 60. La idea de un motor de 3 cilindros se probó sobre la base de un motor de 5 cilindros en el que se amortiguaban dos cilindros. Al mismo tiempo, la ruta aire-gas y las unidades de presurización no estaban coordinadas. Naturalmente, también se incrementó la potencia de las pérdidas mecánicas.
El principal obstáculo para la creación de una familia unificada de motores en los años 60 y 70 fue la falta de un programa claro para el desarrollo de la construcción de motores en el país; el liderazgo fue “tirarse” entre varios conceptos de motores diésel y motores de turbina de gas.. En los años 70, cuando Leonid Brezhnev llegó al liderazgo del país, la situación se agravó aún más, la producción paralela de tanques con diferentes motores: T-72 y T-80, que por sus características eran "tanques análogos" de los ya producido T-64. Ya no se habló de la unificación de los motores del tanque, los vehículos de combate de infantería y los vehículos blindados de transporte de personal.
Desafortunadamente, la misma situación ocurrió en otras ramas del complejo militar-industrial; al mismo tiempo, se estaban desarrollando varias oficinas de diseño en cohetería, construcción de aviones, mientras que las mejores no fueron seleccionadas entre ellas, sino productos similares de diferentes oficinas de diseño (Design Bureau) se produjeron en paralelo.
Tal política fue el comienzo del fin de la economía nacional y la razón del retraso en la construcción de tanques, en lugar de estar unidos en un "solo puño", los esfuerzos se dispersaron en el desarrollo paralelo de oficinas de diseño competidoras.
Los vehículos ligeros (LME), producidos en los años 60 … 80 del siglo pasado, tienen motores de diseño anticuado, proporcionando una densidad de potencia en el rango de 16-20 CV / t. Las máquinas modernas deberían tener una potencia específica de 25-28 CV / t, lo que aumentará su maniobrabilidad.
En los años 90, 2000, la modernización del LME se volvió relevante: BTR-70, BTR-50, BMP-2.
Durante este período, se llevaron a cabo pruebas de estas máquinas, que mostraron las altas características del nuevo motor, pero, al mismo tiempo, una gran cantidad de motores UTD-20S1 fueron almacenados y en producción en el territorio de Ucrania después del colapso. de la URSS.
Diseñador general para la construcción de tanques de Ucrania M. D. Borisyuk (KMDB) decidió utilizar los motores en serie existentes: SMD-21 UTD-20 y el alemán "Deutz" para modernizar estas máquinas.
Cada vehículo tenía sus propios motores que no estaban unificados entre sí y con motores que ya estaban en el ejército. El motivo es que resulta rentable para las plantas de reparación del Ministerio de Defensa utilizar los motores disponibles en los almacenes del cliente, lo que reduce el coste de obra.
Pero este cargo privado del trabajo de la Empresa Estatal “Planta que lleva el nombre de V. A. Malysheva”y, sobre todo, la planta de áridos.
Esta posición resultó ser ambigua: por un lado, ahorros, por otro, pérdida de perspectiva.
Cabe señalar que en KMDB en relación a 3TD, se realizaron una serie de reclamos (por ruido y humo), que fueron aceptadas y eliminadas.
Para reducir el humo durante el arranque y en los modos transitorios, se instaló un equipo de combustible cerrado en el motor ZTD y el consumo de aceite se redujo significativamente. La reducción del ruido se garantiza reduciendo la presión máxima de combustión y reduciendo el juego en el par pistón-cilindro en motores de 280 y 400 hp, así como reduciendo el rango de vibraciones torsionales.
La reducción del consumo de aceite en los motores ZTD se logró debido a los siguientes factores:
- reducir el número de cilindros;
- el uso de un pistón con cuerpo de hierro fundido en lugar de una aleación de aluminio;
- aumentando la presión específica del anillo raspador de aceite mediante
pared del cilindro.
Como resultado de las medidas tomadas, el consumo relativo de aceite en los motores ZTD se acerca al consumo en los motores con fines económicos nacionales.