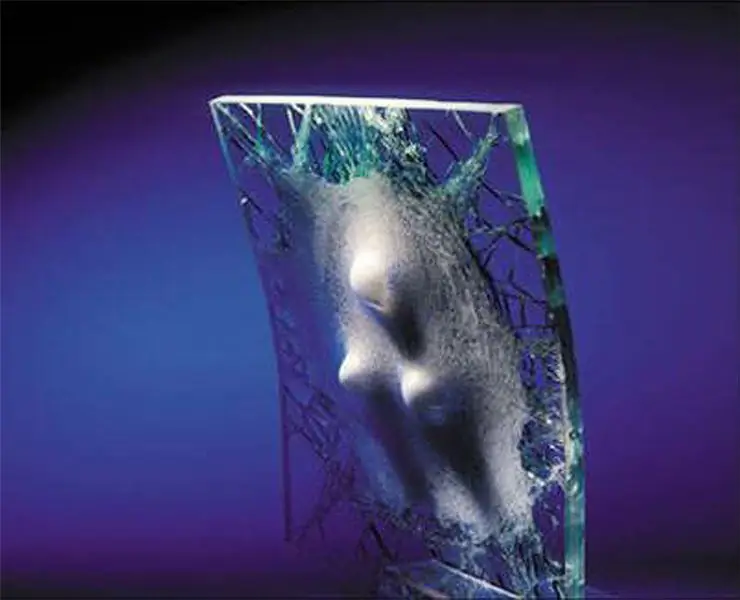
Los vehículos militares se han fabricado tradicionalmente con acero blindado pesado, caro pero de alta resistencia. Los materiales compuestos cerámicos modernos se utilizan cada vez más como protección sin cojinetes para vehículos de combate. Las principales ventajas de estos materiales son un costo significativamente menor, una protección mejorada y una reducción de peso en más de la mitad. Considere los materiales cerámicos básicos modernos que se utilizan hoy en día para la protección balística
Debido a su capacidad para soportar temperaturas muy elevadas, significativamente superiores a la de los metales, dureza, la mayor resistencia específica y rigidez específica, las cerámicas son ampliamente utilizadas para la fabricación de revestimientos para motores, componentes de cohetes, filos de herramientas, transparentes especiales y escudos opacos, que, por supuesto, se encuentran entre las áreas prioritarias para el desarrollo de sistemas militares. Sin embargo, en el futuro, el alcance de su aplicación debe expandirse significativamente, ya que en el marco de la investigación y el desarrollo llevados a cabo en muchos países del mundo, se están buscando nuevas formas de aumentar la plasticidad, la resistencia al agrietamiento y otras propiedades mecánicas deseables por parte de combinando una base cerámica con fibras de refuerzo en la denominada matriz cerámica. Materiales compuestos (KMKM). Además, las nuevas tecnologías de fabricación permitirán la producción en masa de productos transparentes muy duraderos y de alta calidad de formas complejas y grandes tamaños a partir de materiales que transmiten ondas visibles e infrarrojas. Además, la creación de nuevas estructuras mediante la nanotecnología permitirá obtener materiales duraderos y ligeros, resistentes al sobrecalentamiento, químicamente resistentes y, al mismo tiempo, prácticamente indestructibles. Esta combinación de propiedades se considera hoy en día mutuamente excluyente y, por tanto, muy atractiva para aplicaciones militares.
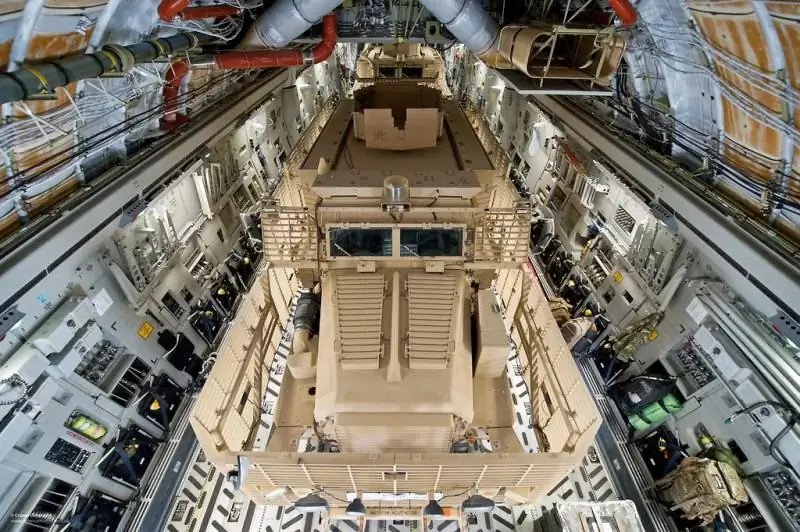
Materiales compuestos de matriz cerámica (KMKM)
Al igual que sus análogos poliméricos, las CMC consisten en una sustancia base, llamada matriz, y un relleno de refuerzo, que son partículas o fibras de otro material. Las fibras pueden ser continuas o discretas, orientadas al azar, colocadas en ángulos precisos, entrelazadas de una manera especial para obtener una mayor resistencia y rigidez en direcciones dadas, o distribuidas uniformemente en todas las direcciones. Sin embargo, cualquiera que sea la combinación de materiales o la orientación de las fibras, la unión entre la matriz y el componente de refuerzo es fundamental para las propiedades del material. Dado que los polímeros son menos rígidos que el material que los refuerza, la unión entre la matriz y las fibras suele ser lo suficientemente fuerte como para permitir que el material resista la flexión en su conjunto. Sin embargo, en el caso de CMCM, la matriz puede ser más rígida que las fibras de refuerzo de modo que la fuerza de unión, igualmente optimizada para permitir una ligera deslocalización de la fibra y la matriz, ayude a absorber la energía del impacto, por ejemplo, y evitar el desarrollo de grietas. que de otro modo conduciría a una frágil destrucción y división. Esto hace que el CMCM sea mucho más viscoso en comparación con la cerámica pura, y esta es la más importante de las propiedades de las piezas móviles muy cargadas, por ejemplo, las piezas de los motores a reacción.
Palas de turbina livianas y calientes
En febrero de 2015, GE Aviation anunció pruebas exitosas de lo que llama "el primer kit CMC no estático del mundo para un motor de avión", aunque la compañía no reveló los materiales utilizados para la matriz y el material de refuerzo. Hablamos de álabes de turbina de baja presión en un modelo experimental del motor turbofan F414, cuyo desarrollo pretende proporcionar una mayor confirmación del cumplimiento del material con los requisitos declarados para el funcionamiento con altas cargas de choque. Esta actividad es parte del Programa de demostración de motores autoadaptativos de próxima generación del Demostrador de tecnología de motores adaptables (AETD), en el que GE colabora con el Laboratorio de Investigación de la Fuerza Aérea de EE. UU. El objetivo del programa AETD es proporcionar tecnologías clave que puedan implementarse en motores de cazas de sexta generación y, a partir de mediados de la década de 2020, en motores de aviones de quinta generación, como el F-35. Los motores adaptables podrán ajustar su aumento de presión y la relación de derivación en vuelo para obtener el máximo empuje durante el despegue y en combate, o la máxima eficiencia de combustible en el modo de vuelo de crucero.
La empresa enfatiza que la introducción de partes giratorias hechas de CMC en las partes “más calientes y más cargadas” de un motor a reacción representa un avance significativo, ya que anteriormente la tecnología permitía usar CMC solo para la fabricación de partes estacionarias, por ejemplo, un Cubierta de turbina de alta presión. Durante las pruebas, las palas de la turbina KMKM en el motor F414 pasaron por 500 ciclos, desde la velocidad de ralentí hasta el empuje de despegue y viceversa.
Las palas de la turbina son mucho más livianas que las palas de aleación de níquel convencionales, lo que permitió que los discos de metal a los que están unidas fueran más pequeños y livianos, dijo la compañía.
“El cambio de las aleaciones de níquel a la cerámica giratoria dentro del motor es un gran paso adelante. Pero es pura mecánica”, dijo Jonathan Blank, director de CMC y aglutinantes poliméricos de GE Aviation. - Las hojas más ligeras generan menos fuerza centrífuga. Esto significa que puede contraer discos, cojinetes y otras partes. KMKM hizo posible realizar cambios revolucionarios en el diseño de un motor a reacción”.
El objetivo del programa AETD es reducir el consumo específico de combustible en un 25%, aumentar el rango de vuelo en más del 30% y aumentar el empuje máximo en un 10% en comparación con los cazas de quinta generación más avanzados. “Uno de los mayores desafíos al pasar de componentes CMC estáticos a componentes giratorios es el campo de tensión en el que deben operar”, dijo Dan McCormick, Gerente del Programa de Motor de Combate Avanzado en GE Aviation. Al mismo tiempo, agregó que las pruebas del motor F414 arrojaron resultados importantes que se utilizarán en el motor de ciclo adaptativo. “Una pala de turbina CMC de baja presión pesa tres veces menos que la pala metálica a la que reemplaza, además, en el segundo modo económico, no hay necesidad de enfriar la pala CMC con aire. La hoja ahora será más eficiente aerodinámicamente, ya que no es necesario bombear todo este aire de refrigeración a través de ella.
Los materiales KMKM, en los que la compañía dice haber invertido más de mil millones de dólares desde que comenzó a trabajar en ellos a principios de los 90, pueden soportar temperaturas cientos de grados más altas que las aleaciones de níquel tradicionales y se distinguen por un refuerzo de fibra de carburo de silicio en una matriz cerámica.., lo que aumenta su resistencia al impacto y al agrietamiento.
GE parece haber hecho un trabajo bastante duro en estas palas de turbina. De hecho, algunas de las propiedades mecánicas de KMKM son muy modestas. Por ejemplo, la resistencia a la tracción es comparable a la resistencia a la tracción del cobre y las aleaciones de aluminio baratas, lo que no es muy bueno para las piezas que están sujetas a grandes fuerzas centrífugas. Además, presentan una baja deformación en la rotura, es decir, se alargan muy ligeramente en la rotura. Sin embargo, estas deficiencias parecen haber sido superadas y el bajo peso de estos materiales definitivamente contribuyó de manera importante a la victoria de la nueva tecnología.
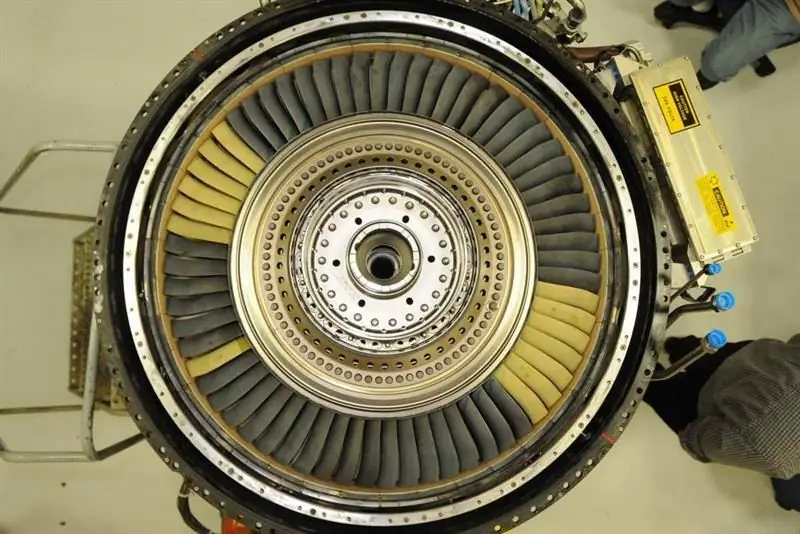
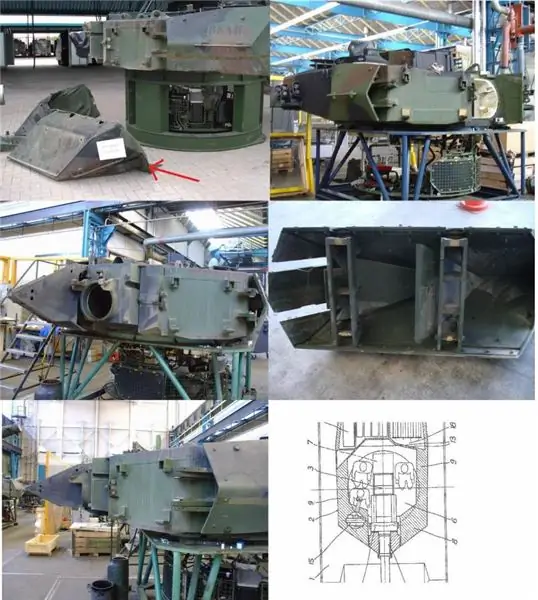
Armadura modular con nanocerámica para el tanque LEOPARD 2
Contribución de armadura compuesta
Aunque las tecnologías de protección, que son una combinación de capas de metal, compuestos poliméricos reforzados con fibra y cerámica, están bien establecidas, la industria continúa desarrollando materiales compuestos cada vez más complejos, pero muchos de los detalles de este proceso se ocultan cuidadosamente. Morgan Advanced Materials es bien conocido en el campo, y el año pasado anunció un premio en la conferencia Armored Vehicles XV en Londres por su tecnología de defensa SAMAS. Según Morgan, la protección SAMAS ampliamente utilizada en los vehículos del ejército británico es un material compuesto reforzado con materiales como S-2 Glass, E-Glass, aramida y polietileno, que luego se forma en láminas y se cura a alta presión: “Las fibras se pueden combinar con materiales híbridos de cerámica y metal para cumplir con requisitos especiales de diseño y rendimiento.
Según Morgan, la armadura SAMAS con un espesor total de 25 mm, utilizada para la fabricación de cápsulas protectoras de la tripulación, puede reducir el peso de los vehículos ligeros protegidos en más de 1000 kg en comparación con los vehículos con cápsula de acero. Otros beneficios incluyen reparaciones más fáciles con espesores de menos de 5 mm más gruesos y las propiedades inherentes del revestimiento desconchado de este material.
Progreso explícito de la espinela
Según el Laboratorio de Investigación de la Marina de los EE. UU., El desarrollo y la producción de materiales transparentes basados en óxido de magnesio y aluminio (MgAI2O4), también conocidos colectivamente como espinelas artificiales, está en auge. Las espinelas son conocidas desde hace mucho tiempo no solo por su resistencia - la espinela de 0,25 "de espesor tiene las mismas características balísticas que el vidrio a prueba de balas de 2,5" - sino también por la dificultad de fabricar piezas grandes con transparencia uniforme. Sin embargo, un grupo de científicos de este laboratorio ha inventado un nuevo proceso de sinterización a baja temperatura en vacío, que permite obtener piezas con dimensiones limitadas únicamente por el tamaño de la prensa. Este es un gran avance en comparación con los procesos de fabricación anteriores, que comenzaron con el proceso de fundir el polvo original en un crisol de fusión.
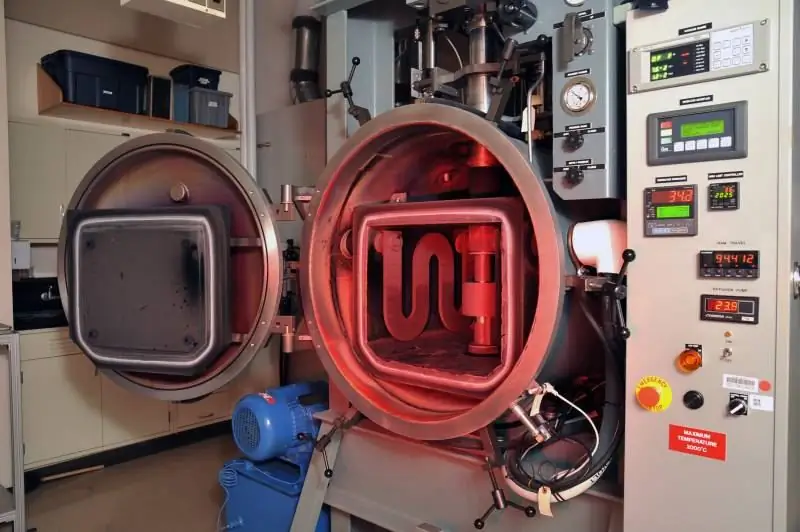
Uno de los secretos del nuevo proceso es la distribución uniforme del aditivo de sinterización de fluoruro de litio (LiF), que funde y lubrica los granos de espinela para que puedan distribuirse uniformemente durante la sinterización. En lugar de mezclar en seco fluoruro de litio y polvos de espinela, el laboratorio ha desarrollado un método para recubrir uniformemente las partículas de espinela con fluoruro de litio. Esto le permite reducir significativamente el consumo de LiF y aumentar la transmitancia de luz hasta un 99% del valor teórico en las regiones visible e infrarroja media del espectro (0.4-5 micrones).
El nuevo proceso, que permite la producción de ópticas en varias formas, incluidas láminas que se ajustan cómodamente a las alas de un avión o dron, ha sido autorizado por una empresa anónima. Las posibles aplicaciones de la espinela incluyen vidrio blindado que pesa menos de la mitad de la masa del vidrio existente, máscaras protectoras para soldados, ópticas para láseres de próxima generación y lentes con sensores multiespectrales. Al producir en masa, por ejemplo, gafas resistentes a las grietas para teléfonos inteligentes y tabletas, el costo de los productos de espinela disminuirá significativamente.
PERLUCOR: un nuevo hito en los sistemas de protección antibalas y antidesgaste
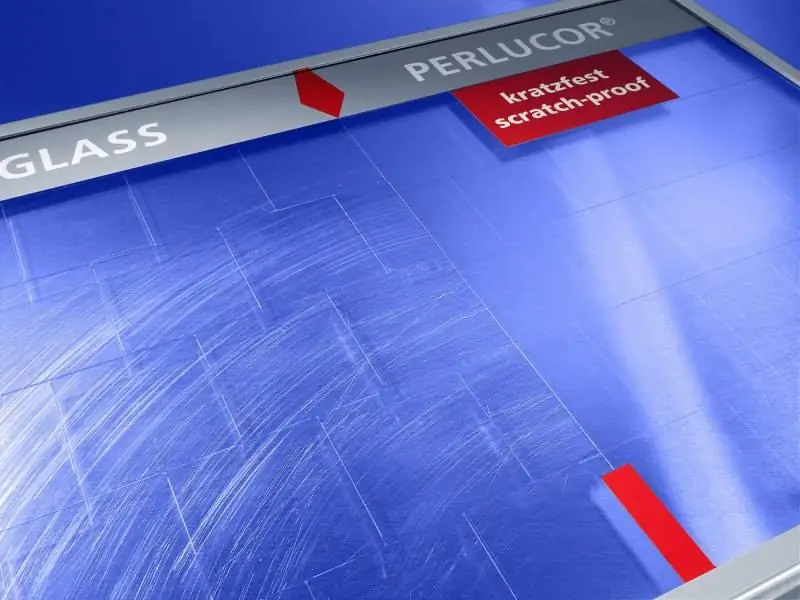
CeramTec-ETEC desarrolló las cerámicas transparentes PERLUCOR hace unos años con buenas perspectivas para aplicaciones civiles y de defensa. Las excelentes propiedades físicas, químicas y mecánicas de PERLUCOR fueron las principales razones para la exitosa entrada al mercado de este material.
PERLUCOR tiene una transparencia relativa de más del 90%, es de tres a cuatro veces más fuerte y más duro que el vidrio ordinario, la resistencia al calor de este material es aproximadamente tres veces mayor, lo que permite su uso a temperaturas de hasta 1600 ° C, también tiene una resistencia química extremadamente alta, esto permite su uso con ácidos y álcalis concentrados. PERLUCOR tiene un alto índice de refracción (1, 72), lo que permite fabricar objetivos ópticos y elementos ópticos de dimensiones en miniatura, es decir, obtener dispositivos con un potente aumento, que no se puede lograr con polímeros o vidrio. Las baldosas cerámicas PERLUCOR tienen un tamaño estándar de 90x90 mm; sin embargo, CeramTec-ETEC ha desarrollado una tecnología para la producción de láminas de formas complejas basadas en este formato de acuerdo con las especificaciones del cliente. El grosor de los paneles en casos especiales puede ser de décimas de milímetro, pero, por regla general, es de 2-10 mm.
El desarrollo de sistemas de protección transparente más ligeros y delgados para el mercado de la defensa avanza a un ritmo acelerado. Una contribución significativa a este proceso la hacen las cerámicas transparentes de la empresa SegamTes, que forma parte de los sistemas de protección de muchos fabricantes. Cuando se prueba de acuerdo con STANAG 4569 o APSD, la reducción de peso es del orden del 30-60 por ciento.
En los últimos años, ha tomado forma otra dirección en el desarrollo de tecnologías desarrolladas por SegatTes-ETEC. Las ventanillas de los vehículos, especialmente en áreas rocosas y desérticas como Afganistán, son propensas a impactos de piedras y arañazos por el movimiento de las escobillas del limpiaparabrisas en un parabrisas polvoriento y arenoso. Además, se reducen las características balísticas de los vidrios antibalas que han sido dañados por impactos de piedras. Durante las hostilidades, los vehículos con vidrios dañados están expuestos a riesgos graves e impredecibles. SegamTes-ETEC ha desarrollado una solución verdaderamente innovadora y original para proteger el vidrio de este tipo de desgaste. Una capa fina (<1 mm) de revestimiento cerámico PERLUCOR en la superficie del parabrisas ayuda a resistir con éxito tales daños. Esta protección también es adecuada para instrumentos ópticos como telescopios, lentes, equipos de infrarrojos y otros sensores. Las lentes planas y curvas de cerámica transparente PERLUCOR prolongan la vida útil de este equipo óptico de gran valor y sensibilidad.
CeramTec-ETEC presentó con éxito un panel de puerta de vidrio a prueba de balas y un panel protector resistente a arañazos y piedras en el DSEI 2015 en Londres.
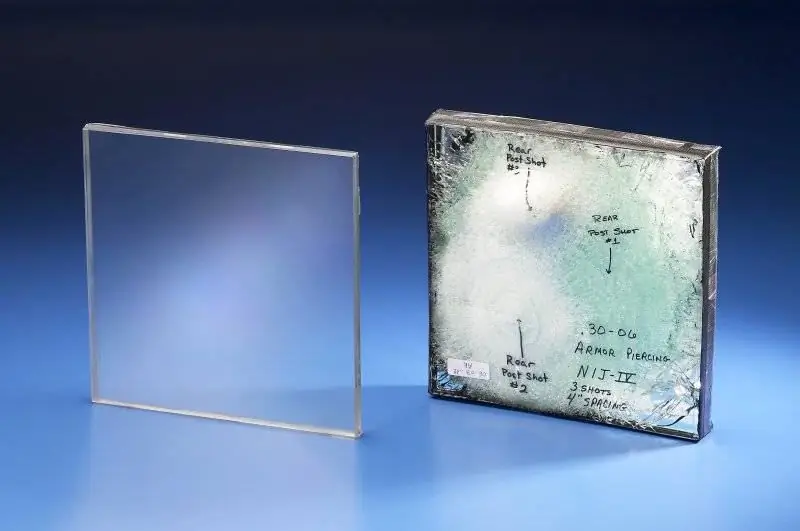
Nanocerámica duradera y flexible
La flexibilidad y la resiliencia no son cualidades inherentes a la cerámica, pero un equipo de científicos dirigido por la profesora de ciencia y mecánica de materiales Julia Greer del Instituto de Tecnología de California abordó el problema. Los investigadores describen el nuevo material como "nanoredes cerámicas tridimensionales resistentes, ligeras y regenerables". Sin embargo, este es el mismo nombre para un artículo publicado por Greer y sus estudiantes en una revista científica hace un par de años.
Lo que se esconde debajo se ilustra mejor con un cubo de nanoredes de óxido de aluminio de varias decenas de micrones de tamaño, tomado con un microscopio electrónico. Bajo la acción de la carga, se contrae en un 85% y, cuando se retira, se restaura a su tamaño original. También se realizaron experimentos con celosías formadas por tubos de diferentes espesores, siendo los tubos más delgados los más resistentes y elásticos. Con un espesor de pared del tubo de 50 nanómetros, la celosía colapsó, y con un espesor de pared de 10 nanómetros, volvió a su estado original, un ejemplo de cómo el efecto de tamaño aumenta la resistencia de algunos materiales. La teoría explica esto por el hecho de que con una disminución en el tamaño, el número de defectos en los materiales a granel disminuye proporcionalmente. Con esta arquitectura de celosía de tubos huecos, el 99,9% del volumen del cubo es aire.
El equipo del profesor Greer crea estas pequeñas estructuras ejecutando un proceso similar a la impresión 3D. Cada proceso comienza con un archivo CAD que impulsa dos láseres que "pintan" la estructura en tres dimensiones, curando el polímero en puntos donde los haces se amplifican entre sí en fase. El polímero sin curar fluye fuera de la rejilla curada, que ahora se convierte en el sustrato para formar la estructura final. Luego, los investigadores aplican la alúmina al sustrato utilizando un método que controla con precisión el grosor del recubrimiento. Finalmente, los extremos de la celosía se cortan para eliminar el polímero, dejando solo la celosía cristalina de los tubos huecos de alúmina.
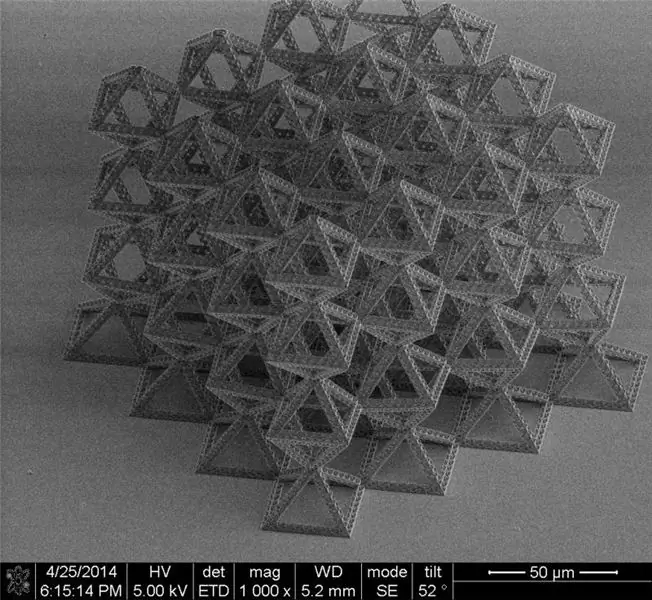
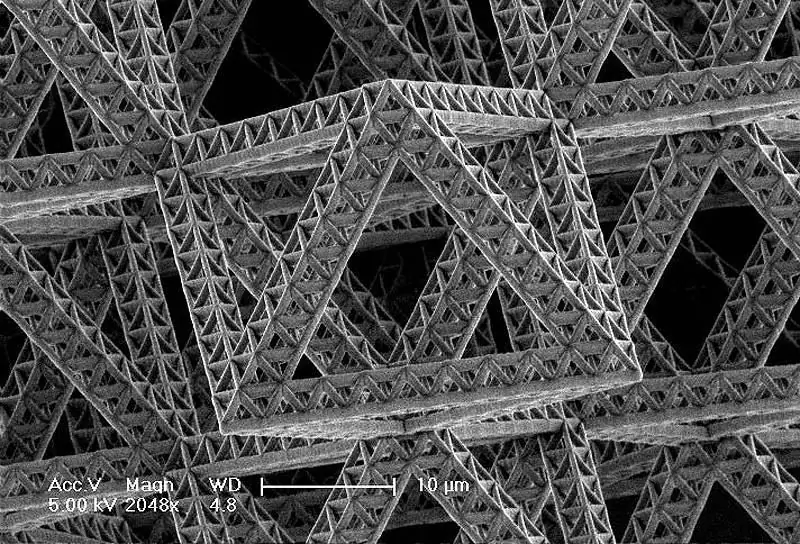
Resistencia del acero, pero pesa como el aire
El potencial de estos materiales "diseñados", que son en su mayoría aire por volumen, pero son menos fuertes como el acero, es enorme, pero difícil de comprender, por lo que el profesor Greer dio varios ejemplos sorprendentes. El primer ejemplo, globos de los que se bombea helio, pero que al mismo tiempo conservan su forma. El segundo, futuro avión, cuyo diseño pesa tanto como pesa su modelo manual. Lo más sorprendente es que si el famoso puente Golden Gate estuviera hecho de nanoredes, todos los materiales necesarios para su construcción podrían colocarse (excluyendo el aire) en la palma de una mano humana.
Así como las enormes ventajas estructurales de estos materiales duros, livianos y resistentes al calor adecuados para innumerables aplicaciones militares, sus propiedades eléctricas predeterminadas podrían revolucionar el almacenamiento y la generación de energía: “Estas nanoestructuras son muy livianas, mecánicamente estables y al mismo tiempo enormes en tamaño. superficies, es decir, que podemos utilizar en una variedad de aplicaciones de tipo electroquímico.
Estos incluyen electrodos extremadamente eficientes para baterías y celdas de combustible, son un objetivo preciado para fuentes de energía autónomas, plantas de energía portátiles y transportables, así como un verdadero avance en la tecnología de celdas solares.
"Los cristales fotónicos también se pueden nombrar a este respecto", dijo Greer. "Estas estructuras le permiten manipular la luz de tal manera que puede capturarla por completo, lo que significa que puede hacer células solares mucho más eficientes: captura toda la luz y no tiene pérdida por reflexión".
“Todo esto sugiere que la combinación del efecto de tamaño en nanomateriales y elementos estructurales nos permite crear nuevas clases de materiales con propiedades que no se han podido lograr”, dijo el profesor Greer de la Organización Europea para la Investigación Nuclear en Suiza. "El mayor desafío al que nos enfrentamos es cómo escalar y pasar de nano al tamaño de nuestro mundo".
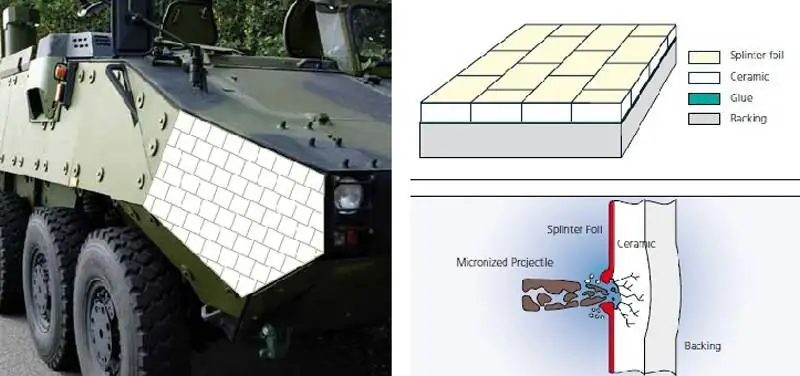
Protección industrial de cerámica transparente
IBD Deisenroth Engineering ha desarrollado una armadura de cerámica transparente con un rendimiento balístico comparable a la armadura de cerámica opaca. Esta nueva armadura transparente es aproximadamente un 70% más liviana que el vidrio blindado y se puede ensamblar en estructuras con las mismas características de impacto múltiple (capacidad para resistir múltiples golpes) que la armadura opaca. Esto permite no solo reducir drásticamente la masa de vehículos con ventanas grandes, sino también cerrar todas las brechas balísticas.
Para obtener una protección según STANAG 4569 Nivel 3, el vidrio blindado tiene una densidad superficial de aproximadamente 200 kg / m2. Con un área de ventana típica de un camión de tres metros cuadrados, la masa de los vidrios antibalas será de 600 kg. Al reemplazar dichos vidrios a prueba de balas con cerámica IBD, la reducción de peso será de más de 400 kg. La cerámica transparente de IBD es un desarrollo posterior de la cerámica IBD NANOTech. IBD ha logrado desarrollar procesos de unión especiales que se utilizan para ensamblar baldosas cerámicas ("armadura transparente de mosaico") y luego laminar estos ensamblajes a capas estructurales fuertes para formar paneles de ventanas grandes. Debido a las características sobresalientes de este material cerámico, es posible producir paneles de blindaje transparentes con un peso significativamente menor. El respaldo, en combinación con el laminado de NANO-Fibra Natural, mejora aún más el rendimiento balístico de la nueva protección transparente debido a su mayor absorción de energía.
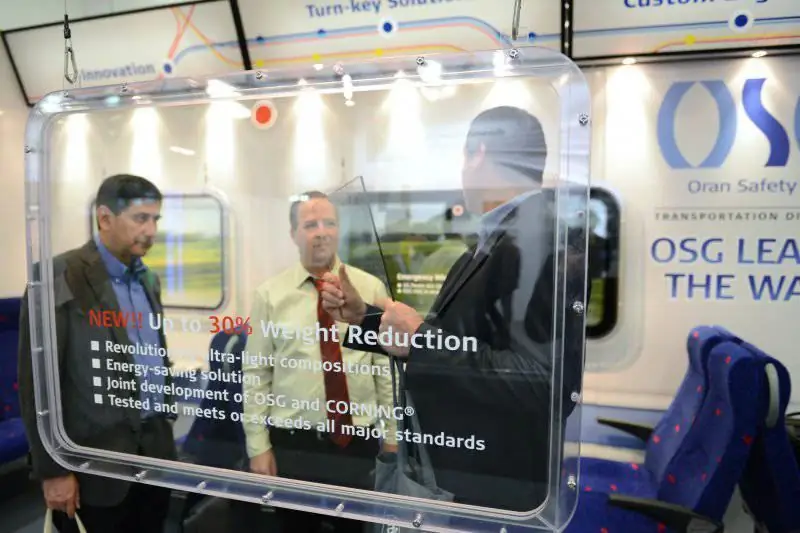
La empresa israelí OSG (Oran Safety Glass), respondiendo a los crecientes niveles de inestabilidad y tensión en todo el mundo, ha desarrollado una amplia gama de productos de vidrio a prueba de balas. Están diseñados específicamente para los sectores de defensa y civil, el ejército, los paramilitares, ocupaciones civiles de alto riesgo, la construcción y la industria automotriz. La empresa promueve las siguientes tecnologías en el mercado: soluciones de protección transparente, soluciones de protección balística, sistemas de blindaje transparente avanzado adicional, ventanas visuales digitales, ventanas de salida de emergencia, ventanas de cerámica con tecnología de visualización a color, sistemas de luces indicadoras integradas, protectores de vidrio resistentes a los golpes, piedras y, finalmente, la tecnología ADI anti-astillado.
Los materiales transparentes OSG se prueban constantemente en situaciones de la vida real: repelen ataques físicos y balísticos, salvan vidas y protegen propiedades. Todos los materiales transparentes blindados se han creado de acuerdo con los principales estándares internacionales.