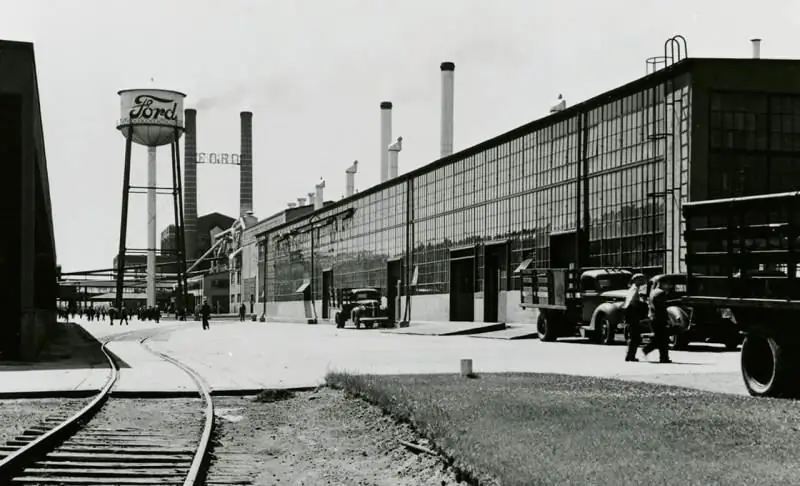
Tecnologías estratégicas
Antes de familiarizarse con las características de la producción de blindados en la planta de Michigan Ford en Detroit (EE. UU.), Conviene explicar brevemente las condiciones en las que se estaba estableciendo la industria del blindaje en la URSS. Como sabes, todo se aprende por comparación.
La producción de armaduras durante la Segunda Guerra Mundial fue uno de los factores más importantes en la ventaja estratégica. Con el comienzo de la guerra, la Unión Soviética se encontró en una posición desastrosa: toda la producción de blindados se concentró en la parte europea del país. El rápido avance del ejército alemán podría paralizar por completo la producción de blindados de tanques en el país. Solo a costa de increíbles esfuerzos para evacuar parte de las fábricas hacia el este al comienzo de la guerra, fue posible restaurar la producción de armaduras. Las principales "fábricas blindadas" eran las plantas metalúrgicas de Kuznetsk, Nizhny Tagil y Magnitogorsk.
Pero el asunto no se limitó a una simple transferencia de producción a un nuevo sitio detrás de la línea del frente. La mayoría de las nuevas fábricas no se adaptaron a la fundición de blindaje de tanques; antes de la guerra, las fábricas trabajaban para las necesidades del Comisariado Popular de Metalurgia Ferrosa. El tiempo de guerra ha añadido sus propios ajustes. Ahora que los hornos de hogar abierto a menudo tenían trabajadores poco calificados, existía un grave problema de falta de equipos especiales térmicos, de prensado y de trabajo de metales. Por lo tanto, la transferencia de la producción de armaduras fue acompañada de una seria reestructuración de la propia tecnología para la fundición de acero militar. Entonces, fue necesario adecuar la producción a los principales hornos de hogar abierto para 120-180 toneladas, excluyendo el proceso de desoxidación por difusión. El endurecimiento de las placas de blindaje y las partes del blindaje tuvo que realizarse en agua.
Tal simplificación no podía dejar de afectar la calidad de la armadura recibida. Esto es especialmente cierto para los tanques de acero 8C de alta dureza más difíciles de fabricar. Las primeras muestras de placas de blindaje en las pruebas mostraron pizarra significativa y estratificación de la fractura, una alta tendencia a la formación de grietas durante la soldadura y el enderezamiento. Además de esto, las pruebas de campo revelaron la excesiva fragilidad de las muestras de armadura durante el fuego de los proyectiles.
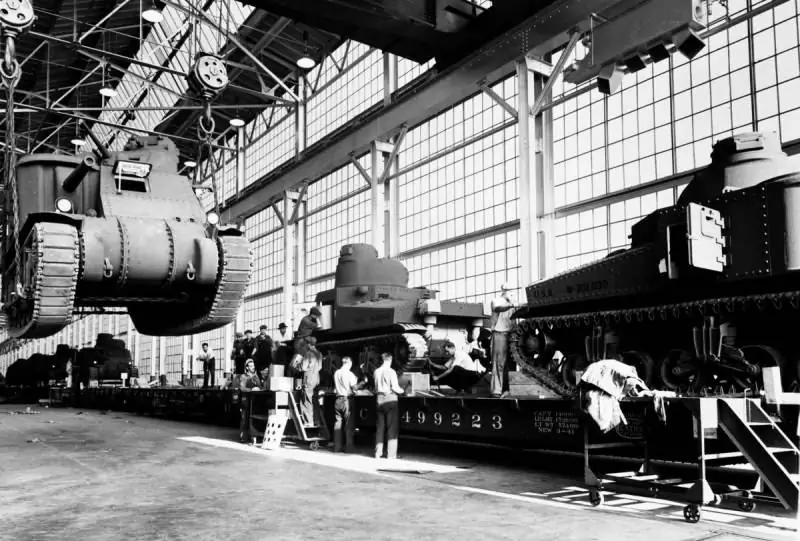
Tales defectos no pueden ignorarse. Y en el TsNII-48 especializado se han desarrollado una serie de mejoras. En primer lugar, a partir de ahora, se suponía que el acero para armaduras solo se fundiría en hornos precalentados después de fundir aceros de grado "civil". El acero tuvo que hervir en el baño de fundición de hogar abierto durante al menos una hora y media, y verterlo en moldes cuadrados o convexos. Además, los metalúrgicos prestaron especial atención al contenido de azufre en el arrabio original (no más del 0.06%), así como al carbono y al manganeso. En combinación con otras medidas, esto permitió mejorar la calidad de la armadura. En particular, para reducir la pizarra y estratificación de la fractura.
Un problema importante fue la tecnología de tratamiento térmico de armaduras domésticas. En pocas palabras, el endurecimiento y revenido de las placas de blindaje tomó demasiado tiempo y energía, y faltaba el equipo necesario. Era necesario simplificar el proceso. Al respecto, daremos un ejemplo típico. En 1942, los metalúrgicos de TsNII-48 lograron simplificar tanto el proceso de preparación térmica que solo para partes de los fondos de los tanques KV y T-34 ahorraron alrededor de 3230 horas de horno por cada 100 cascos.
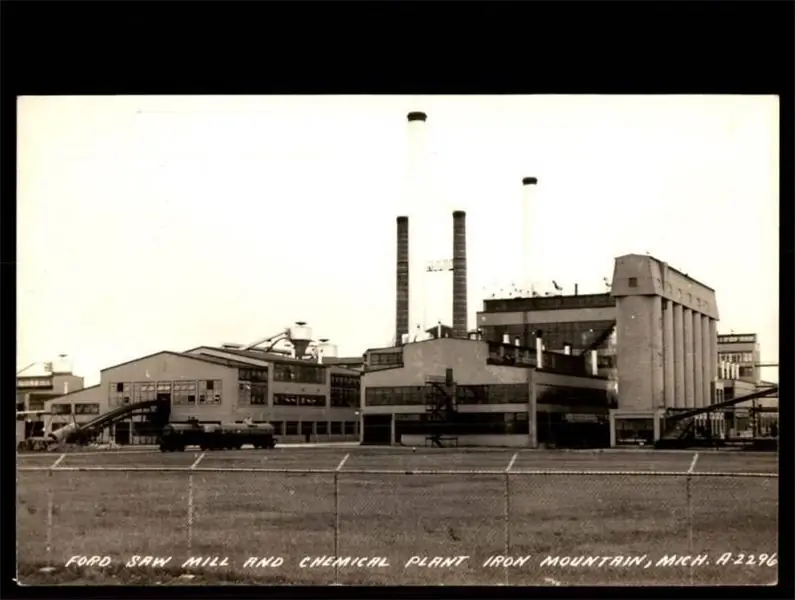
Sin embargo, hasta el final de la guerra en la Unión Soviética, las condiciones para la producción de blindaje de tanques de importancia estratégica estaban lejos de ser necesarias. No se puede decir lo mismo de la industria militar del socio extranjero, cuyo territorio no se vio afectado por la guerra mundial. Los ingenieros metalúrgicos soviéticos tuvieron que asegurarse de esto una vez más el 26 de febrero de 1945, 72 días antes de la Victoria.
Lujo americano
La poco conocida historia de la visita de la delegación soviética a la fábrica blindada Ford en Detroit fue anunciada por Vasily Vladimirovich Zapariy, Candidato de Ciencias Históricas del Instituto de Historia y Arqueología de la Rama Ural de la Academia de Ciencias de Rusia. El material del científico se basa en el informe de los metalúrgicos soviéticos sobre los resultados de un viaje a los Estados Unidos almacenados en el Archivo Estatal de Economía de Rusia (RGAE). Cabe señalar que la RGAE es solo un tesoro de documentos de archivo de la era de la Gran Guerra Patria relacionados con la producción de equipos y equipos militares. Solo queda adivinar cuántos secretos más guarda el archivo en las pruebas hasta ahora clasificadas.
Según los ingenieros que regresaron de Detroit, el taller blindado de la planta de Ford era un edificio que constaba de dos vanos de 273 metros de largo, 30 metros de ancho y unos 10 metros de alto. Al mismo tiempo, la tienda no olía armaduras. Estaba destinado principalmente al tratamiento térmico y al corte de acero. Esto naturalmente despertó un interés particular entre los metalúrgicos soviéticos, dados los problemas antes descritos de la producción de blindados domésticos. El perfil de producción principal del taller de Ford Motors fue trabajar con armaduras de hasta 76 mm de espesor. Se utilizaron láminas de acero tratadas térmicamente para soldar los cascos de vehículos blindados ligeros y medianos en otras fábricas de Detroit.
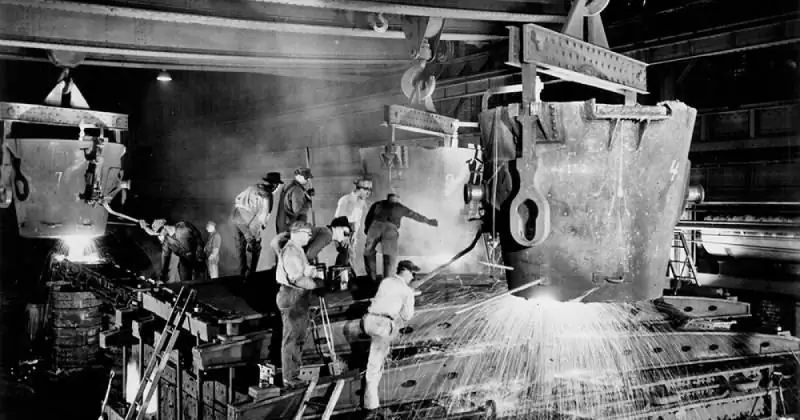
En primer lugar, la mecanización del proceso de producción impresionó a los talleres de Ford. Después de fundir y rodar, las placas de blindaje se entregaron al taller de tratamiento térmico en las cargadoras hidráulicas de mesa United. Los cargadores, a su vez, tomaron el blindaje de los andenes ferroviarios ubicados cerca del taller. En el propio taller, había dos puentes grúa diseñados para mover láminas de blindaje durante todas las operaciones tecnológicas, a excepción de los procesos de endurecimiento.
Para crear la necesaria estructura cristalina de la armadura se recurrió a dos prensas, con un esfuerzo de 2500 toneladas cada una, cinco hornos metódicos de cinta transportadora de 70 metros y cinco hornos transportadores de templado a gas de 100 metros. Se suministró agua a las prensas de endurecimiento de armaduras mediante el funcionamiento de seis bombas a la vez, bombeando más de 3700 litros por minuto. Como escribieron los ingenieros rusos, la complejidad y el costo del diseño de tales prensas, capaces de estampar y enfriar simultáneamente armaduras al rojo vivo, eran prohibitivos. Al mismo tiempo, existían dudas sobre la conveniencia de utilizar prensas para armaduras con un espesor de 30-76 mm. Aquí, la intensidad del suministro de agua para refrigeración pasó a primer plano.
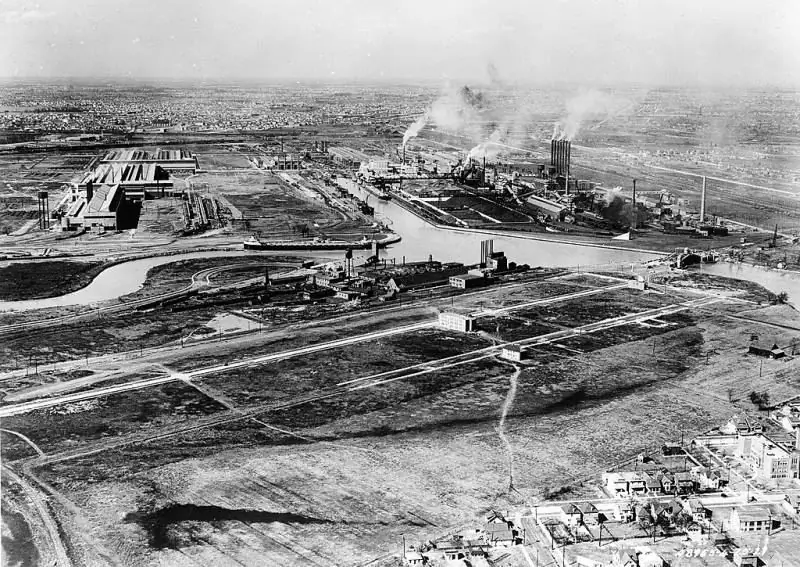
Las prensas de 2.500 toneladas no fueron las únicas en el vehículo blindado Ford. Las prensas Toledo # 206 se dedicaron a cortar armaduras delgadas y desarrollaron una presión de 161 toneladas. Para armaduras de más de 2,5 cm, se utilizó exclusivamente corte de fuego.
Durante una visita a la empresa, los metalúrgicos pudieron captar el proceso de endurecimiento de la armadura delgada a prueba de balas. Permaneció bajo una prensa de 1000 toneladas durante 15 segundos, y luego la hoja se envió durante 2,5 horas para templar a 900 grados Celsius y durante cuatro horas de vacaciones a 593 grados.
Toda esta riqueza técnica fue observada por los ingenieros soviéticos, sin contar varios "pequeños accesorios": máquinas de soldar, fresadoras, tijeras y similares.
La característica principal del tratamiento térmico de la armadura fue el flujo continuo de producción. En casi todas las etapas del procesamiento, las láminas de acero estaban en proceso de moverse sobre transportadores de rodillos y cadenas. El transportador se controlaba desde una consola central. En una de las últimas etapas, se inspeccionaron todas las placas de blindaje para determinar el nivel de dureza Brinell. En este caso, la fluctuación del parámetro de prueba de una hoja a otra debe ser mínima, no más de 0,2 mm.
De particular interés para la delegación soviética fueron dos máquinas de granallado, que limpiaban las placas de blindaje casi después de cada operación tecnológica. Tal perfeccionismo y tal lujo solo podrían ser permitidos por los estadounidenses, lejos de las dificultades de la guerra.