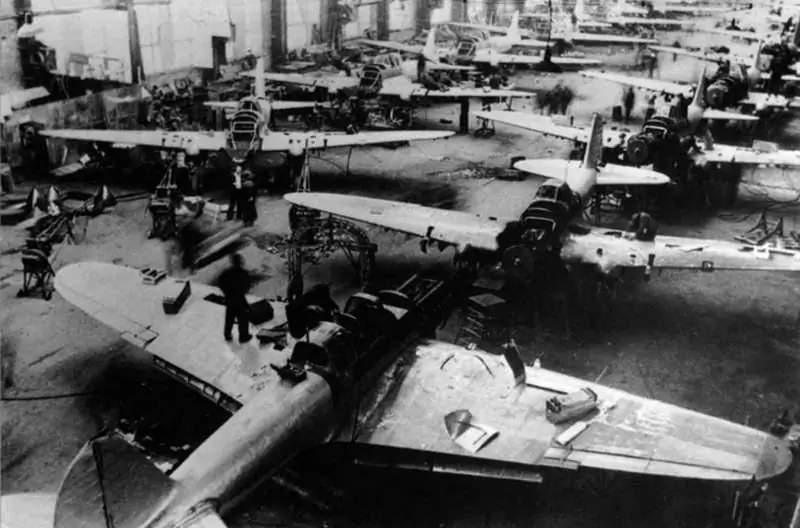
Preparándose para una gran guerra
En la primera parte del material sobre la industria del aluminio y su impacto en el potencial militar de la Unión Soviética, se dijo que el país estaba muy por detrás de Alemania. En 1941, la industria nazi estaba más de tres veces por delante de la soviética en este parámetro. Además, incluso sus propios cálculos en el marco del plan de movilización MP-1, que data del 17 de junio de 1938 (aprobado por el Comité de Defensa del Consejo de Comisarios del Pueblo), suponían que el país necesitaría unas 131,8 mil toneladas de Aluminio en caso de guerra. Y para 1941, en realidad, la Unión Soviética era capaz de producir no más de 100 mil toneladas de "metal alado", y esto, por supuesto, sin tener en cuenta la pérdida de los territorios occidentales, donde las principales empresas de se localizaron metalurgia ferrosa.
La industria de la aviación fue la más sensible al déficit de aluminio, y el Consejo de Comisarios del Pueblo desarrolló una serie de medidas para satisfacer parcialmente las crecientes necesidades del Comisariado del Pueblo para la Industria de la Aviación. En 1941, se suponía que la escasez se cerraría utilizando el retorno de metales ligeros (34 mil toneladas), la introducción de madera refinada (15 mil toneladas) en el diseño de aviones, la producción de aleaciones de magnesio (4 mil toneladas) y mediante ahorros banales (18 mil toneladas). toneladas). Esto, por cierto, fue una consecuencia del aumento de los apetitos de movilización de la Unión Soviética: para 1942 se planeó usar no 131, 8 mil toneladas de aluminio, sino más de 175 mil toneladas. Además del aumento cuantitativo de la producción de aluminio, se previeron en el país métodos de mejora cualitativa de las aleaciones basadas en el "metal alado". Los aviones de duraluminio fueron inicialmente más reparados y pintados en el ejército de lo que volaban, lo que fue una consecuencia de la baja resistencia a la corrosión de la aleación. Con el tiempo, la planta de Aviakhim desarrolló un método para revestir duraluminio con aluminio puro (que, a su vez, estaba cubierto de aire con una fuerte película protectora de óxido), y desde 1932 esta técnica se ha vuelto obligatoria para toda la industria de la aviación soviética.
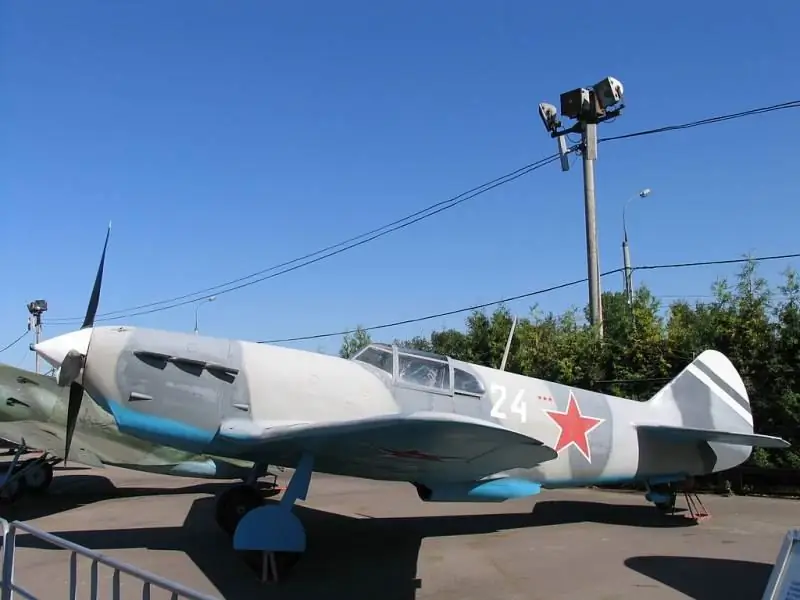
La "hambruna de aluminio" afectó negativamente la calidad de los aviones domésticos no sólo de la clase de motor ligero de los tipos U-2 y UT-2, sino también de los cazas Yak-7 y LaGG-3. Por ejemplo, el caza Yak-7 era un avión con un ala de madera y una piel de fuselaje lisa de madera contrachapada. La parte de cola del casco, timones y alerones estaban cubiertos con lona. Solo el capó del motor y las escotillas laterales de la nariz del avión estaban hechos de duraluminio. Además, uno de los principales cazas de combate del período de guerra, el LaGG-3, era generalmente de madera. Los elementos portantes de su estructura estaban hechos de la llamada madera delta. Los pilotos descifraron sarcásticamente la abreviatura "LaGG" como "ataúd garantizado lacado". Sin embargo, se produjeron 6.528 aviones de este tipo, incluso en las fábricas de aviones de Leningrado, y participaron activamente en las hostilidades. Según el historiador militar A. A. Ayuda, estos cazas estaban originalmente "condenados a ceder ante el Me-109 de aluminio alemán, que en 1941 se acercaba a la velocidad de 600 km / h".
Las aleaciones sobre una base de aluminio, tan necesarias para la aviación, en la URSS al comienzo de la guerra fueron fundidas por tres plantas: Voroshilov en Leningrado, Moscú No. 95 y la planta de aleaciones ligeras Stupino No. 150 construida en 1940. Durante la construcción de este último, recurrieron activamente a los estadounidenses en busca de ayuda. En 1935, una delegación encabezada por Andrei Tupolev fue a los Estados Unidos, donde resultó que grandes láminas de duraluminio de 2, 5 metros por 7 metros se utilizan ampliamente en la construcción de aviones en el extranjero. En la URSS, en ese momento no podían hacer una hoja de más de 1x4 metros; tales estándares tecnológicos existen desde 1922. Naturalmente, el gobierno pidió a Alcoa que proporcionara laminadores de rodillos múltiples para la producción de láminas de duraluminio similares, pero la respuesta fue no. No vendí los molinos a Alcoa; así es como lo hará el antiguo socio comercial de la Unión Soviética, Henry Ford. Su empresa y varias otras en los Estados Unidos suministraron varios grandes trenes de laminación para aleaciones de aluminio a la URSS a fines de la década de 1930. Como resultado, solo la planta de Stupino en 1940 produjo 4191 toneladas de productos laminados de duraluminio de alta calidad.
El decimotercer elemento de la victoria
La mayor pérdida del comienzo de la Gran Guerra Patria para la industria del aluminio fue la planta de aluminio Dneprovsky. A mediados de agosto, intentaron detener a los tanques alemanes que se dirigían a Zaporozhye destruyendo parcialmente la central hidroeléctrica de Dnieper, lo que provocó numerosas bajas tanto entre los ocupantes como entre el Ejército Rojo y la población civil. La evacuación de la fundición de aluminio Dneprovsky, la planta más grande de su tipo en Europa, estuvo a cargo de funcionarios de alto rango junto a los alemanes: el ingeniero jefe de Glavaluminiya A. A. La evacuación bajo constante fuego enemigo (los nazis estaban en la otra orilla del Dnieper) terminó el 16 de septiembre de 1941, cuando se envió el último de dos mil vagones con equipo hacia el este. Los alemanes no lograron organizar la producción de aluminio en la empresa Zaporozhye hasta el mismo momento del exilio. Según un escenario similar, las refinerías de aluminio de Volkhov y de alúmina de Tikhvin fueron evacuadas.
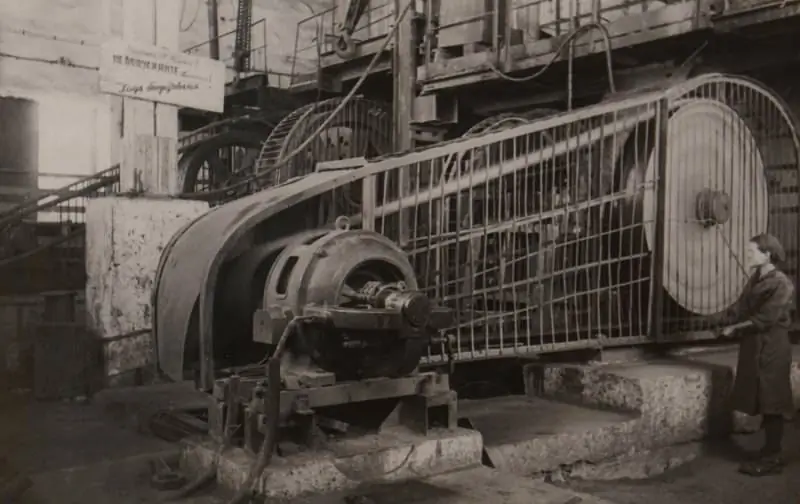
En el otoño de 1941, cesó la producción de productos laminados de duraluminio y solo se restableció en mayo del año siguiente. Ahora la producción se basaba únicamente en dos empresas: la planta nº 95 en Verkhnyaya Salda y la planta nº 150 en la estación de Kuntsevo. Naturalmente, debido a una parada temporal, el volumen de producción de aviones totalmente metálicos se hundió, aunque ligeramente, de 3404 copias de 1940 a 3196 aviones alados en 1941. Pero desde 1942, el volumen de producción de aviones de duraluminio no ha dejado de crecer. Formalmente, la industria de la aviación soviética logró superar la aguda escasez de duraluminio en el verano de 1944; fue entonces cuando se estabilizó el volumen de producción de aviones. En cuanto a los cazas, esto se pudo observar durante la Operación Bagration en Bielorrusia, cuando comenzaron a llegar al frente aviones del diseño de S. A. Lavochkin La-7. La mayoría de sus elementos portantes estaban hechos de aleaciones de metales ligeros. El caza era superior a su principal enemigo, el FW-190A, en velocidad, velocidad de ascenso y maniobrabilidad. Y si en 1942 el crecimiento de la producción de aviones se explicaba por la puesta en servicio de capacidades evacuadas de oeste a este, entonces en 1943 aparecieron en el país plantas de aluminio, que antes no existían. Este año fue posible encargar la construcción de la planta de aluminio de Bogoslovsky en la región de Sverdlovsk y la planta de aluminio de Novokuznetsk en la región de Kemerovo. Los especialistas de las plantas de aluminio de Volkhov y de alúmina de Tikhvin, previamente evacuadas, brindaron una enorme ayuda para organizar la producción de aluminio en estas empresas. En cuanto a la Planta Teológica de Aluminio, cabe decir que la primera fundición de aluminio se llevó a cabo solo en un día significativo, el 9 de mayo de 1945. La primera etapa de la planta de Novokuznetsk se lanzó en enero de 1943. Ese mismo año, la fundición de aluminio en la URSS superó el nivel de antes de la guerra en un 4%. Por ejemplo, solo la Planta de Aluminio de los Urales (UAZ) en 1943 producía 5,5 veces más aluminio que antes de la guerra.
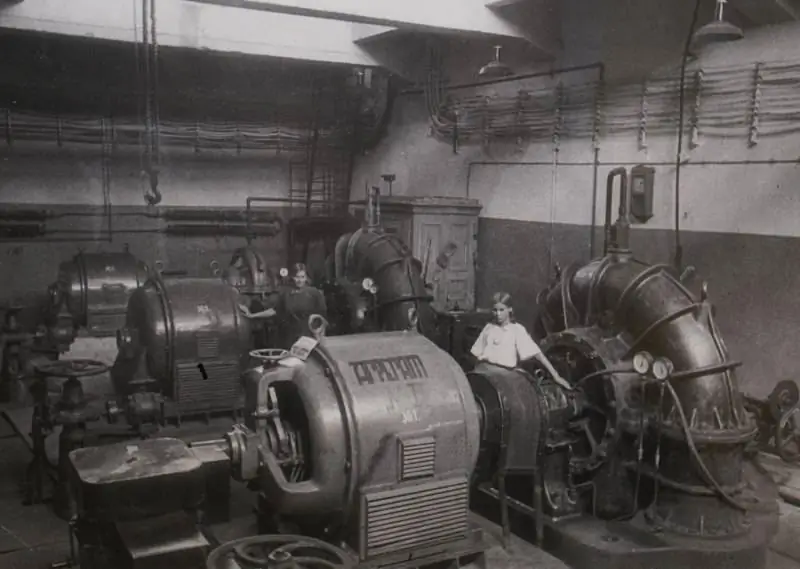
Evidentemente, el déficit de aluminio nacional se superó no sin la ayuda de los suministros de Estados Unidos en el marco del programa Lend-Lease. Entonces, allá por julio de 1941, al recibir en el Kremlin al representante personal del presidente estadounidense G. Hopkins, Joseph Stalin nombró la gasolina de alto octanaje y el aluminio para la producción de aviones entre los tipos de asistencia más necesarios de Estados Unidos. En total, EE. UU., Gran Bretaña y Canadá suministraron alrededor de 327 mil toneladas de aluminio primario. ¿Es mucho o poco? Por un lado, no mucho: solo Estados Unidos, en el marco del Lend-Lease, envió a la URSS 388 mil toneladas de cobre refinado, una materia prima mucho más escasa. Por otro lado, los suministros del exterior representaron el 125% del nivel de producción de aluminio en tiempos de guerra en la Unión Soviética.
Los avances en la producción de aluminio durante la Gran Guerra Patria se observaron no solo en términos de aumento de los volúmenes de producción, sino también en la reducción del consumo de energía para la fundición. Entonces, en 1943, la URSS dominó la tecnología de fundición de aluminio en hornos de gas, lo que redujo gravemente la dependencia de las empresas metalúrgicas no ferrosas del suministro de electricidad. En el mismo año, la técnica de colada continua de duraluminio comenzó a ser ampliamente utilizada. Y un año antes, por primera vez en la historia de la industria en la planta de Ural, la producción actual de aluminio excedía los 60 gramos de metal por 1 kilovatio-hora de electricidad a la tasa requerida de 56 gramos. Esta fue una de las razones del brillante logro de 1944: UAZ ahorró 70 millones de kilovatios-hora de electricidad. Creo que no tendría sentido hablar de lo que esto significó para la industria movilizada de la Unión Soviética.