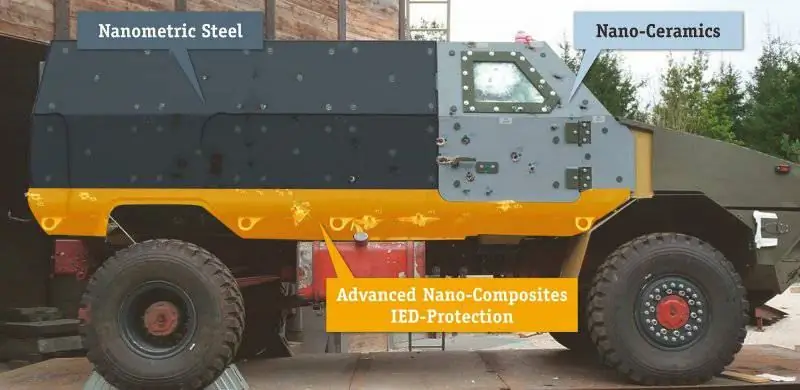
El Iveco MPV utiliza las últimas soluciones de protección IBD Deisenroth, principalmente basadas en nanotecnología
Armadura pasiva: la última barrera
Los cascos de los vehículos blindados todavía están hechos de acero, al que se atornillan kits de blindaje adicionales. Sin embargo, cuanto más pueda ofrecer el diseño básico en términos de protección balística y explosiva, mayor será el nivel final de protección. Además, incluso con la instalación de sistemas de protección activa que destruyen los proyectiles atacantes incluso al acercarse, los fragmentos de alta energía resultantes pueden causar daños graves al vehículo, que nuevamente requiere una buena protección básica
La empresa sueca SSAB es uno de los especialistas de renombre en el campo de los materiales de blindaje, y su familia de aceros de blindaje Armox es bien conocida en todo el mundo. La familia incluye seis tipos diferentes, el número en la designación del grado de acero indica la dureza Brinell promedio. Si bien la dureza afecta directamente la protección balística, la dureza es necesaria para absorber la energía de la explosión, dos características que, de hecho, no pueden existir juntas. La conformabilidad exacerba este conflicto, ya que los aceros de alta resistencia son generalmente menos conformables y a menudo tienen problemas de soldabilidad.
Con el tiempo, las características balísticas de los aceros SSAB mejoraron gradualmente: en 1990, se necesitaba acero Armox 500T con un espesor de 9 mm para detener el proyectil M193 / SS92 que volaba a una velocidad de 937 m / s, pero diez años después con el Armox Aleación 600T, solo se necesitaban 6 para detener mm. Otros diez años y 4.5 mm Armox Advance hace lo mismo, aunque el número ya no vale la pena, ¡ya que la dureza está más allá de la escala Brinell! Desde los 70,7 kg / m2 iniciales, SSAB ha logrado reducir el peso a 47,1 kg / m2 en diez años y hasta 35,3 kg / m2 en la próxima década. Según los expertos de SSAB, no se esperan más disminuciones significativas, la cifra real para 2020 es de 30 kg / m2. El departamento de I + D de la empresa está trabajando más en mejorar la tenacidad y conformabilidad del material existente que en su dureza, especialmente porque la explosión es la principal amenaza en la actualidad. Su acero Armox 440T 420-480 HB Brinell ha sido apodado como el devorador de energía preferido, y su dureza hace que sea fácil obtener cualquier forma, como un fondo sólido. Incluso el acero Armox 500T más duro, con una dureza de 480-540 HB, se considera un material de protección contra explosiones.
Como se mencionó anteriormente, la característica principal de Armox Advanced es la dureza, por lo que SSAB considera este acero como una cerámica de facto. Por ello, la empresa recomienda encarecidamente no moldearlo ni soldarlo, ya que no se debe calentar por encima de los 100 ° C para mantener su dureza. Cómo lograr niveles similares de protección y peso en el futuro con materiales más moldeables es una tarea muy difícil en la actualidad.
Entre los nuevos aceros blindados, por supuesto, cabe destacar Super Bainite, introducido en el otoño de 2011. Desarrollado por el Laboratorio de Ciencia y Tecnología de Defensa DSTL del Reino Unido, el nuevo acero se fabrica en Tata Steel UK. Presenta un rendimiento mucho mejor que el acero blindado estándar. Estas características no son solo consecuencia de la composición química, sino también del proceso de fabricación, en particular del tratamiento térmico con enfriamiento con aire y sales fundidas. El producto final tiene el doble de rendimiento balístico que la armadura homogénea enrollada.
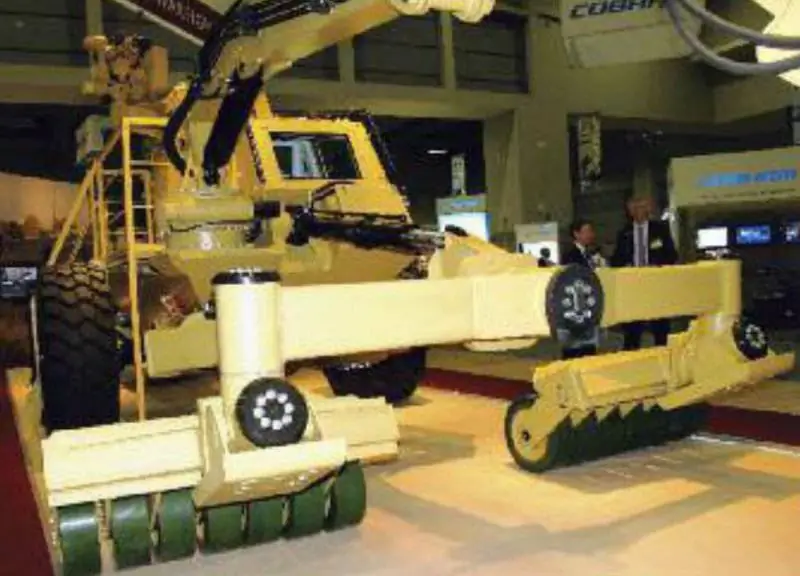
La empresa sudafricana Aardvark Perroc utiliza ampliamente acero SSAB Armox 500 en sus productos. Esto demuestra que incluso este acero de alta dureza es capaz de absorber grandes cantidades de energía.
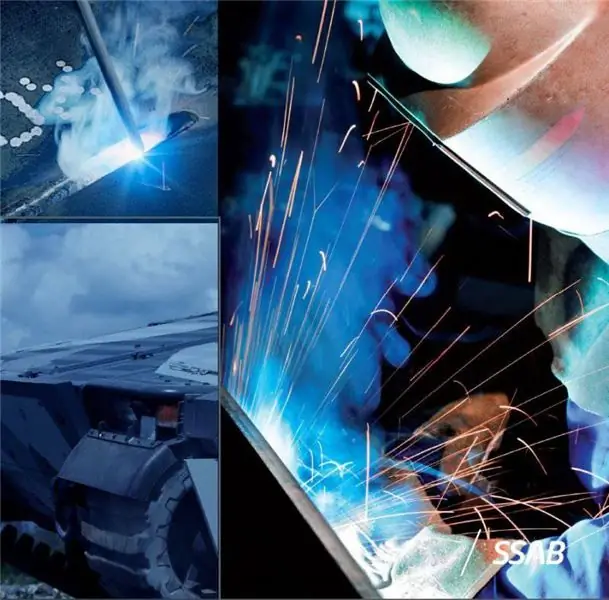
SSAB fabrica formas complejas a partir de su acero Armox 440T, a menudo denominado "devorador de energía". Es muy adecuado para estructuras expuestas a IED. SSAB está trabajando actualmente para hacer que sus aceros blindados sean más moldeables.
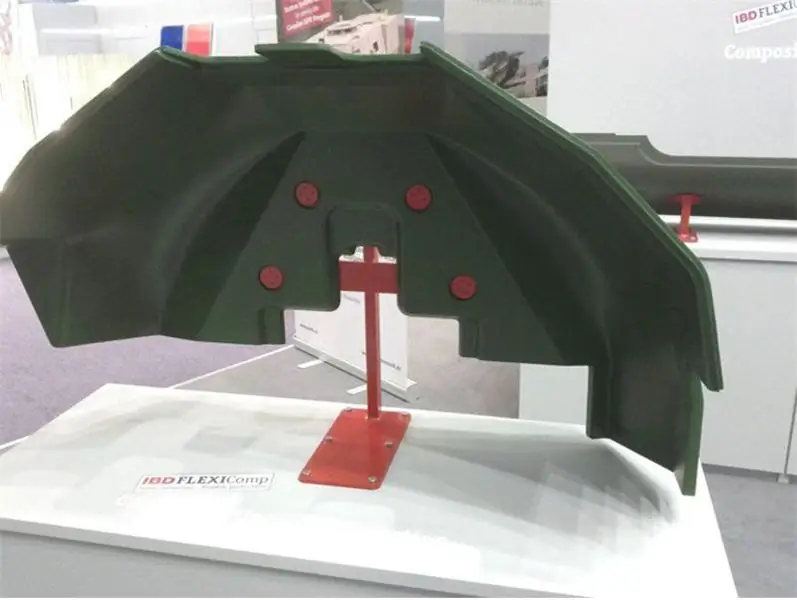
El uso del revestimiento IBD FlexiComp permite la producción de elementos de seguridad volumétricos, reduciendo el número de puntos débiles en el sistema de seguridad general.
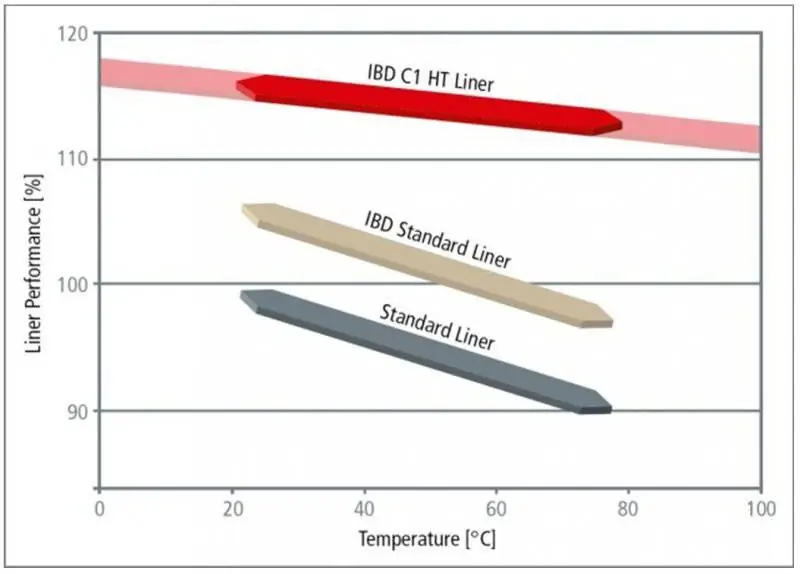
Diagrama de las características de los liners IBD en función de la temperatura. El efecto de las altas temperaturas es una preocupación importante cuando se implementan máquinas en climas cálidos.
En diciembre de 2012, Lockheed Martin UK y la Universidad de Surrey anunciaron un método nuevo y más simple para mejorar la protección y supervivencia de los vehículos blindados. Los científicos han desarrollado un método para tratar materiales cerámicos con el fin de mejorar la fuerza de adhesión de las cerámicas de alúmina y las cerámicas de carburo de silicio a un sustrato compuesto, lo que aumenta significativamente la resistencia de la armadura. La colocación de placas de cerámica en su respaldo siempre ha sido el talón de Aquiles de esta tecnología. Los resultados mostraron que la nueva técnica mejora las fuerzas de tracción. Las pruebas han demostrado que cuando una bala incendiaria perforante de 14,5 mm se dispara contra una placa de blindaje, permanece intacta.
El desarrollo tecnológico sigue siendo el negocio principal de IBD Deisenroth Engineering, mientras que las soluciones pasivas se subcontratan actualmente a Rheinmetall Chempro, 51% propiedad de Rheinmetall Defense y 49% de la familia Deisenroth.
Cuando el Dr. Ulf Deisenroth desarrolló las tecnologías de armadura de cuarta generación para varios tipos de materiales, la tarea era reducir la masa manteniendo el nivel de protección, o viceversa, para aumentar el nivel de protección para una masa determinada, mientras que las nuevas tecnologías prometen ahorros. de más del 40%. Se basan en los últimos avances en el campo de la protección pasiva asociada a los nanomateriales, que incluyen cerámicas nanocristalinas, acero nanométrico y fibras de alta resistencia. En colaboración con los fabricantes de acero, IBD ha desarrollado aceros al nitrógeno de alta resistencia que están casi a la par con los materiales cerámicos estándar. Estos nuevos tipos de aceros se pueden aplicar a elementos estructurales, mientras que pueden lograr un ahorro de peso aún mayor si se utilizan en las primeras etapas de diseño. En cuanto a las fibras de alta resistencia, por ejemplo, IBD C1 HT Liner, tienen características que son casi un 20% más altas no solo en comparación con el forro estándar, sino incluso un 10% más alto que otros forros de IBD; el deterioro de sus parámetros con el aumento de las temperaturas también es más lento, lo que es especialmente importante dadas las temperaturas extremas en los campos de batalla modernos. Además de los aceros y nanocerámicas a nanoescala utilizados en máquinas de nuevo desarrollo, IBD también ha desarrollado nuevas soluciones de materiales compuestos que permiten la producción de elementos con geometrías curvas complejas, lo que permite alcanzar una cobertura del 100% del área protegida casi sin espacios balísticos.. Esta solución se utiliza en particular en la producción de elementos de fondo, donde el más mínimo espacio puede comprometer toda la protección.
IBD también ha tenido éxito en el desarrollo de laminados de nanocompuestos que tienen una resistencia tan aumentada que pueden reemplazar partes estructurales de una máquina al mismo tiempo que sirven como protección balística de alto nivel. Debido a su baja densidad superficial, el peso total de este nivel de protección se reduce así significativamente. Estos compuestos se basan en los materiales de nanotecnología mencionados anteriormente de IBD. Se han desarrollado procesos de unión específicos y se utilizan para fabricar laminados nanocompuestos de materiales estructurales, conocidos como IBD FlexiComp, con mayor resistencia estructural y rendimiento balístico. Con un 10% menos de densidad en comparación con los laminados estándar, las propiedades elásticas de estos materiales son dos veces más altas. Esta alta resistencia les permite integrarse en el diseño de la máquina, mientras que las características balísticas le permiten hacer frente a amenazas de alto nivel, mientras que los materiales FlexiComp tienen un buen potencial para la reducción de peso. Su uso se puede materializar en dos enfoques diferentes. Un enfoque directo es usarlos para protección contra minas y artefactos explosivos improvisados como blindaje adicional en pasos de rueda, guardabarros, placas de minas y pisos internos espaciados. Al moldear piezas volumétricas, pueden reemplazar otras soluciones, como ensamblajes ensamblados por soldadura o atornillado. El segundo enfoque es la integración de piezas compuestas como escotillas, escotillas de motor, puertas de popa y rampas. Constituyen una gran proporción de la superficie total del vehículo y, como resultado, la reducción absoluta de peso será muy significativa. Para STANAG 4569 Nivel 4, esta reducción de peso es de 1500 kg para una máquina 8x8 (ver tabla). En términos de costos de fabricación, los procesos desarrollados por IBD permiten la producción de piezas compuestas sin el uso de autoclaves, proporcionando importantes ahorros de costos, especialmente para componentes grandes, su costo es comparable al costo de los componentes producidos utilizando tecnologías estándar.
Estos componentes son fabricados actualmente por Rheinmetall Chempro, cuya tarea es dominar las tecnologías de ingeniería IBD Deisenroth, desarrollarlas en un proceso de producción para lograr precios competitivos, desarrollar soluciones especializadas y seguirlas hasta el proceso de calificación de la máquina. Las entregas de componentes fabricados con las últimas tecnologías avanzadas comenzaron a principios de 2013, principalmente máquinas AMPV de KMW-Rheinmetall y vehículos de protección media de Iveco DV-KMW. Más de una docena de fabricantes de equipos originales de todo el mundo pronto recibirán componentes que les permitirán reducir realmente el peso de sus máquinas, lo que aumentará la carga útil y reducirá los costos del ciclo de vida, dijo la División de Protección de Rheinmetall.
El portafolio pasivo de Rheinmetall Chempro incluye varias versiones de la familia Amap (Advanced Modular Armor Protection). Esta familia utiliza la última tecnología desarrollada por IBD. Los productos Amap generalmente se combinan para brindar la protección deseada contra una amplia variedad de amenazas. Entre los diversos productos opacos, vemos la solución balística Amap-B, que brinda protección contra armas pequeñas y municiones de calibre medio, protección contra minas Amap-M, Amap-IED diseñado para combatir IED, revestimientos Amap-L que protegen el compartimento de combate. absorbiendo metralla secundaria, Amap-SC contra proyectiles HEAT y, finalmente, la solución Amap-X, que protege contra amenazas típicas de las condiciones urbanas.
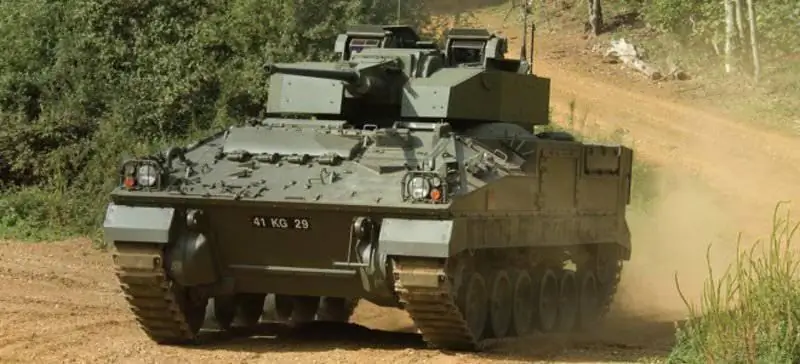
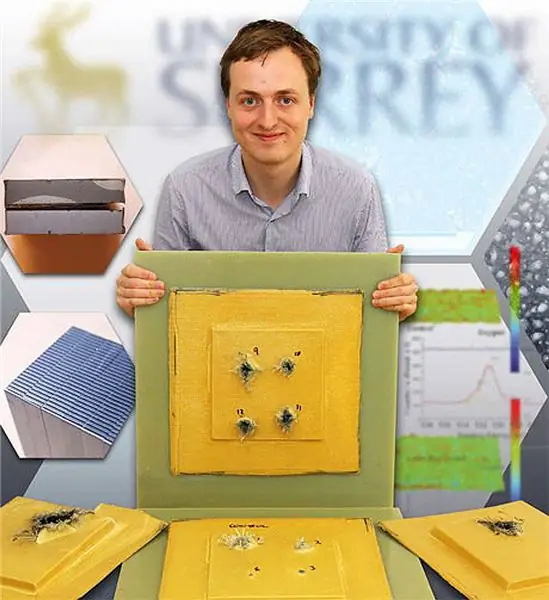
La nueva tecnología de unión desarrollada por Lockheed Martin UK y la Universidad de Surrey podría mejorar significativamente la protección de vehículos blindados como el Warrior BMP (arriba)
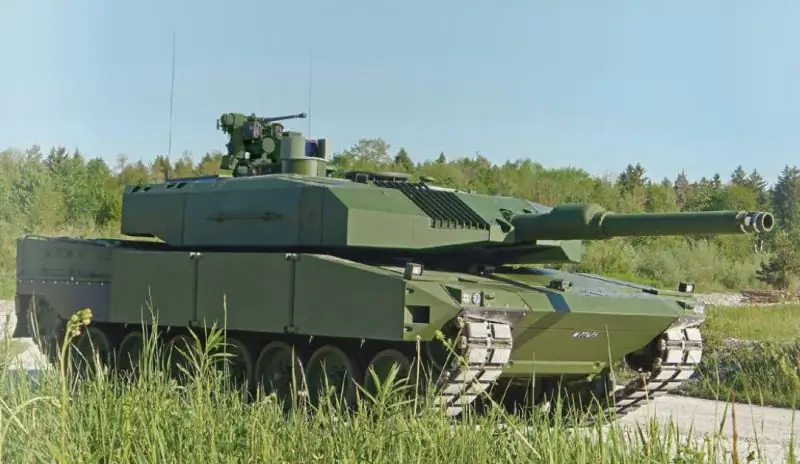
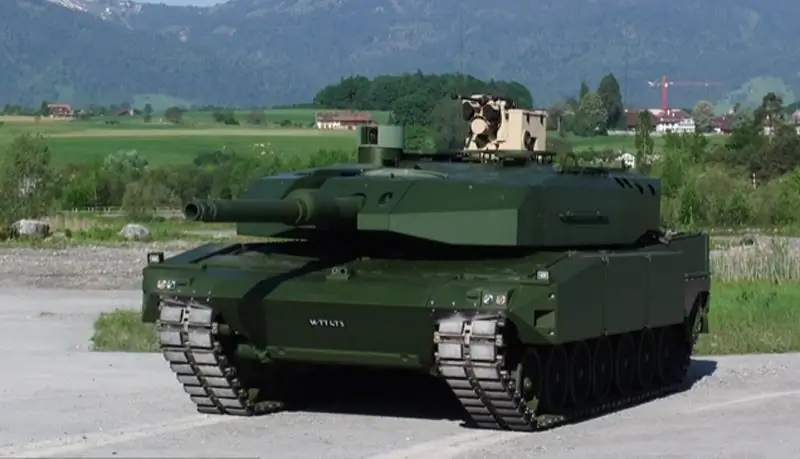
Módulos SidePro-ATR adicionales para MBT Leopard
Cabe señalar que dentro del Grupo Rheinmetall, otra empresa se dedica a la protección pasiva, Rheinmetall Ballistic Protection GmbH, que recibió su nuevo nombre el 1 de enero de 2013. Anteriormente, se llamaba Rheinmetall Verseidag Ballistic Protection GmbH. De propiedad total de Rheinmetall, esta firma se especializa en el diseño y fabricación de soluciones de blindaje para vehículos militares ligeros que utilizan materiales como cerámica, metales avanzados y tejidos especiales.
Aunque Ruag Defense todavía tiene soluciones de protección dinámica (blindaje activo-reactivo) en su cartera, ya no se ve a los ojos de los consumidores como una empresa ultramoderna capaz de aumentar la capacidad de supervivencia de vehículos medianos y pesados. En este sentido, la empresa suiza centró su atención en perfeccionar soluciones completamente pasivas que puedan hacer frente a cargas cinéticas y perfiladas. El sistema SidePro-ATR va mucho más allá de la agresividad del RPG-7, ya que puede manejar las cargas con formas utilizadas en escenarios simétricos, mientras que la versión básica garantiza protección balística de nivel 5. SidePro-ATR se mostró por primera vez al público en 2012, este sistema es escalable y, por lo tanto, se puede utilizar tanto en vehículos blindados de transporte de personal como en tanques. En su versión básica, tiene un espesor de 400 mm, y su masa es comparable a la masa de una solución reactiva (es decir, aproximadamente 300 kg / m2). Este sistema fue calificado para el tanque Leopard 2A4. El nivel de protección balística se puede incrementar significativamente hasta el punto que el sistema resistirá el impacto de un núcleo alargado de 120 mm, aunque no se proporcionaron datos al respecto.
La escalabilidad de SidePro-ATR permite su uso en escenarios de combate simétricos y asimétricos. Otra solución para combatir la munición cinética y los IED bajo la designación SidePro-KE / IED se probó en el vehículo blindado de reconocimiento Fennek, que está en servicio con Alemania y los Países Bajos. Esta solución, basada principalmente en cerámica, estaba destinada a combatir los artefactos explosivos improvisados de primera generación. Las nuevas bombas al borde de la carretera, utilizadas en varios teatros, generan miles de fragmentos de alta velocidad y, por lo tanto, se necesitan muy buenas características de impacto múltiple. Desde entonces, Ruag ha perfeccionado el sistema KE / IED, alejándose de la cerámica y utilizando bolsas multicapa no expandibles. La nueva solución SidePro-KE / IED, disponible desde 2012, ofrece protección de nivel 4 / nivel 5 contra armas cinéticas y tiene un rendimiento de impactos múltiples extremadamente alto. Suponiendo que el chasis está hecho de acero balístico de 7 mm, un panel de 30 mm podría proporcionar la protección completa requerida, y el sistema KE / IED permite la ganancia de peso más pequeña, dependiendo solo del tipo de vehículo. Esta solución está pendiente con varios fabricantes.
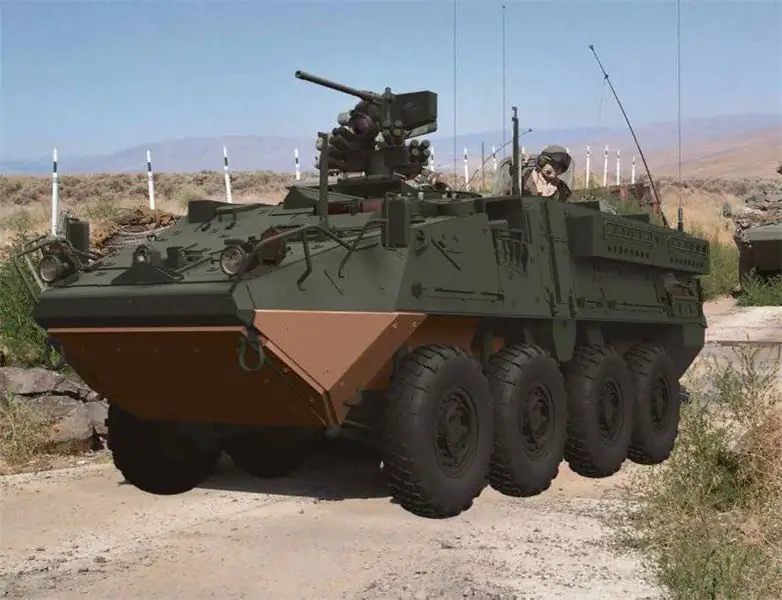
Ruag ha finalizado el SidePro KE / IED. El fotomontaje muestra los elementos de un sistema diseñado para contrarrestar nuevos dispositivos que generan múltiples fragmentos.
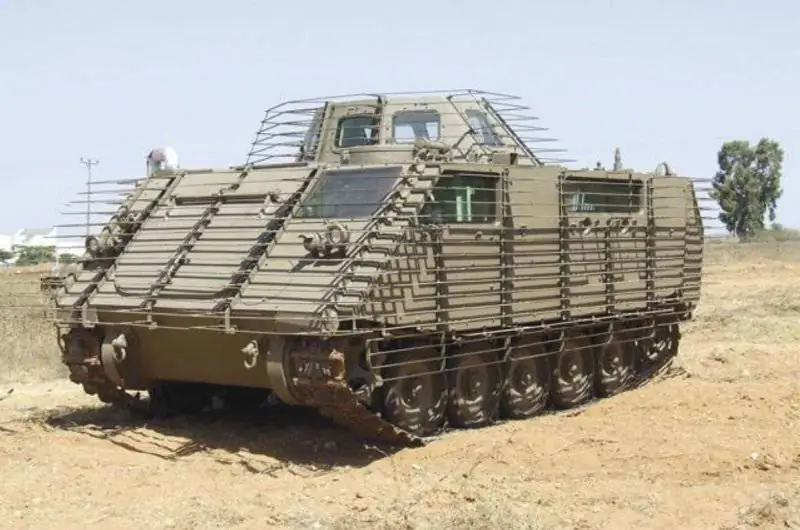
BTR M113, equipado con un sistema pasivo anti-RPG Iron Wall de Israel Military Industries, que combina armadura pasiva y de celosía
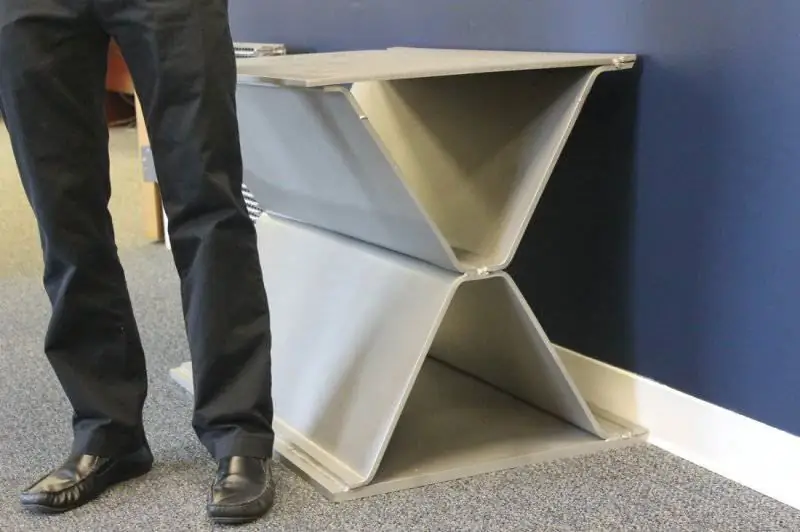
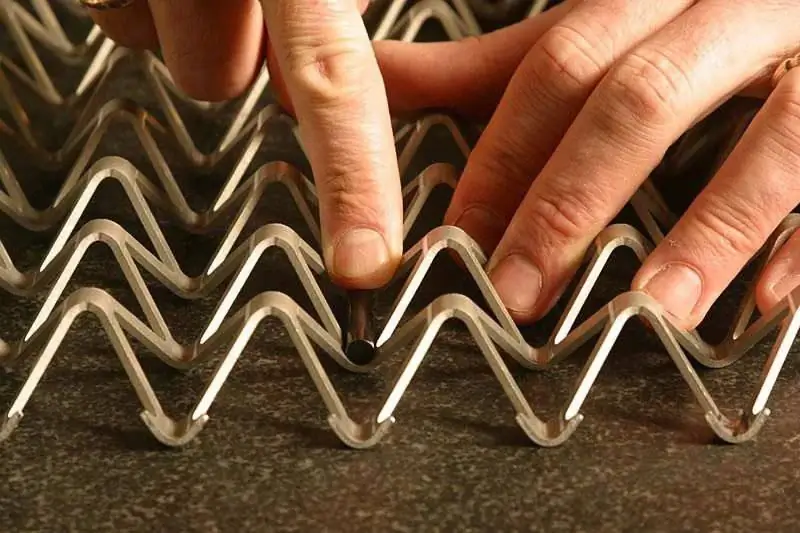
Ceradyne y Cellular Materials International han desarrollado un protector inferior basado en un panal de aluminio CMI MicroTruss que absorbe hasta un tercio de la energía generada por una explosión. A continuación se muestra un primer plano del material MicroTruss.
Ejemplo de reducción de peso para una máquina 8 x 8 con componentes de IBD FLEXICOMP
Peso en kg
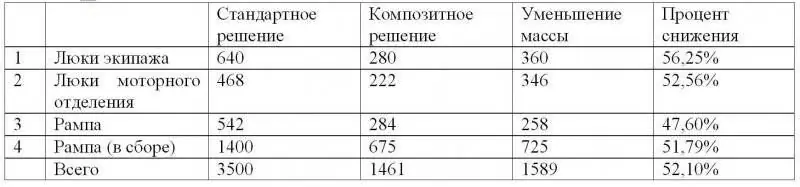
Plasan Sasa sigue siendo uno de los actores clave en la industria de las reservas pasivas. No se dan detalles tecnológicos en esta área, mientras que la empresa está activa tanto en reservas adicionales como en edificios prefabricados. El segundo enfoque se tomó con el desarrollo del Mrap de Navistar MaxxPro y el M-ATV de Oshkosh. "Esto nos permite aumentar la producción utilizando una fuerza laboral sin habilidades de soldadura, ya que nuestro enfoque estilo Lego se basa en bloques que contienen todos los componentes que se pueden ensamblar en un tiempo mínimo", dijo una fuente de la compañía. Algunos de los más de doscientos ingenieros de la empresa están trabajando en nuevas soluciones que podrían resultar de la aparición de nuevos materiales o soluciones geométricas innovadoras. El enfoque de sistemas permanece en el corazón del ciclo de protección.
IMI ha desarrollado recientemente una gama de soluciones pasivas y reactivas para contrarrestar los últimos tipos de IED, incluidos los diversos tipos de "núcleos de choque" EFP o SFF (Fragmentación autoformada) y los últimos modelos de RPG. La empresa ha propuesto una solución pasiva de pared de hierro basada en una combinación de metal y compuestos complementados con una armadura de celosía. Dependiendo del nivel de protección requerido, el espesor puede variar entre 110 y 150 mm y el peso entre 200 y 230 kg / m2. Iron Wall está siendo sometido actualmente a juicios militares con el ejército israelí.
IMI también ofrece su armadura de celosía como sistema independiente. L-VAS (Light Vehicle Armor System - sistema de blindaje para vehículos ligeros) está diseñado para proteger vehículos como los vehículos blindados de transporte de personal. Para reducir el peso, el sistema se basa en materiales compuestos y elementos reactivos, estos últimos contienen un mínimo de materiales energéticos. Esto reduce las pérdidas indirectas y el tipo de material evita el riesgo de detonación secundaria de elementos adyacentes. Según IMI, el sistema L-VAS también protege contra rondas perforantes de 14,5 mm y fragmentos de artillería. El sistema ha sido completamente calificado en Israel para su APC M113 y tiene una gravedad específica de aproximadamente 200 kg / m2.
También se ofrece un sistema de rompeolas más pesado. Esta armadura reactiva, compuesta por elementos metálicos y compuestos, está diseñada para combatir tres amenazas principales: RPG, SFF y EFP. IMI ha llevado a cabo pruebas exhaustivas y actualmente está procediendo con las calificaciones para comenzar a producir una solución con un espesor de 350 a 400 mm y un peso de 430 a 450 kg / m2 a fines de 2013.
Ceradyne es otro jugador importante en reservas pasivas. Según Mark King, presidente de Ceradyne, el acero sigue siendo el material principal en el negocio de reservas, con el objetivo de mejorar el rendimiento y reducir los costes. "En los Estados Unidos, el factor determinante es principalmente el costo de adquirir un vehículo, no el costo de su vida útil, y esto va en contra de las actualizaciones", dijo King en la conferencia de AUSA de 2012. Mientras que en los Estados Unidos, el énfasis estaba en cantidad, lo que llevó a los desarrolladores europeos de sistemas de protección por delante de los estadounidenses. Sin embargo, King enfatizó que Estados Unidos está progresando actualmente, enfocándose principalmente en la protección antiexplosiva de los bajos, ya que la protección balística se ve como un problema resuelto. King valora positivamente el interés del ejército estadounidense, nuevamente demostrado en resolver el problema de proteger la parte inferior de vehículos como, por ejemplo, el Humvee ($ 20 millones solo para desarrollo). Ceradyne es uno de los que definitivamente competirá por un contrato para su modernización. El requisito proporciona la máxima protección con importantes ahorros de peso para reducir el impacto en el rendimiento de la máquina.
Ceradyne ha desarrollado una solución MicroTruss de Cellular Materials International Inc (CMI). Este material de aleación de aluminio poroso tiene una densidad de 58 kg / m2 en comparación con la densidad de 112 kg / m2 de una solución de metal monolítico equivalente. Esta solución se diferencia en el ángulo "V" del cuerpo igual a sólo 5 °, que es suficiente para reflejar la onda expansiva y tiene una masa de 300 kg. MicroTruss garantiza la absorción de hasta un 30% de la energía de explosión, lo que no solo limita el impacto en la cápsula de la tripulación, sino que también reduce el movimiento vertical del vehículo. Ceradyne también está muy involucrado en el programa de reservas Flyer Gen.2, que tiene como objetivo el proyecto de las Fuerzas de Operaciones Especiales para el GMV 1.1. Para mantener la transportabilidad dentro de los helicópteros V-22, CH-47D y CH-53E cuando la masa y el ancho deben mantenerse dentro de ciertos límites, la compañía ha desarrollado un kit que proporciona un nivel B6 (.357 Magnum) de protección balística para las puertas y techo.
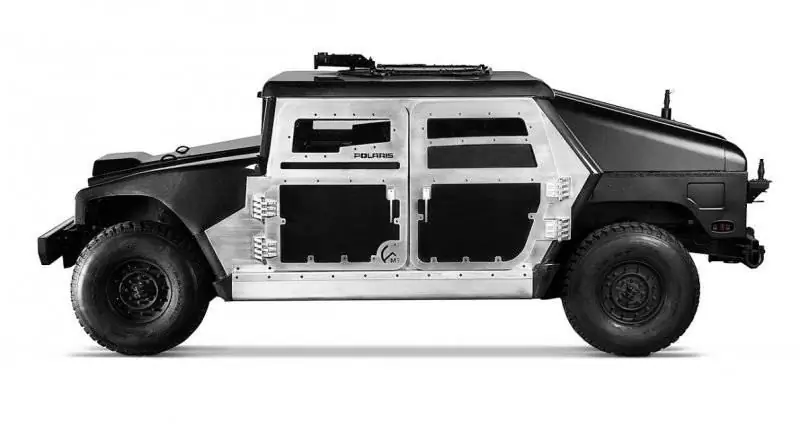
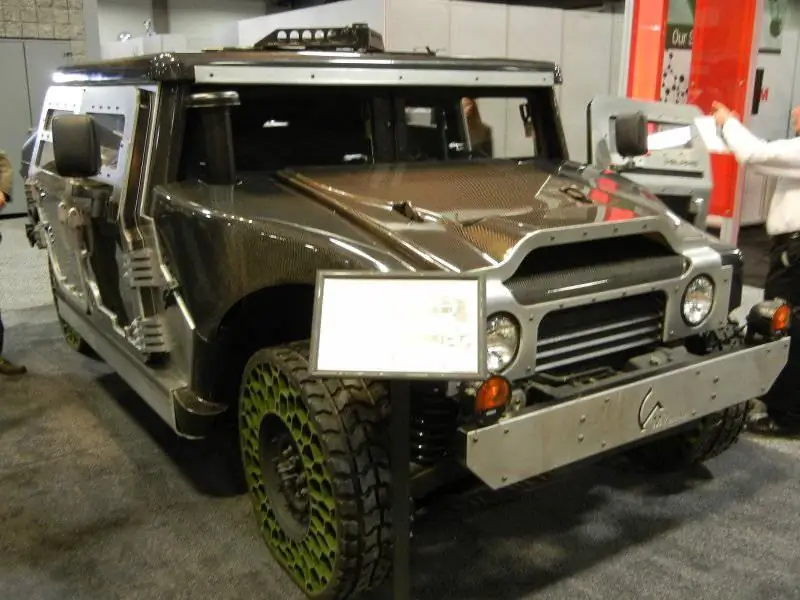
Polaris Defense y M9 Defense Armor Technology han desarrollado una armadura estructural compuesta de acero híbrido que puede reducir significativamente el propio peso del Humvee mientras mantiene los niveles de protección. El prototipo que se muestra a la derecha tiene un peso en vacío de solo 3400 kg, que es casi un 50% menos que el Humvee con protección de Nivel 3.(Tenga en cuenta las ruedas del automóvil en la parte inferior)
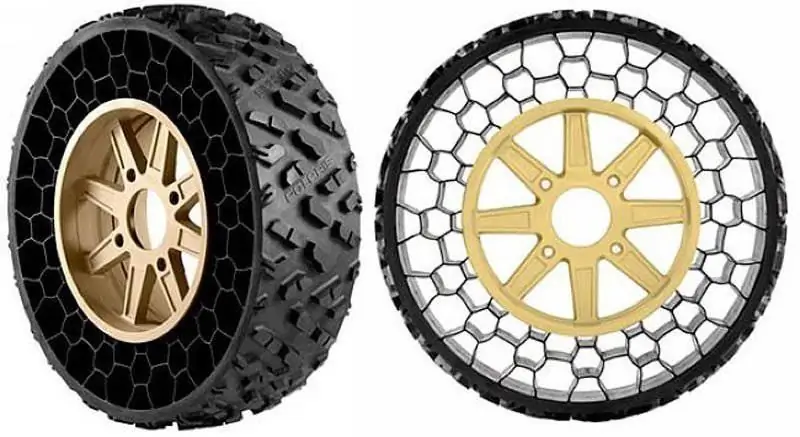
La protección también consiste en no quedarse en el campo de batalla en caso de que se pinche una rueda. Las ruedas no neumáticas de Polaris Defense garantizan una durabilidad significativamente mejor en comparación con los neumáticos estándar y pueden soportar una bala de 12,7 mm. Actualmente, están disponibles no solo para automóviles, incluida la clase Hummer, sino que ahora estas ruedas también se están desarrollando para los automóviles más pesados de la clase Mraps.
Ceradyne también participa en el programa de transporte de personal de los Marines en asociación con Lockheed Martin y Patria en un vehículo del Cuerpo de Infantería de Marina basado en el Patria AMV finlandés. Cabe destacar que el 28 de noviembre de 2012 se anunció que Ceradyne fue adquirida por el Grupo 3M, lo que le permitirá invertir más en I + D y soluciones innovadoras.
La integración de diseño y protección es una solución muy buscada para vehículos ligeros. En AUSA 2012, Polaris Defense mostró un prototipo de vehículo Humvee con un nuevo concepto desarrollado en colaboración con M9 Defense. El desafío es reducir el peso en vacío mientras se mantienen y aumentan los niveles de protección. Para hacer esto, el equipo de Polaris-M9 eliminó toda la armadura superior para echar un vistazo al concepto de armadura estructural. Luego se quitó todo del automóvil, solo se dejó un chasis desnudo y luego se le colocó una estructura híbrida liviana (material compuesto de acero). Esta armadura estructural puede brindar protección de Nivel 3 con una masa de 70 kg / m2, y con una masa de 83 kg / m2, es capaz de resistir una bala de 12,7 x 99 mm, aunque el grupo Polaris-M9 confía en que puede alcanzar el nivel 3+ (bala perforante de 12, 7 mm). La solución Polaris-M9 también protege el motor. Mientras que el vehículo blindado Hummer estándar pesa aproximadamente 6.350 kg, la solución propuesta permite reducir su peso a 3400 kg. La armadura estructural híbrida utiliza un material no exótico, lo que permite al equipo Polaris-M9 hablar sobre el costo de la nueva solución, comparable al costo de las soluciones actuales. Además, este material se moldea en formas complejas, lo que da como resultado fondos en forma de V sin costuras, entre otras cosas. Lograr la forma deseada se logra mediante el conformado hidráulico, un proceso de alta velocidad que ayuda a reducir los costos. Según el equipo de Polaris-M9, esta tecnología puede reducir el peso en un 40 por ciento.
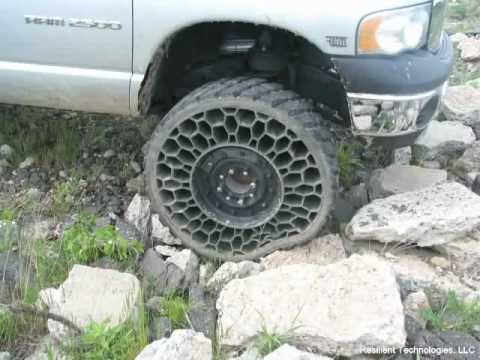
Demostración de ruedas no neumáticas de Polaris Defense
La ecuación de defensa incluye otro término que se relaciona directamente con la movilidad: la rueda. Tras la adquisición de Resilient Technologies, Polaris Defense ahora ofrece ruedas no neumáticas (NPT). El consumo de ruedas es uno de los problemas logísticos más importantes en un motor de turbina y la solución NPT ayudará en muchos casos a solucionarlo. Según el mando de las fuerzas de operaciones especiales en Afganistán, los neumáticos convencionales recorren aproximadamente 1.300 km, mientras que una rueda NPT pinchada por una bala de 12,7 mm puede recorrer más de 8.000 km y, por tanto, desplazar ruedas de repuesto de la cadena de suministro, al tiempo que mejora la calidad de marcha.. Ya se han realizado prototipos NPT para vehículos Hummer. El objetivo actual es un juego de ruedas NPT para la máquina de 7,7 toneladas, que es casi el peso total de la variante de uso general JLTV. Según representantes de la empresa, el modelado mostró que la masa puede alcanzar las 18 toneladas, es decir, las ruedas pueden soportar un coche de la clase Mrap. A medida que aumenta la carga útil, la tecnología sigue siendo la misma y los programas de simulación de la empresa permiten predicciones muy precisas. Lo que cambiará es el material que tiene que adaptarse a la masa, que a su vez aún no ha aparecido en el futuro.