El patriotismo de la élite industrial soviética se combinó con la responsabilidad conjunta del resultado final.
La interacción interindustrial en todo momento, tanto en el Imperio ruso como en la URSS y hoy, no perteneció a las fortalezas de la industria nacional. A diferencia de Alemania o Estados Unidos, donde las obligaciones contractuales tenían y tienen una fuerza inmutable y casi sagrada.
Tomemos, por ejemplo, la relación entre los metalúrgicos y los fabricantes de maquinaria rusos. En la segunda mitad del siglo XIX, las nuevas plantas de ingeniería de transporte y los astilleros no recibieron la cantidad requerida de metales industriales de los mineros de los Urales. Este último consideró que no era rentable fabricar una gran cantidad de productos laminados relativamente baratos, ya que el mismo beneficio se obtenía con un volumen mucho menor de costoso hierro para techos. El metal que faltaba para los ejes de los automóviles, los ejes de los motores y el revestimiento de los barcos tuvo que comprarse en el extranjero. Solo a finales de siglo, el problema fue resuelto por las plantas metalúrgicas del sur de Rusia, fundadas por industriales belgas o franceses. En los Urales, los franceses también construyeron una planta: Chusovskaya.
Parecería que en la época soviética, tales caprichos estaban fuera de discusión. Además, las plantas metalúrgicas construidas en los años 30 proporcionaron al país el metal en su conjunto. Sin embargo, cada vez que los fabricantes de maquinaria solicitaron nuevos tipos complejos de productos laminados, los metalúrgicos los dominaron durante años o incluso décadas.
Feudalismo departamental
Pasemos a la historia de Uralvagonzavod. Ya en sus primeros proyectos, estaba previsto utilizar ruedas de acero laminado sólido debajo de los coches de cuatro ejes a medida que la capacidad de diseño alcanzaba su capacidad de diseño, cuyo proveedor estaba previsto para la cercana planta metalúrgica de Novo-Tagil. Sin embargo, este último lo estaba construyendo el departamento metalúrgico, y pospuso la construcción del laminador de ruedas hasta 1938-1942, y no en primer lugar. Como resultado, el caso no comenzó antes de la guerra. Y después de la guerra, el alquiler de ruedas no interesó demasiado a los metalúrgicos. Resultado: hasta mediados de los años 50, los coches Tagil salían de fábrica con ruedas de hierro fundido de corta duración en lugar de con ruedas de acero. Esto trajo enormes pérdidas a los trabajadores ferroviarios, pero no había otra opción: esos coches o ninguno.
Lo mismo sucedió con la introducción de aceros de baja aleación en la construcción de carruajes. Prometieron una notable reducción del peso muerto del material rodante manteniendo todas las características de rendimiento. Los diseñadores de Uralvagonzavod comenzaron a diseñar automóviles hechos de metal de baja aleación a fines de los años 30, pero su producción en serie comenzó solo en la segunda mitad de los años 50, ya que los metalúrgicos no proporcionaban productos laminados ni ferroaleaciones adecuados para las piezas de fundición.
Hay que decir que el virus del feudalismo departamental afectó a los propios constructores de maquinaria. En el verano de 1937 tuvo lugar una interesante historia que caracterizó las relaciones interinstitucionales de esa época. La Dirección General de Empresas Metalúrgicas envió a Uralvagonzavod un pedido de cinco mil toneladas de espacios en blanco para la fábrica de vendajes recién inaugurada de la Planta Novo-Tagil. La Dirección Principal de Ingeniería de Transporte estaba indignada por la usurpación de una empresa subordinada. Subjefe de la Dirección General G. G. El 11 de julio, Aleksandrov envió una carta a GUMP y Uralvagonzavod con la siguiente declaración: “Estamos extremadamente sorprendidos de que la solución de un tema tan importante como la organización de la producción de un vendaje en blanco en Uralvagonzavod se haya llevado a cabo sin nuestra participación, y más aún - Ni siquiera nos enviaron una copia del atuendo enviado a Uralvagonzavod … Les pido que establezcan un procedimiento firme para la entrega de espacios en blanco a nuestras fábricas sólo mediante un acuerdo con nosotros ya través de Glavtransmash.
Como resultado, a los metalúrgicos se les negó el acero para vendas, supuestamente debido a la imposibilidad técnica de fundir lingotes de alta calidad en el taller de hogar abierto de Uralvagonzavod. Mientras tanto, ya en 1936, aquí se fundió una pieza en bruto axial, y en 1937, lingotes para laminado de láminas. Por lo tanto, los lingotes para el molino de mortaja, ubicado a pocos kilómetros de UVZ, tuvieron que ser transportados desde las plantas de Vyksa y Kuznetsk. Además, su calidad dejaba mucho que desear y los volúmenes de suministros eran insuficientes.
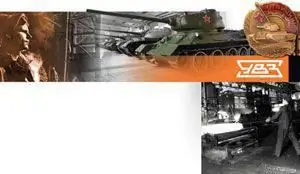
En 1938, la historia se repitió. El principal consumidor de lingotes de UVZ fue la Planta de Artillería Molotov (es decir, Perm), que recibió un lote de piezas en bruto a finales de año. Y solo un pequeño número de ellos fue a la tienda de vendajes, que nuevamente tuvo que importar el metal faltante durante dos o dos mil quinientos kilómetros. Los intereses de la industria en la distribución del acero de Uralvagonzavodsk prevalecieron claramente.
Las enfermedades departamentales tampoco perdonaron a la industria de defensa. Numerosas publicaciones sobre la historia de la construcción de tanques soviéticos están francamente repletas de ejemplos de cómo la construcción de prototipos o el despliegue de la producción en masa se retrasó debido a la falta de entrega de metal, especialmente armaduras.
Y aún hoy el interés propio sectorial no ha ido a ninguna parte, solo ha cambiado de forma. Las solicitudes de nuevas formas de productos laminados simplemente se rechazan con precios exorbitantes. No es necesario hablar de una política coordinada. Después del colapso del tipo de cambio del rublo a finales de 2014-2015, las empresas metalúrgicas aumentaron los precios del material rodante entre un 30% y un 60%. E inmediatamente comenzaron a quejarse de los fabricantes de máquinas por el equipo que había subido de precio; después de todo, las máquinas se producen en Rusia y no están atadas al tipo de cambio del dólar.
Parece que en nuestro país solo existe una cura para los problemas intersectoriales: la creación de sistemas integrados verticalmente, donde el mineral extraído por nuestras propias fuerzas se convierte primero en metal y luego en máquinas terminadas.
Unidad en tiempos de guerra
Sin embargo, hay un breve período en nuestra historia en el que los intereses de la industria han pasado a un segundo plano. Estamos hablando de la Gran Guerra Patria. El indudable patriotismo de la élite industrial soviética en ese momento se combinó con la responsabilidad conjunta de todos los involucrados en la producción de defensa por el resultado final. Es decir, el director de la planta de laminación blindada era responsable no tanto del volumen de acero fundido y laminado, sino de la cantidad de tanques construidos.
El principal paso en esta dirección fue el director de NII-48 A. S. Zavyalov. En los primeros días de la guerra, se dirigió al gobierno con una propuesta para instruir al instituto para que introdujera tecnologías para la producción de aceros especiales y estructuras blindadas en empresas del este del país, que participaron por primera vez en la fabricación de blindados. vehículos. A principios de julio, equipos de especialistas de NII-48 encabezaron la reestructuración tecnológica de 14 empresas más grandes. Entre ellas se encontraban las plantas metalúrgicas de Magnitogorsk y Kuznetsk, las plantas metalúrgicas de Novo-Tagil y Chusovka, la planta de construcción de maquinaria pesada de los Urales, la planta de tractores Gorky Krasnoye Sormovo, la planta de tractores de Stalingrado, el octubre rojo de Stalingrado y el número 264. Por lo tanto, Zavyalov violó la tabú de antes de la guerra: la lista incluía empresas de tres comisarías populares.
El patriotismo y la supresión obligatoria del egoísmo departamental proporcionaron a la metalurgia soviética tasas de desarrollo de productos de defensa sin precedentes, ni en la preguerra ni en la posguerra. En cuestión de meses, en el este del país (principalmente en los Urales), se organizó la producción de ferromanganeso, ferrosilicio, ferrocromo, ferrovanadio y otras aleaciones, sin las cuales es imposible obtener acero blindado. Después de la pérdida de las regiones occidentales, Chelyabinsk siguió siendo la única planta de ferroaleaciones en la URSS. En él, en poco tiempo, la fundición se incrementó dos veces y media. Se produjeron 25 tipos de productos, pero la mayoría eran de varios tipos de ferrocromo. La fundición de ferromanganeso se estableció en altos hornos, y no solo en altos hornos viejos de bajo tonelaje de las plantas de Nizhniy Tagil y Kushvinsky, sino también en un gran horno moderno de la cosechadora Magnitogorsk. Contrariamente a todas las ideas de antes de la guerra, el ferrocromo fue fundido en la segunda mitad de 1941 en sus altos hornos por los metalúrgicos de las plantas de Nizhniy Tagil y Serov, y los científicos de la rama de los Urales de la Academia de Ciencias de la URSS brindaron una gran ayuda para crear un nuevo tecnología. Posteriormente, se dominó la fundición de ferrosilicio en los altos hornos de Serov.
No había campos blindados ni en los Urales ni en Siberia Occidental antes de la guerra, tuvieron que ser trasladados apresuradamente desde empresas que estaban en la zona de combate.
En el verano de 1941, el equipo evacuado todavía estaba en tránsito. Y luego, el mecánico jefe de Magnitogorsk Combine N. A. Ryzhenko sugirió enrollar la armadura en un molino floreciente. A pesar del gran riesgo, la idea se llevó a cabo. Y en octubre entró en servicio un campamento blindado, sacado de la planta de Mariupol. Se montó en solo 54 días. De acuerdo con los estándares de antes de la guerra, esto tomó un año.
La planta de Novo-Tagil obtuvo el campamento de Leningrado. Los preparativos para su admisión comenzaron en julio, inicialmente se asumió que se montaría en el sitio del vendaje. El campamento de vendajes se desmontó, pero resultó que las existencias viejas no eran suficientes para instalar el campamento blindado y tuvieron que colocarse en otro lugar. La guerra obligó a hacer lo que se consideraba imposible hasta hace poco: hace apenas un año, los intentos de llevar a cabo la construcción industrial mediante un método integrado de "alta velocidad" en Nizhny Tagil tuvieron, en el mejor de los casos, un éxito parcial, y en el verano de 1941 La compleja operación de construcción fue casi perfecta. El 10 de septiembre, se laminó la primera chapa de acero Tagil un mes antes de lo previsto. En total, al final del año, se obtuvieron 13,650 toneladas de chapa metálica, incluido alrededor del 60 por ciento de armadura (la fábrica se probó en acero al carbono, y en octubre-diciembre, se laminó acero al carbono con escasez de lingotes de armadura). Como resultado, ya en enero de 1942, la producción mensual de placas de blindaje en las fábricas de los Urales superó los seis meses en toda la Unión Soviética de antes de la guerra.
Eventos no menos sorprendentes tuvieron lugar en otras empresas poco conocidas. Durante la guerra, la planta metalúrgica de Zlatoust era inferior a la cosechadora Magnitogorsk en términos de volumen de acero laminado y fundido, pero la superó significativamente en su mezcla de productos: aquí se produjeron alrededor de 300 grados de aleación y acero al carbono. Sin los suministros de Zlatoust, la producción de muchos tipos de armas, principalmente motores de tanque, se habría detenido.
Las antiguas fábricas de los Urales demostraron ser indispensables en la producción de pequeños lotes de acero especialmente de alta calidad. Por ejemplo, en todos los tanques soviéticos se invirtió metal de Serov Metallurgical, el principal fabricante de productos laminados calibrados. La planta de Nizhnesalda pasó a la fundición de níquel, hierro y acero. Esta lista puede continuar interminablemente: durante los años de la guerra, donde había al menos una cúpula, se derretía metal apto para armas.
Existe una historia curiosa con los fundentes para soldadura automática. Antes y al comienzo de la guerra, se fundieron en una de las empresas de Donbass, después de la ocupación de la cual los suministros centralizados cesaron por completo. A finales de 1941, los empleados del Instituto de Soldadura Eléctrica de la Academia de Ciencias de la República Socialista Soviética de Ucrania comenzaron a buscar materiales sustitutos disponibles en los Urales en condiciones más o menos utilizables. Y los encontraron, en forma de escorias de alto horno de la planta metalúrgica Ashinskiy. Solo se requirieron pequeñas mejoras: los altos hornos enriquecieron sus escorias con manganeso y, por lo tanto, las convirtieron en un fundente completamente adecuado. El equipo necesario para las pruebas se trajo de Nizhny Tagil directamente a Asha.
Los ejemplos de cooperación local entre tanques y plantas metalúrgicas son muy indicativos. Antes del lanzamiento de sus propias instalaciones, en la Planta Metalúrgica de Nizhniy Tagil se llevó a cabo el tratamiento térmico de las partes de los tanques de la Planta de Tanques Ural No. 183.
El trabajo exitoso de los trabajadores de la fundición de UTZ se vio facilitado en gran medida por la asistencia de la planta de arcilla refractaria vecina de Nizhniy Tagil, que estableció la producción de tapones de piedra refractaria de alta calidad. Esto hizo posible realizar una fundición sin problemas de fundiciones de acero de armadura pesada para fundición moldeada.
En 1942-1945, los hornos de hogar abierto en UTZ funcionaban principalmente con horno de coque y gas de alto horno de las plantas de coque de Novo-Tagil Metallurgical y Nizhniy Tagil. El gasoducto está en funcionamiento desde febrero de 1942. La propia estación generadora de gas de la Planta No. 183 cubrió no más del 40 por ciento de las necesidades.
A veces, un simple consejo era suficiente para resolver un problema. La información de los metalúrgicos locales sobre una pequeña mina de manganeso desarrollada en la década de 1870 ayudó a sobrevivir varias semanas antes del inicio de las entregas de ferromanganeso sin detener la fundición de las orugas de los tanques.
Otro ejemplo: a medida que aumentaba la producción de acero blindado, el taller de hogar abierto ya no podía seguir el ritmo de la fundición de metal para las cabezas de las bombas aéreas. No fue posible conseguirlo desde el exterior. El director Yu. E. Maksarev recordó el curso de otros eventos en sus memorias: “Cuando estaba en una de las reuniones del comité de la ciudad, conocí al director de la antigua planta de Demidov y le pedí que me quitara el casting de las cabezas de la bomba. Dijo: No puedo ayudar con el acero, pero con un consejo ayudaré. Y cuando llegué a su planta, me mostró un convertidor Bessemer de una tonelada y media con soplado medio. Me dio los dibujos y dijo que sabe que tenemos una buena fundición de hierro mecanizado y que sus convertidores soldarán”. Así apareció el pedido de la planta del 8 de septiembre de 1942 sobre la organización en el taller de ruedas Griffin de la sección Bessemer de tres pequeños convertidores (una tonelada y media de metal cada uno). Para el 25 de septiembre, el proyecto fue preparado por el departamento de diseño y tecnología de la gerencia de construcción de capital, los especialistas del departamento del jefe de mecánicos soldaron rápidamente convertidores y calderas: tanques de almacenamiento de hierro líquido. La prueba de funcionamiento del departamento de Bessemer y la fundición de un lote experimental de cinco nombres de piezas tuvieron lugar a finales de octubre-noviembre de 1942. La producción en serie comenzó a finales de noviembre.
Al final del tema: la cooperación de los metalúrgicos y los constructores de tanques en tiempos de guerra actuó en ambas direcciones. Los instaladores de la Planta de Tanques de los Urales participaron en la puesta en servicio de muchas unidades nuevas de la Planta Metalúrgica de Novo-Tagil. En mayo de 1944, en el taller de fundición de la torre blindada se fabricó un número significativo de placas de revestimiento para la reparación del alto horno.
Pero el asistente principal de los metalúrgicos fue, por supuesto, la Planta de Construcción de Maquinaria Pesada de los Urales. Los libros de pedidos de UZTM para 1942-1945 están literalmente repletos de documentos sobre la producción de repuestos y dispositivos para fines metalúrgicos, tanto para las necesidades de la industria de tanques como para las empresas del Comisariado Popular de Metalurgia Ferrosa. En el otoño de 1942, se restauró oficialmente en UZTM una división especial para la producción de equipos para plantas metalúrgicas. Recibió el código "División 15" y estaba subordinado al subdirector de tiendas de aprovisionamiento y producción de cascos.
Éxito en la intersección de industrias
La cooperación de los metalúrgicos y los constructores de tanques ha llevado a la creación de una serie de tecnologías que, sin exagerar, pueden llamarse verdaderos avances científicos y técnicos.
Habiendo fundido y laminado el acero blindado en láminas, los metalúrgicos transfirieron sus productos a la producción de cascos blindados. Aquí, el metal se cortó de acuerdo con la plantilla en las partes correspondientes. En la producción del "treinta y cuatro" especialmente, dos partes del casco causaron muchos problemas: los guardabarros (el lado inclinado del costado) y la placa lateral vertical. Ambos eran tiras largas, incluso de ancho, con cortes oblicuos a lo largo de los bordes.
La idea, naturalmente, se sugirió en sí misma para enrollar una tira de medición del mismo ancho que las piezas terminadas. Fue formulado por primera vez por los vehículos blindados de la planta de Mariupol en el verano de 1941. Para la laminación de prueba, elegimos un laminador de desbastes en Zaporizhstal, donde se enviaron dos escalones de lingotes de blindaje. Pero luego no tuvieron tiempo de ponerse manos a la obra: las tropas alemanas que avanzaban capturaron tanto los escalones como el propio Zaporozhye.
A la vuelta de 1941-1942, durante la evacuación y el desarrollo de la producción de armaduras en las nuevas fábricas, no había suficientes rayas. Sin embargo, en mayo de 1942, el Comisariado Popular de Metalurgia Ferrosa recibió nuevamente un pedido para alquilarlo para tanques T-34 y KV. La tarea resultó ser difícil: las tolerancias en ancho no deben exceder -2 / + 5 milímetros, la forma de media luna (curva) para la longitud total de la pieza fue de 5 milímetros. No se permitieron grietas, atardeceres y delaminación en los bordes para que la soldadura se pudiera realizar sin mecanizar ni cortar con llama.
El trabajo experimental comenzó simultáneamente en los talleres de laminación de las plantas metalúrgicas de Magnitogorsk y Kuznetsk, al principio sin ningún logro particular. El alquiler de piezas para los tanques KV pronto se abandonó, pero el T-34 finalmente tuvo éxito. El equipo de autores formado por el jefe del departamento metalúrgico de la NII-48 G. A. Vinogradov, el ingeniero jefe de la KMK L. E. Vaisberg y el ingeniero de la misma planta S. E. stands "900" del molino de rieles y estructuras es un completamente nuevo método de rodar "en el borde". En enero de 1943, se emitieron 280 tiras, en febrero - 486, en marzo - 1636 piezas. En abril, después de todas las pruebas requeridas, comenzó el desarrollo de la producción bruta de tiras de medición para los revestimientos de los pasos de rueda de los tanques T-34. Inicialmente, se suministraron a UZTM y la planta de tanques de Ural, y luego a otras fábricas: fabricantes de tanques T-34. La chatarra, que originalmente era del 9,2 por ciento, se había reducido al 2,5 por ciento en octubre de 1943, y las tiras de calidad inferior se utilizaron para fabricar piezas más pequeñas.
Una evaluación completa y precisa de la nueva tecnología se da en el informe correspondiente de TsNII-48 con fecha del 25 de diciembre de 1943: “Se desarrolló, probó e introdujo en la producción bruta un método fundamentalmente nuevo de enrollar una banda ancha blindada“en el borde”., que hasta hace poco se consideraba inviable en la URSS y en el extranjero. La obtención de una tira calibrada (medida) con un ancho de la parte acabada del casco blindado del tanque T-34 hizo posible que las fábricas de NKTP adoptaran una nueva tecnología de alto rendimiento para la fabricación de piezas blindadas sin cortar bordes longitudinales. Gracias a la aplicación del nuevo método a una de las principales partes blindadas del tanque T-34 (guardabarros), se logró un ahorro de tiempo muy significativo (alrededor del 36%) al cortarlos. Se logró un ahorro de acero blindado 8C de hasta un 15 por ciento y un ahorro de oxígeno de 15.000 metros cúbicos por cada 1.000 cascos”.
A fines de 1943, se dominó el balanceo de una tira de medición para otra parte del casco del T-34: la parte vertical del costado. Solo queda agregar que los autores de esta invención fueron galardonados con el Premio Stalin de 1943.
En el mismo 1943, gracias a los esfuerzos conjuntos del laboratorio del Instituto Ucraniano de Metales (encabezado por PA Aleksandrov) y los trabajadores de la Cosechadora Metalúrgica Kuznetsk y la Planta de Tanques Ural, se desarrolló un perfil laminado periódico especial y se dominó en la producción para la adquisición. de masa y partes críticas de los "treinta y cuatro" - ejes equilibradores. El primer lote experimental de un perfil periódico se recibió en KMK en diciembre, a principios de 1944 comenzó la producción en serie. En octubre, la Planta de Tanques de Ural cambió por completo a la fabricación de ejes equilibradores a partir de una nueva pieza en bruto, al final del año UZTM se unió a ella. Como resultado, la productividad de los martillos de forja aumentó en un 63 por ciento y el número de roturas de piezas disminuyó.
El trabajo exitoso de los constructores de tanques se vio facilitado en gran medida por el material rodante del laminador de vendajes de la Planta Metalúrgica de Novo-Tagil. A partir de la primavera de 1942, suministraron correas de hombro enrolladas con asignaciones de mecanizado reducidas, en 1943 las asignaciones se redujeron nuevamente. En combinación con la nueva herramienta de corte, esto hizo posible llevar a cabo el pelado de las correas de los hombros, que consumía mucho tiempo, estrictamente en el cronograma y sin mucho estrés. Un caso raro: el Comisario Popular de la Industria de Tanques V. A. Malyshev, en su orden del 28 de septiembre de 1943, consideró necesario expresar un agradecimiento especial a los metalúrgicos de Tagil.
Y finalmente, el último ejemplo: en 1943, las llantas de los tanques de apoyo T-34, primero en la planta de Chelyabinsk Kirov y luego en otras empresas, comenzaron a fabricarse a partir de productos laminados perfilados especiales. Este éxito también se observó en el orden de V. A. Malyshev.
Queda por agregar que los especialistas de la compañía estadounidense "Chrysler", después de estudiar el tanque T-34-85 capturado en Corea, notaron especialmente la perfección de los espacios en blanco de acero con los que se fabricó el vehículo de combate. Y también el hecho de que a menudo superaban en número a los productos de las empresas metalúrgicas estadounidenses.