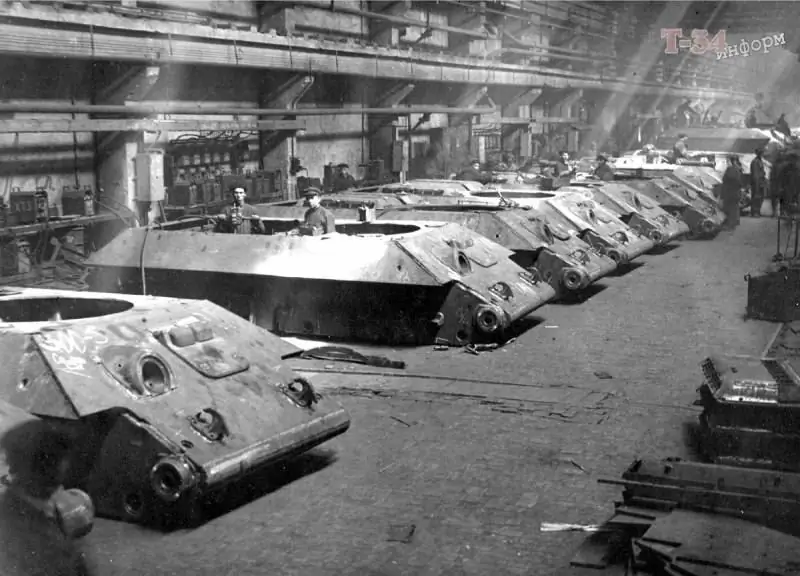
Eslabones débiles de la guardia de acero
¿Cómo puede un aumento similar a una avalancha en la producción de tanques que el frente necesita con urgencia? El libro de Nikita Melnikov "La industria de tanques de la URSS durante la Gran Guerra Patriótica" proporciona datos sobre la disminución de las condiciones para recibir productos terminados por parte de representantes militares.
Desde el 15 de enero de 1942, las fábricas de tanques han sido muy "liberales" al evaluar la calidad de la fabricación de vehículos blindados. Solo uno de cada diez tanques medianos T-34 y KV pesados a elección del representante militar fue sometido a una carrera corta de cinco kilómetros. En el caso de los tanques T-60, obviamente hubo más dudas, por lo que uno de cada cinco tanques ligeros fue sometido a una carrera. O, tal vez, tales máquinas eran menos necesarias en el frente, por lo tanto, eran más estrictas con ellas incluso en la etapa de aceptación. Esto confirma indirectamente el disparo de control del cañón de cada T-60 que sale de las puertas de las fábricas, mientras que los cañones T-34 y KV se probaron solo en cada décimo vehículo. Se permitió enviar tanques a las tropas con velocímetros faltantes, motores de giro de torreta, intercomunicadores si se reemplazaban con lámparas de señalización, así como ventiladores de torre. El último punto, afortunadamente, solo se permitió en invierno.
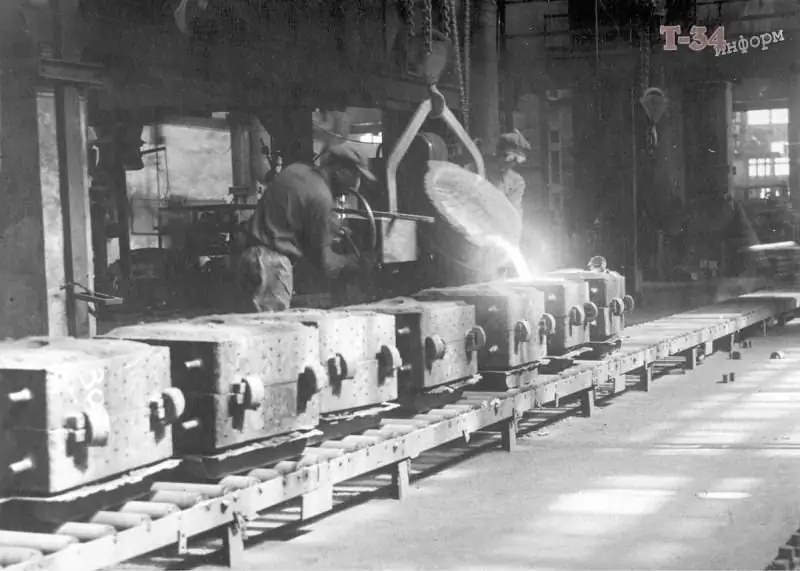
Cabe señalar por separado que la industria de los tanques ya había hecho frente con éxito a los indicadores cuantitativos de la producción de vehículos blindados a mediados de 1942. Uralmash incluso excedía regularmente los estándares de producción para tanques, y la planta de Kirov en Chelyabinsk, solo de enero a marzo, cuadruplicó la producción del motor diesel V-2.
Estas tasas de crecimiento de la producción se debieron en gran parte a una grave disminución de la calidad de los tanques que salen de la línea de montaje. Un ejemplo ilustrativo es la 121a Brigada de Tanques, que, durante un lanzamiento de 250 kilómetros, perdió la mitad de sus KV pesados debido a averías. Ocurrió en febrero de 1942. Durante mucho tiempo después de eso, la situación no cambió fundamentalmente. En el otoño de 1942, se inspeccionaron 84 tanques KV, que estaban averiados por razones técnicas, que ni siquiera funcionaron 15 horas de motocicleta. La mayoría de las veces, había motores defectuosos, cajas de engranajes rotas, rodillos defectuosos, triplex inutilizables y muchas fallas menores. En el verano de 1942, hasta el 35% de todos los tanques T-34 se perdieron no por haber sido alcanzados por proyectiles enemigos o explotados por una mina, sino por fallas de componentes y ensamblajes (principalmente motores). Nikita Melnikov en su trabajo sugiere que algunas de las pérdidas pueden atribuirse al bajo nivel de calificaciones de la tripulación, pero incluso teniendo esto en cuenta, el porcentaje de pérdidas no relacionadas con el combate es demasiado alto. Sin embargo, estos fallos de funcionamiento del KV y del T-34 bien podrían eliminarse en el campo, a veces simplemente reemplazando la unidad o el conjunto. Pero fue inútil luchar con la calidad insatisfactoria de la armadura en el T-34 en la parte delantera: los cascos blindados se cocinaron con acero de baja viscosidad, que, cuando fue golpeado por proyectiles enemigos, causó grietas, delaminación y desconchado. A menudo, se formaban grietas en las máquinas nuevas, lo que reducía drásticamente las posibilidades de que la tripulación tuviera un resultado favorable cuando un proyectil alemán golpeaba una grieta o un área de blindaje adyacente.
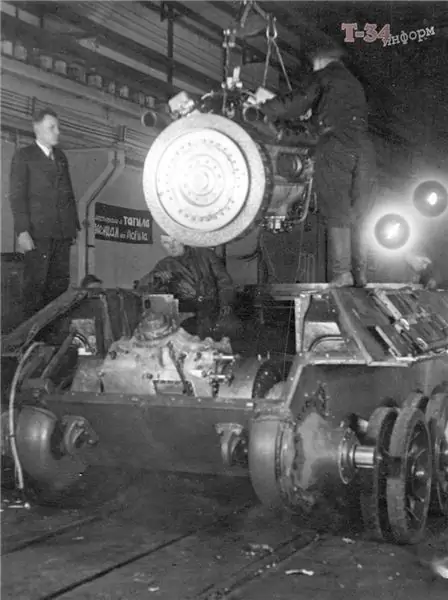
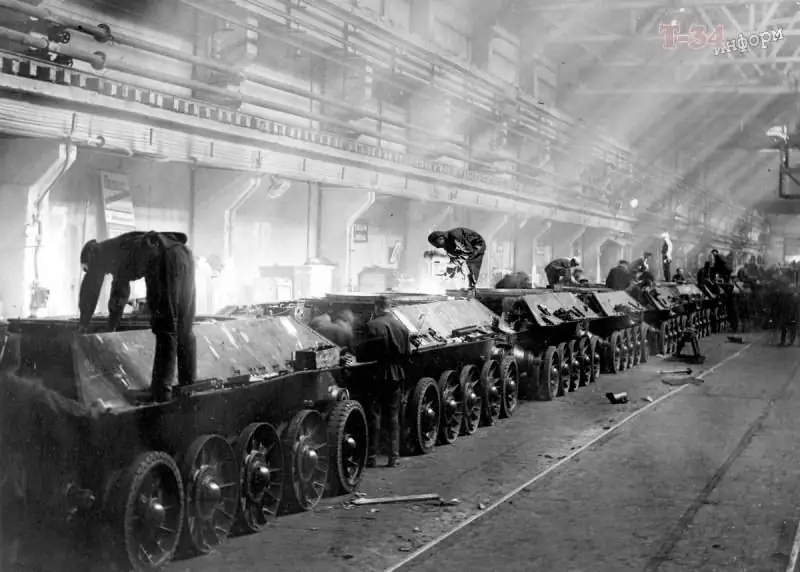
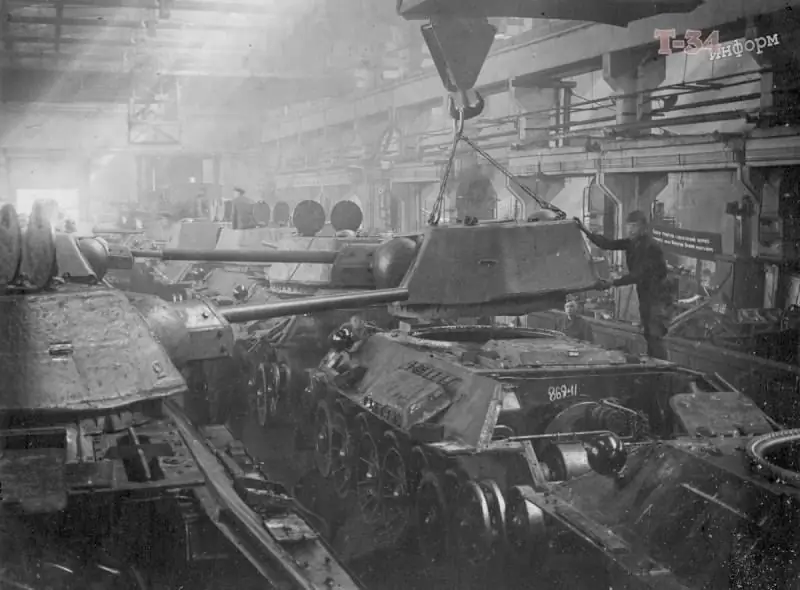
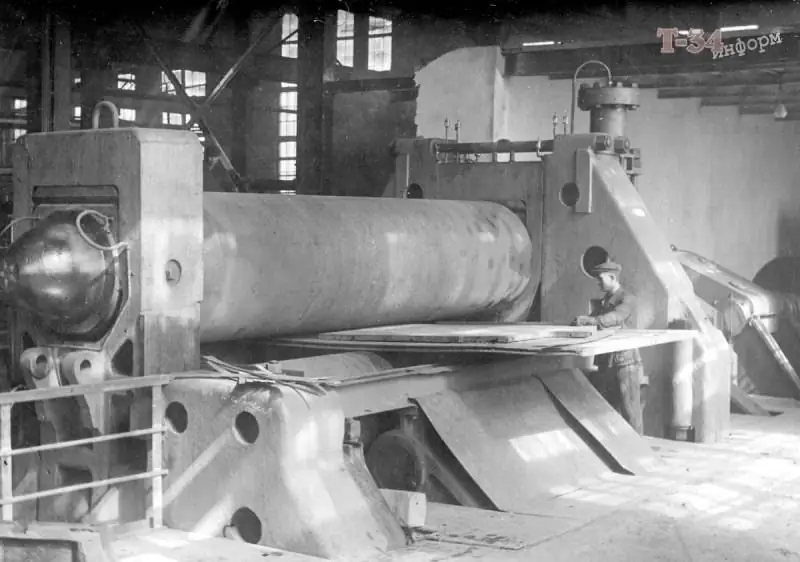
Las primeras llamadas alarmantes sobre la llegada de unidades T-34 con grietas sonaron en mayo de 1942: la fábrica # 183 recibió reclamos por 13 vehículos ese mes, por 38 tanques en junio y por setenta y dos T-34 en los primeros diez días de Julio. … El gobierno no pudo guardar silencio en este caso, y el 5 de junio el Comité de Defensa del Estado adoptó una resolución "Sobre la mejora de los tanques T-34". Al mismo tiempo, se ordenó a la Fiscalía de la URSS que investigara las razones de esta disminución en la calidad de los tanques.
En el curso del trabajo, los investigadores, en particular, descubrieron numerosos hechos de robo de productos de la dieta de los trabajadores de las empresas de la industria de tanques. Los trabajadores de la fábrica simplemente estaban desnutridos. Un ejemplo de esta actitud depredadora se da en una serie de materiales sobre Isaac Zaltsman, el líder más controvertido de las fábricas de tanques.
Entre las empresas que "se distinguieron" en la producción de T-34 defectuosos, la famosa planta de Nizhny Tagil ocupó el primer lugar. Además, el pico en el lanzamiento de productos defectuosos cayó justo en el momento del liderazgo del mencionado Zaltsman. Sin embargo, el director de la empresa, como recordamos, no fue degradado, sino que fue nombrado Comisario del Pueblo de la industria de tanques de inmediato. Obviamente, las autoridades decidieron culpar a los más altos escalones de Vyacheslav Aleksandrovich Malyshev, el primer comisario popular de la industria de tanques de la URSS. Es cierto que la sobriedad llegó un año después, en el verano de 1943, Malyshev fue nuevamente puesto en el lugar del comisario del pueblo, que mantuvo hasta el final de la guerra.
La oficina del fiscal en el curso del trabajo en las empresas evacuadas de la industria de tanques, además de la existencia medio hambrienta de los trabajadores de la fábrica, reveló otro problema de la calidad insatisfactoria de los tanques: una grave violación del ciclo de producción.
Simplificación a expensas de la calidad
Como saben, la planta de Mariupol que lleva el nombre de Ilich no pudo ser defendida, terminó en manos del enemigo, y con una masa de equipo tecnológico que no lograron evacuar. Fue esta empresa (la única en el país) que fue capaz de producir cascos blindados completos para el T-34 de acuerdo con todos los estándares. En los Urales, ni una sola planta podía ofrecer tal cosa, por lo que el equipo de investigación del Instituto Blindado (TsNII-48) comenzó a adaptar las prácticas de Mariupol a las realidades de las fábricas evacuadas. Para la producción de armaduras de alta calidad en los volúmenes requeridos por GKO, hubo una aguda escasez de hornos térmicos, por lo que el instituto desarrolló un nuevo ciclo de endurecimiento de piezas de armadura. En Mariupol, la hoja de la armadura primero se endureció, luego a altas vacaciones, luego de nuevo a endurecerse. Finalmente, siguieron unas pocas vacaciones. Para acelerar la producción, inicialmente se canceló el primer endurecimiento y luego el revenido alto, lo que afecta directamente la tenacidad del acero de la armadura y reduce la probabilidad de agrietamiento. Además, entre las medidas necesarias, según los especialistas del Instituto de Armadura, el requisito era cargar no una, sino inmediatamente cuatro o cinco filas de placas de armadura en el horno térmico. Naturalmente, esto resultó ser mucho más rápido, pero la calidad final de las losas fue muy heterogénea. Curiosamente, el Instituto Blindado decidió posteriormente cancelar el procedimiento de templado bajo, que reduce las tensiones residuales del metal, lo que nuevamente no dejó de afectar negativamente la formación de grietas.
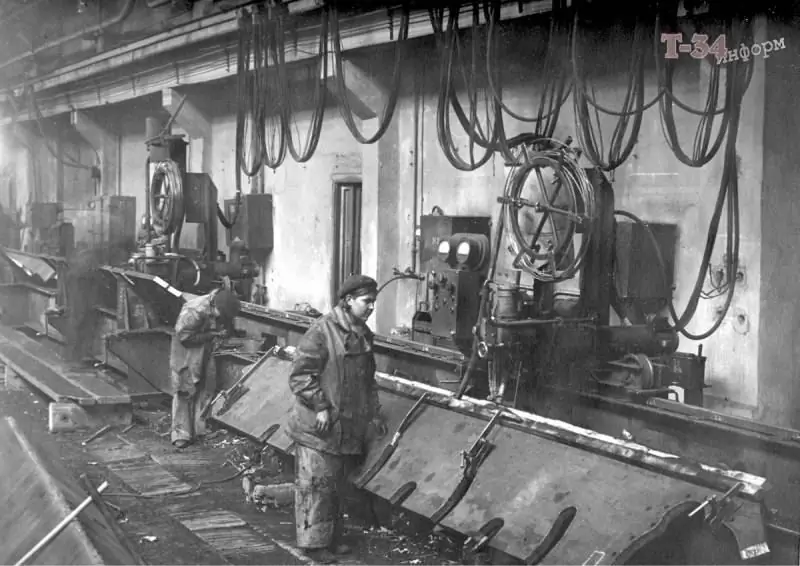
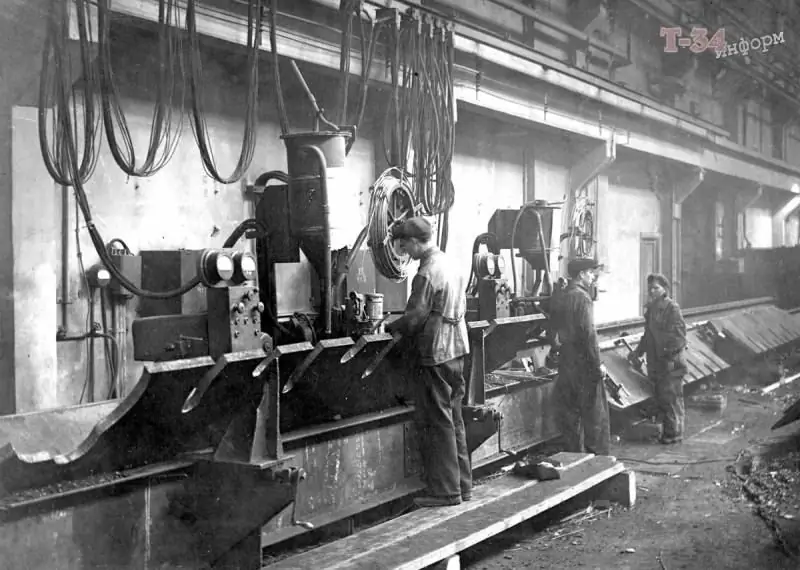
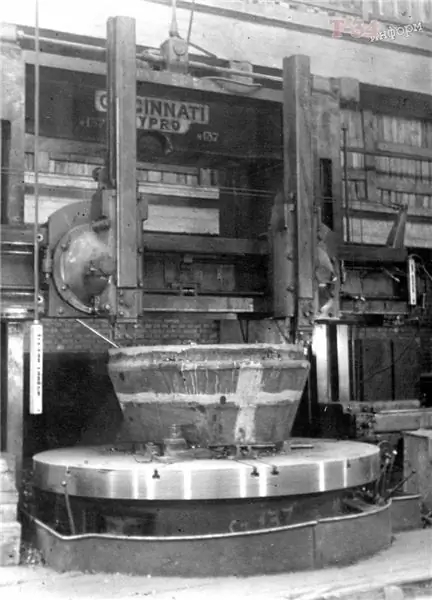
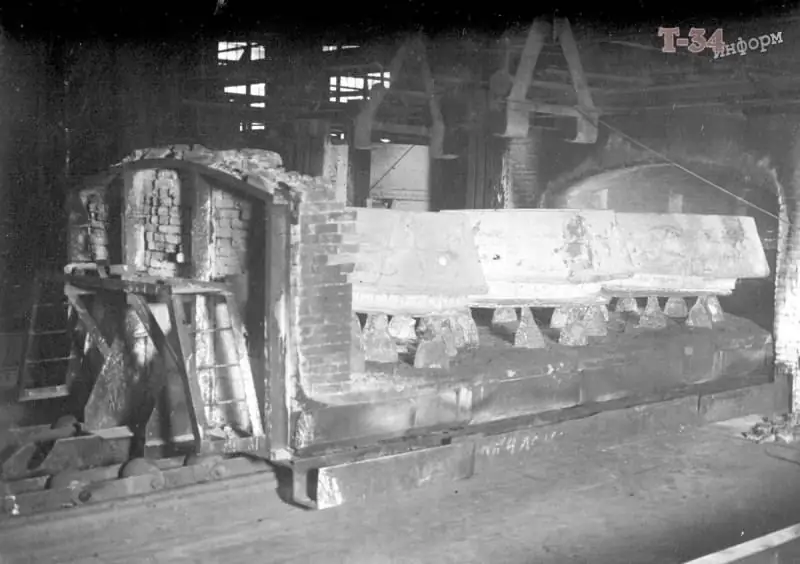
No se puede cortar acero endurecido con cortadores de gas: esta tesis es conocida por todos, pero las realidades de la producción de cascos blindados T-34 obligaron a recurrir a este método impopular. La punta era de acero 8C, que se expandía después del temple y, naturalmente, esto obligaba a los trabajadores de la fábrica a cortarla con quemadores de alta temperatura. Se perdió el punto de endurecimiento de la armadura en el área de corte.
No vale la pena argumentar que las recomendaciones para mejorar el proceso de producción fueron solo negativas para la calidad de la armadura. Entonces, una verdadera innovación en el ensamblaje de los cascos de los tanques T-34 fue la soldadura de placas de blindaje "en una espina" en lugar de las antiguas "en la cerradura" y "en un cuarto". Ahora, las partes acopladas no se cortaron entre sí, sino que se superpusieron parcialmente entre sí. Solo esta decisión redujo seriamente el volumen de horas-máquina por caja de 198,9 a 36.
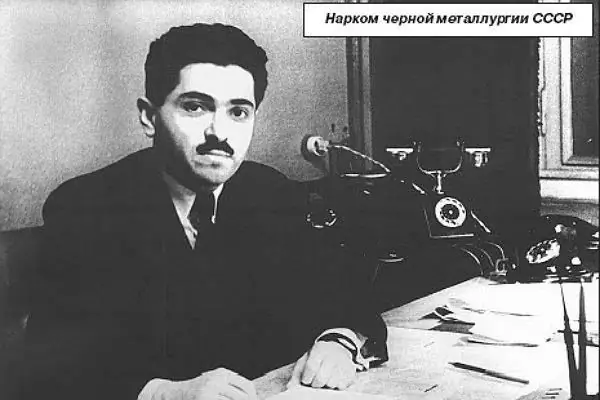
El principal proveedor de láminas de acero defectuosas para las fábricas que producían T-34 era la planta Novo-Tagil del Comisariado del Pueblo de Metalurgia Ferrosa. Al principio, fue interrumpido por suministros de la planta de Mariupol, y cuando se cambió a la suya propia, llegó una corriente de quejas del frente y de las fábricas. En particular, en la composición de la armadura 8C de esta empresa hubo serias discrepancias con las especificaciones técnicas (TU) en el contenido de carbono, fósforo y silicio. En general, hubo dificultades con TU. La Comisaría Popular de Metalurgia Ferrosa no acordó preservar la UT de acuerdo con las normas de Mariupol, en las que el fósforo, en particular, no debe ser superior al 0,035%. A principios de noviembre de 1941, el Comisario del Pueblo de Metalurgia Ferrosa, Ivan Tevosyan, aprobó nuevos estándares para el fósforo, que aumentaron el contenido posible al 0,04% y del 4 de abril al 0,045%. Es de destacar que los historiadores aún no tienen consenso sobre este, por supuesto, un factor importante en la calidad del acero blindado. Nikita Melnikov, en particular, menciona que la planta de Novo-Tagil, por el contrario, a mediados de 1942 redujo la proporción de fósforo de 0, 029% a 0, 024%. Parece que diferentes científicos encuentran diferentes razones para la aparición de T-34 defectuosos en el frente. Sea como fuere, en ocasiones no se observaron las normas indicadas para el contenido de elementos químicos en la composición del acero. Fue difícil para las fábricas establecer una simple uniformidad de los productos laminados suministrados. La fiscalía también reveló que en las empresas de metalurgia ferrosa en hornos de hogar abierto, el acero blindado estaba "poco cocido", en lugar de 15-18 horas en realidad, no más de 14 horas.
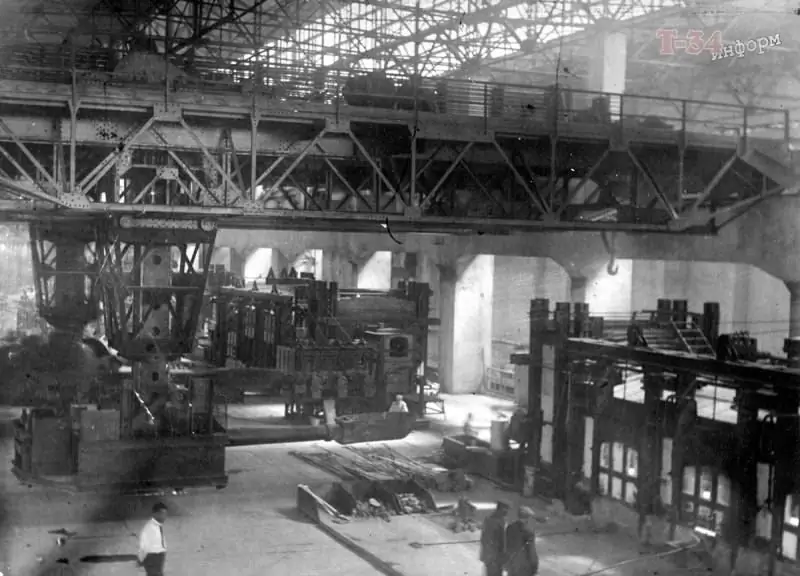
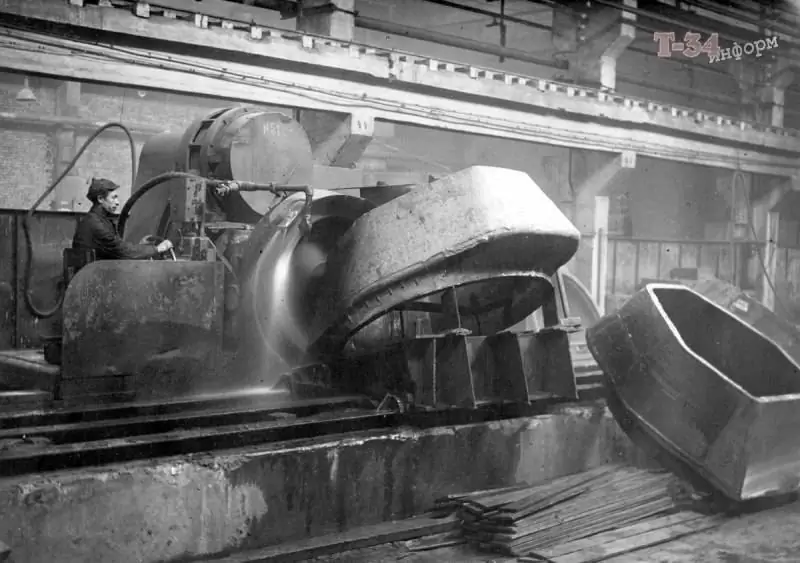
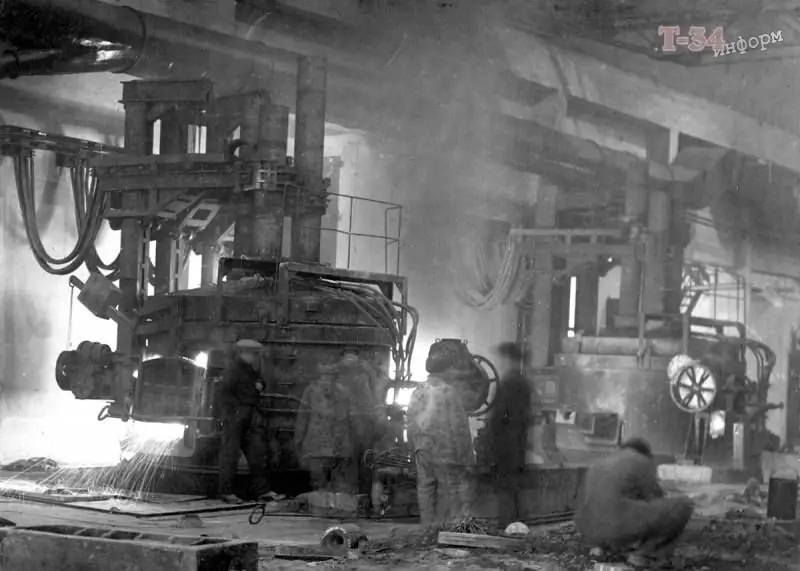
Cuando la información sobre las causas del agrietamiento en los cascos del T-34 llegó a Molotov, las comisarías populares de metalurgia ferrosa y la industria de tanques comenzaron a traspasar la responsabilidad entre sí. Por un lado, la razón principal fue el alto contenido de fósforo en las placas de blindaje, por otro, graves violaciones de la tecnología de producción de cascos en las fábricas de tanques.
Como resultado, TsNII-48 estuvo involucrado en el trabajo para combatir las grietas en el T-34 (aunque indirectamente fue culpable de su apariencia). El conjunto de medidas propuestas por el instituto recién a fines de 1943 permitió eliminar algunos de los comentarios. Y la mejora en la calidad de la producción de acero en las empresas de metalurgia ferrosa permitió reducir la proporción de rechazos del 56, 25% en 1942 al 13, 30% en 1945. Las empresas no alcanzaron el nivel cercano al 100% hasta el final de la guerra.