Se sabe que la guerra es el mejor motor del progreso. La industria de tanques de la Unión Soviética dio un vertiginoso salto cualitativo en solo unos pocos años de guerra. La verdadera corona de esto fueron los tanques de la serie IS.
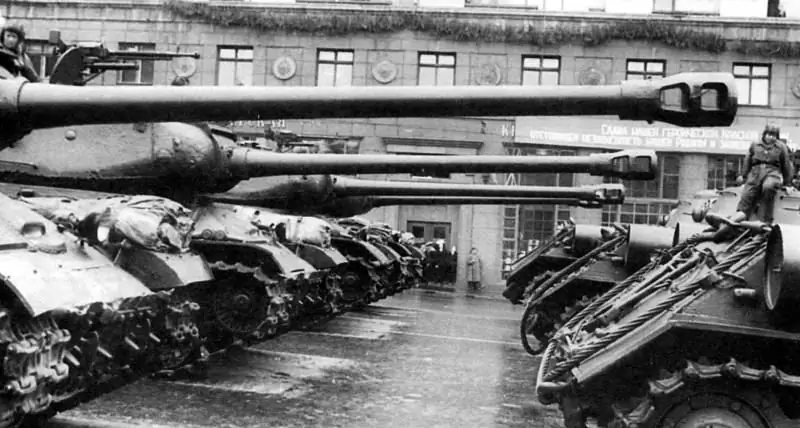
Recetas Magnitogorsk
En la parte anterior de la historia, se trataba de la armadura de fundición de alta dureza 70L utilizada para las torretas de los tanques IS. Los desarrolladores de armaduras de TsNII-48 estaban lejos de tener la primera experiencia en la creación de protección para tanques pesados.
Antes del Kursk Bulge, que se convirtió en un catalizador para el desarrollo de la construcción de tanques pesados domésticos, el principal objeto de modernización era el tanque KV. Inicialmente, todo el trabajo tenía como objetivo reducir la proporción de aditivos de aleación escasos en la composición de la armadura. Incluso el nombre en TsNII-48 apareció con uno apropiado: acero de aleación económica. La armadura original de la marca FD-7954, con la que el tanque KV entró en la Gran Guerra Patriótica, contenía, según requisitos técnicos, hasta 0,45% de molibdeno, 2,7% de níquel y cromo.
A finales de 1941, un grupo de investigadores dirigido por Andrei Sergeevich Zavyalov en el Instituto Blindado creó una receta para el acero FD-6633 o 49C, en la que el molibdeno no requería más del 0,3%, cromo (hasta un 2,3% y níquel). hasta 1, 5%. Teniendo en cuenta que los tanques de la serie KV de la segunda mitad de 1941 a 1943 se recolectaron alrededor de 4 mil copias, uno puede imaginar la cantidad de ahorros reales en la aleación de metales.
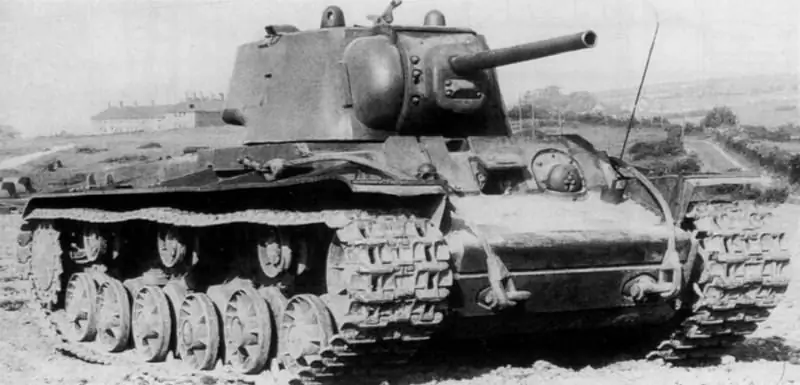
El secreto del exito
El secreto del éxito de los metalúrgicos radica en el estudio de los parámetros de formación de la fractura fibrosa de la armadura, el principal parámetro de resistencia a los proyectiles. Resultó que puede prescindir de una proporción significativa de elementos de aleación simplemente cambiando la velocidad de enfriamiento de la armadura durante el enfriamiento. Pero esto es simple en palabras: cuántos experimentos preliminares y fundiciones tuvieron que hacer los metalúrgicos, solo los archivos ahora clasificados podrán decirlo.
En la Planta Metalúrgica Magnitogorsk en 1941, se obtuvieron los primeros prototipos de acero 49C, que no eran inferiores a la armadura tradicional de "antes de la guerra". En particular, el bombardeo del cañón de 76 mm mostró el pleno cumplimiento de los requisitos tácticos para el tanque. Y desde 1942, solo se utilizó armadura con el nombre 49C para la serie KV. Vale la pena recordar que el consumo de cromo, molibdeno y níquel ha disminuido significativamente.
La búsqueda de nuevas formulaciones de armaduras para equipos pesados no terminó ahí. En 1942 se “solda” el acero GD-63-3, completamente desprovisto de cromo y níquel escasos. Hasta cierto punto, el níquel fue reemplazado por manganeso: su participación aumentó más de tres veces (hasta un 1,43%). Se dispararon prototipos de la nueva armadura. Y resultaron ser bastante adecuados para uso masivo en el diseño del KV. Pero los tanques Klim Voroshilov con armadura de dureza media se estaban retirando. Y el lugar de los vehículos pesados lo ocuparon los vehículos “Joseph Stalin” con blindaje de alta dureza.
Armadura enrollada 51C
Si la armadura de 70L para la torreta IS-2 se podía lanzar, entonces este truco no funcionó con las partes del casco del tanque. Aquí, los ingenieros se enfrentaron a dos problemas a la vez: la creación de armaduras de gran dureza y gran espesor y la necesidad de soldarlas en un casco terminado.
Todos los interesados probablemente ya estén al tanto de los problemas causados por la soldadura de la armadura T-34: existe una alta probabilidad de agrietamiento en el área de las soldaduras. El IS-2 no fue una excepción. Y originalmente se suponía que su cuerpo debía cocinarse a partir de partes finalmente tratadas térmicamente.
Al darse cuenta de las dificultades y peligros que traería una solución tecnológica de este tipo en la operación militar, los especialistas de TsNII-48 cambiaron el ciclo de producción de tanques. Como resultado, en 1943, en la Planta de Construcción de Máquinas Pesadas de Ural y la Planta No. 200 de Chelyabinsk, se decidió cocinar el casco del IS-2 a partir de placas de blindaje que habían pasado solo unas altas vacaciones después de rodar. Es decir, de hecho, el casco de un tanque pesado se ensambló con acero "crudo". Esto redujo en gran medida los defectos de soldadura en la armadura laminada de alta dureza 51C.
El tratamiento térmico final por calentamiento antes del temple ya se realizó en el cuerpo soldado del tanque, habiéndolo previamente reforzado con puntales internos. El cuerpo se mantuvo en el horno durante tres horas. Y luego, en dispositivos especiales, se transfirieron a un tanque de enfriamiento con agua y se mantuvieron en él durante 15 minutos. Además, la temperatura del agua en el tanque de enfriamiento aumentó de 30 a 55 ° C. La temperatura de la superficie del cuerpo después de ser removido del agua fue de 100-150 ° С. Y eso no es todo.
Después del enfriamiento, el cuerpo se sometió inmediatamente a un revenido bajo en un horno de circulación a una temperatura de 280-320 ° С con mantenimiento después de alcanzar esta temperatura durante 10-12 horas. El templado bajo de las torres de fundición de blindaje de 70L se llevó a cabo de forma similar. Curiosamente, el control de grietas en los cascos experimentales del IS-2 duró cuatro meses, cuando los primeros tanques de producción abandonaron las puertas de la fábrica.
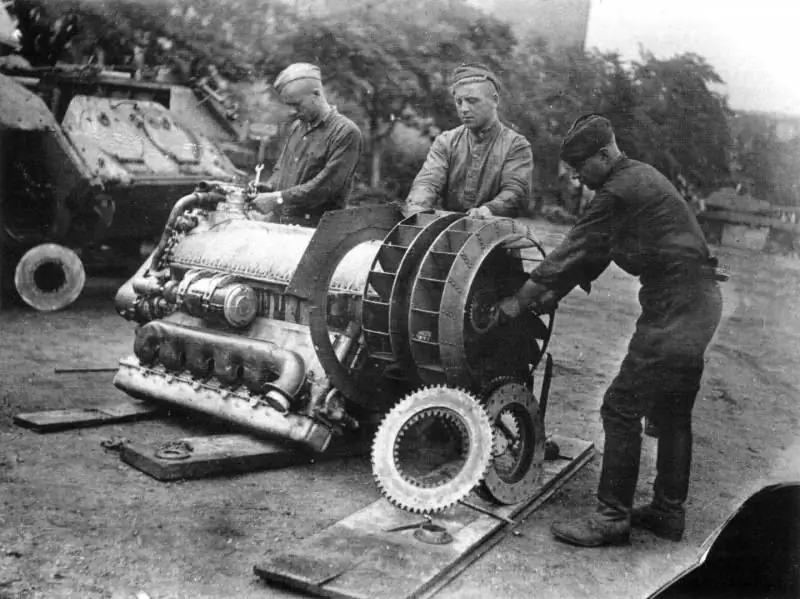
Composición química
¿Cuál fue la armadura enrollada 51C que se convirtió en la principal para el IS-2, ISU-122 e ISU-152? Es un acero de endurecimiento profundo para grandes espesores de armadura con la siguiente composición química (%):
C 0, 18-0, 24
Mn 0, 70-1, 0
Si 1, 20-1, 60
Cr 1, 0-1, 5
Ni 3.0-3.8
Lun 0, 20-0, 40
P ≤0.035
S ≤0,035.
En comparación con la armadura fundida 70L, el acero laminado 51C tenía una mayor proporción de molibdeno y níquel, lo que garantizaba un aumento de la templabilidad de hasta 200 mm. Cuando los cascos de los tanques pesados se dispararon con proyectiles de 88 mm, resultó que el blindaje de alta dureza era muy superior en durabilidad a sus predecesores de dureza media. El problema de colocar la armadura enrollada 51C se resolvió de inmediato.
Soldadura inteligente
Una importante contribución al éxito del desarrollo de la producción de blindaje de tanques de la serie IS se realizó mediante la soldadura automática de acero bajo una capa de fundente. Dado que era imposible transferir todo el proceso de fabricación de un casco blindado de tanque a dicha soldadura a principios de 1944, los ingenieros se enfocaron en automatizar las costuras más extendidas y cargadas mecánicamente.
En la planta No. 200 de Chelyabinsk, en el proceso de ensamblaje del casco del tanque pesado IS-2, solo se pudo automatizar el 25% de todas las soldaduras. A mediados de 1944, Tankograd pudo automatizar el 18% de todos los posibles 25% de las soldaduras. La longitud total de las costuras soldadas a lo largo del casco del tanque pesado IS-2 fue de 410 metros lineales, de los cuales 80 metros lineales se realizaron mediante el método de soldadura automatizado.
Este resultado ha generado importantes ahorros en los escasos recursos y la electricidad. Fue posible liberar hasta 50 soldadores manuales calificados (sus costos laborales en la cantidad de 15,400 horas-hombre) y ahorrar 48,000 kilovatios-hora de electricidad. Disminución del consumo de electrodos (alrededor de 20.000 kg, austenítico - 6.000 kg), oxígeno (en 1.440 metros cúbicos).
El tiempo dedicado a la soldadura también se ha reducido significativamente. Por ejemplo, soldar el fondo y la caja de la torreta a los lados con una costura de dieciséis metros tomó 9.5 horas-hombre en modo manual, y solo 2. Se requirió una costura similar en longitud que conectara la parte inferior a los lados del casco del tanque en modo automático. 3 horas-hombre (en el manual inmediatamente 11, 4). Al mismo tiempo, los soldadores altamente calificados podrían ser reemplazados por trabajadores no calificados en la soldadura automática.
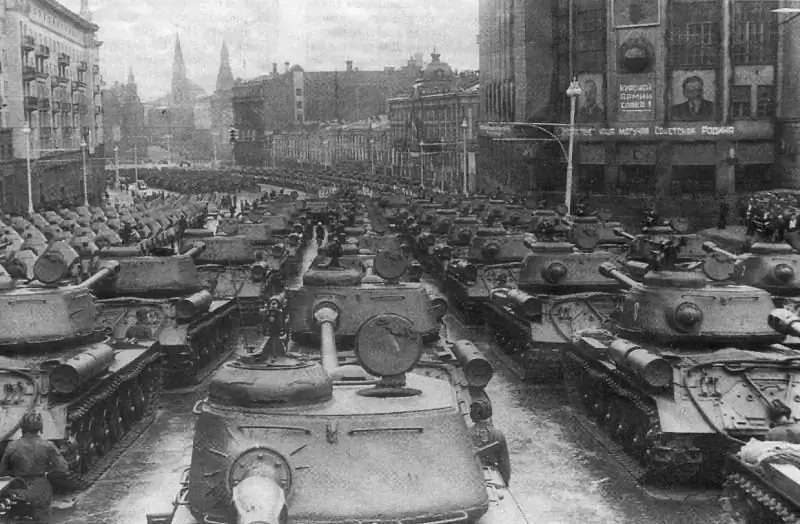
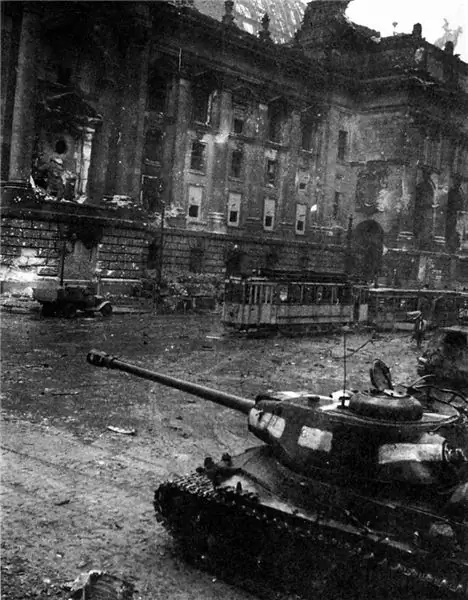
SAG de los Urales
Investigador de la industria de tanques soviéticos, candidato de ciencias históricas Zapariy Vasily Vladimirovich del Instituto de Historia y Arqueología de la Rama Ural de la Academia de Ciencias de Rusia en una de sus obras describe con gran detalle las unidades de soldadura automática utilizadas en los Urales para blindados producción de cascos.
El más extendido fue un rifle de asalto del tipo "ACC" con una cabeza Bushtedt. Había ocho instalaciones de este tipo en Uralmash. La velocidad de alimentación de alambre en esta máquina dependía del voltaje en el arco. Requería 5 unidades, incluyendo 3 motores eléctricos cinemáticos y 1 motor-generador.
A mediados de 1943, la máquina de soldar SA-1000 fue diseñada para las necesidades de los tanques pesados IS-2. O una máquina de soldar con una capacidad de hasta 1000 A.
Para dominar la producción de cascos blindados para el nuevo tanque pesado IS-3 de Chelyabinsk, los ingenieros de la planta diseñaron en 1944 el aparato "SG-2000". Esta máquina fue diseñada para trabajar con alambres de soldadura de bajo carbono con un diámetro aumentado (6-8 mm) y encontró su aplicación en la fabricación de la torre IS-3. La instalación contaba con un dosificador para introducir una composición especial (varias ferroaleaciones) en la sección de soldadura con el fin de desoxidar (restaurar) el metal en la misma. En total, según el principio de autorregulación del arco de soldadura en UZTM, en 1945, se crearon 9 instalaciones de autoldadura de tres tipos: "SA-1000", "SG-2000", "SAG" ("Soldadura automática cabeza").
Más hermosa que la armadura alemana
El resultado de toda la historia con el blindaje de los tanques IS pesados fue un desarrollo sorprendentemente rápido de una receta de acero que superó al blindaje alemán en sus propiedades tácticas. TsNII-48 recibió un acero endurecible de 120 mm, cuyo espesor, si es necesario, podría aumentarse a 200 mm.
Esto se convirtió en la base principal para el desarrollo de la familia de tanques soviéticos pesados de la posguerra.